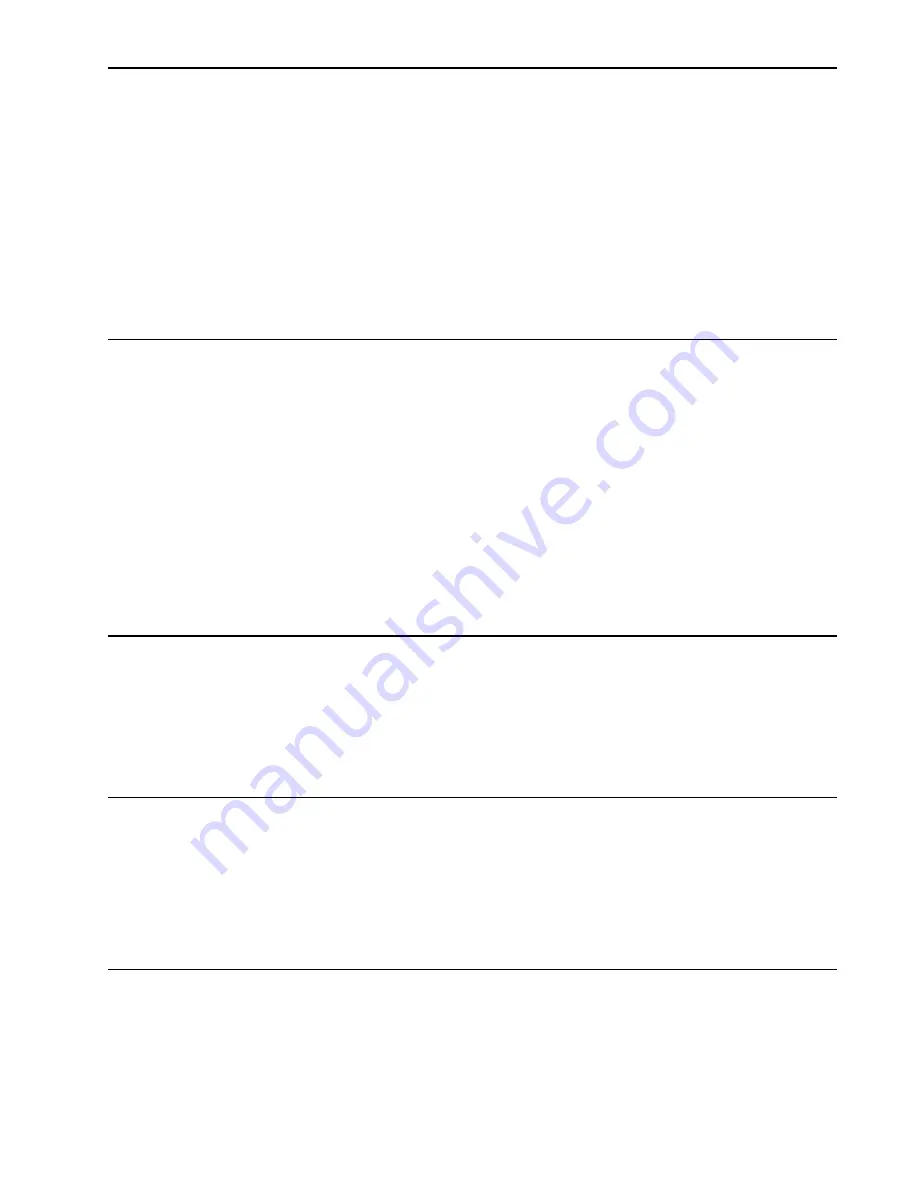
60
...cont.
1. Modulating Valve does
not open
or correct wiring problem as required. Test each sensor lead for continuity to ground. If continuity is
confirmed, replace sensor.
2. FAILSF Error Message
This error message shows whenever the controller goes into a failsafe mode of operation. This will
happen if the controller fails to pass its memory test, configuration tests, or calibration test. Return
controller to the factory for analysis.
3. IN1FAIL Error Message
Controller has detected two consecutive failures of the input signal. Check for shorted or open sen-
sor condition as listed above.
4. No temperature display
Check for 120vac power on controller terminals L1 and L2.
Check to see that Main shutoff valve is open and fire has ignited.
Check that controller set point is higher than ambient temperature.
Check plenum controller for error messages displayed. See above section concerning mes-
sages.
Check for 4-20ma signal between terminals 4 and 5 of plenum controller (you must remove
wires from terminals to make measurement). If no signal, replace controller. If 4ma is measured and
does not increase, check controller part number to be certain the correct controller has been installed.
Check inside main shutoff valve for properly operating auxiliary valve switch. (Continuity
between wires 83 and 81 when valve is open)
Check inside Modulation Valve for 120VAC power to the black and white wire. Temporarily
jumper terminals F and + or F and - and observe action. Motor should drive fully open. If no modula-
tion action occurs, replace motor.
Check for 4-20ma signal on wires 80 and 81 attached to ter and - of modulation valve
(you must remove wires from terminals to make measurement). If no problems detected, replace
Modulation Valve.
P L E N U M T E M P E R A T U R E C O N T R O L
2. Plenum temperature
does not stabilize
Check that valve linkage works freely
Check that linkage has been adjusted properly. (see start-up and testing section.
Check for proper pressure regulator adjustment. See fuel specifications in Table 2-1. Reducing
regulator pressure from settings listed in Fuel Specifications Charts when operating at lower than nor-
mal plenum temperatures, with reclaiming, or in warm ambient conditions will help reduce overshoots
and improve modulation stability.
Inadequate fuel supply or regulator operation will cause supply pressure (gage on shutoff valve)
to drop as modulation valve opens causing unstable temperatures.
4. Plenum temperature
does not reach set point
temperature
Check for too low of a regulator pressure setting and/or inadequate fuel supply.
Check that the Modulating motor has stroked fully open (from 12:00, closed position to 3:00,
open position)
Check that the modulation valve linkage has been properly adjusted per instructions in start-up
and testing. When fully open, the gage pressure on the Shutoff valve and the gage upstream of but-
terfly valve should be nearly equal.
Check for water in vertical manifold pipe.
Check for obstruction at main burner orifice
Check for plugged burner orifices (0.086 dia holes)
3. Plenum temperature
severely overshoots set
point temperature
It is normal to briefly overshoot temperature 10-20°F on start-up. Controller should settle in to
temperature in a few minutes.
Check that the pressure regulator pressures have been set properly. Reducing regulator pres-
sure from settings listed in Fuel Specifications Charts when operating at lower than normal plenum
temperatures, with reclaiming, or in warm ambient conditions will help reduce overshoots and improve
modulation stability.
If plenum temperature stabilizes at a point higher than the set point with the modulation valve
closed, low fire setting may be too high. Adjust linkage for minimum fire as discussed in start-up and
testing section.
TROUBLE
CHECKOUT PROCEDURE & INFORMATION
Summary of Contents for C-21100B
Page 22: ...20 ...
Page 36: ...34 Fig 6 3 LP vaporizer assembly Fig 6 4 ASC control panel ...
Page 49: ...Fig 8 1 Power circuit 220V 3 PH for C 2130B C 2140B C 2160B only 47 4B0280A TIF ...
Page 50: ...48 Fig 8 2 Power cirucit 220V Part wind start for C 2175B C 21100 models only 4B0280C TIF ...
Page 51: ...49 Fig 8 3 Power circuit 440V 3 PH for all C 2100B models 4B0280B TIF ...
Page 52: ...Fig 8 4 Control circuit all models except part wind start p 1 of 3 50 4B0280D TIF ...
Page 53: ...Fig 8 4 Control circuit all models except part wind start p 2 of 3 51 4B0280E TIF ...
Page 55: ...Fig 8 5 Control circuit part wind start models only p 1 of 3 53 4B0280H TIF ...
Page 56: ...Fig 8 5 Control circuit part wind start models only p 2 of 3 54 4B0280I TIF ...
Page 58: ...Fig 8 6 Safety circuit portion of control circuit all models 56 4B0280G TIF ...
Page 65: ......