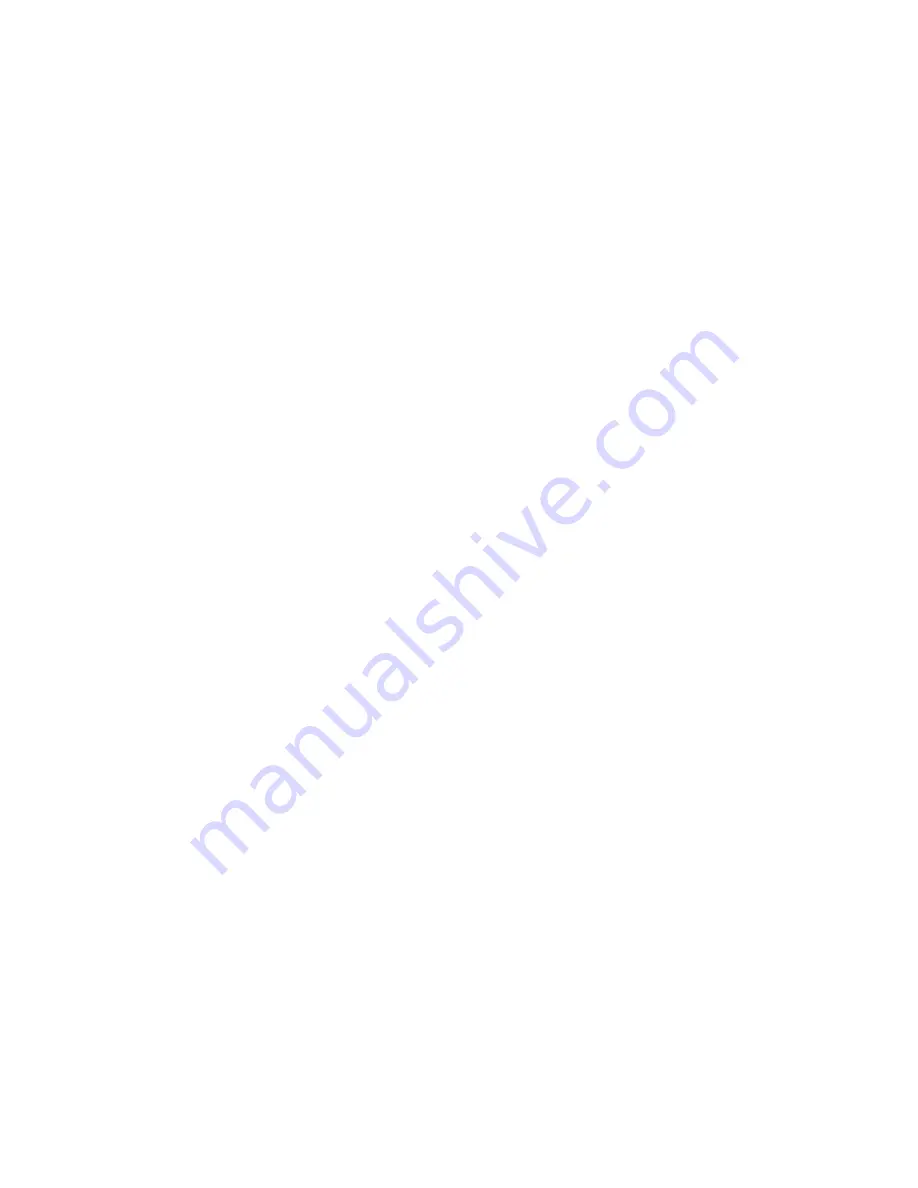
43
14.Inspect that all dryer guards and warning decals are in
place and securely installed. Make certain guards do
not interfere with moving parts.
15. Test fire the dryer several weeks ahead of the drying
season. Include a check for possible gas leaks. At the
beginning of each drying season, remove 2" pipe cap
from water trap located at bottom of vertical fuel pipe to
remove accumulation of condensation before firing
burner.
See Section 4 - TEST FIRING for suggested testing
procedure.
PROPANE VAPORIZER SEASONAL
INSPECTION
LIQUID PROPANE MODELS ONLY - Liquid propane
fueled dryers are equipped with a vaporizer that oper-
ates at relatively high pressure. Since leakage can
result in release of liquid propane, it is extremely impor-
tant to maintain the condition of all components to pro-
vide safe operation. Vaporizers should be inspected
and serviced prior to each season of operation, includ-
ing the following:
1. Carefully inspect the surfaces of the vaporizer coil and
the liquid inlet and vapor outlet pipes for evidence of
severe corrosion or abrasion of metal which could
cause subsequent leakage of liquid propane, gross
overheating, and fire hazard.
Insecure mounting of either the vaporizer or its plumb-
ing due to loosened bolts can cause erosion of the pipe
metal at the point of maintained contact. If there has
been significant abrasion of the steel vaporizer pipe, it
must be replaced.
2. Inspect the fuel train components: Liquid solenoid
valve, pressure relief valves, pressure regulator, Vapor
Hi-limit Thermostat, and the fuel lines and fittings.
VAPORIZER ADJUSTMENT
LIQUID PROPANE MODELS ONLY - After initial instal-
lation and occasionally during the drying operation,
check the temperature of the gas line between the
pressure regulator and the fuel manifold assembly.
ALLOW HEATER TO OPERATE AND STABILIZE
TEMPERATURES BEFORE MAKING THIS CHECK.
See Fig. 6-3.
NOTE:
If the gas temperature exceeds 220°F, the
Vapor Hi-limit thermostat will open the electrical circuit
to the liquid solenoid valve and shut off fuel flow to
heater, thereby causing automatic shutdown of the
dryer.
If the gas line is very cold or "frosted," move the vapor-
izer slightly closer to the flame. If gas line is too hot to
touch, move vaporizer slightly away from the flame.
NOTE: High vaporizer temperatures may be caused by
fuel vaporizing before reaching the vaporizer. Check
for:
A.
Improper fuel hookup. Should be drawing liquid
from tank.
B.
Frosted lines, fittings or valves. Frost indicates a
restriction or pressure drop in piping, causing vaporiza-
tion.
RE-ZEROING THE VACUUM GAUGE
The pressure gauge was zeroed at the Farm Fans fac-
tory prior to shipment. When the dryer is shut down,
the gauge should return to a zero reading. Over time,
however, the gauge may drift out of calibration. If this
occurs, re-zero using the following process:
1. Unscrew the gauge cover by placing the palm of your
hand over the lens and turning counterclockwise.
2. The zero adjust screw is located behind the scale at the
point marked "zero." Using a small hex Allen wrench,
adjust until the needle reads zero. Turning clockwise
increases the reading, and counterclockwise decreas-
es.
3. Reinstall the gauge cover.
GRAIN AND PLENUM TEMPERATURE
SENSORS
Fig. 6-6 shows locations of the following sensors:
Hi-limit temperature sensors in both right and left grain
columns are designed to open the safety circuit and
cause a dryer shut-down if a temperature exceeding
210°F is sensed.
A plenum hi-limit temperature sensor mounted in the
plenum is designed to open the safety circuit and
cause a dryer shut-down if a temperature exceeding
300°F is sensed.
An RTD plenum sensor supplies a resistance signal to
the Plenum Temperature Control Unit on the ASC
panel.
An RTD grain sensor supplies a resistance signal to
the Moisture Control Unit on the ASC panel.
SCR DRIVE AND METER ROLL
INFORMATION
SCR DRIVE - GENERAL INFO.
The meter rolls (which regulate the rate of grain flow
through the dryer) are driven by a separate DC type
electric motor. The DC motor speed is variable and is
controlled by an electronic SCR type (silicon controlled
rectifier) control located within the ASC control box.
See Table 1-4 for SCR system specifications.
The main SCR components are the SCR control board
assembly, DC motor, and speed reducer gear box.
These parts are briefly described as follows:
1. SCR SPEED CONTROL - The Manual Control Dial on
the ASC control panel regulates the SCR control
board, to control the speed of the DC motor which dri-
ves the meter rolls.
2. DC ELECTRIC MOTOR - The 1/3 HP direct current
(DC) motor provides the drive for the meter rolls and is
located on the rear left-hand side of the Dryer (except
on special front discharge models). The motor powers
the gearbox through a V-belt drive arrangement. The
Summary of Contents for C-21100B
Page 22: ...20 ...
Page 36: ...34 Fig 6 3 LP vaporizer assembly Fig 6 4 ASC control panel ...
Page 49: ...Fig 8 1 Power circuit 220V 3 PH for C 2130B C 2140B C 2160B only 47 4B0280A TIF ...
Page 50: ...48 Fig 8 2 Power cirucit 220V Part wind start for C 2175B C 21100 models only 4B0280C TIF ...
Page 51: ...49 Fig 8 3 Power circuit 440V 3 PH for all C 2100B models 4B0280B TIF ...
Page 52: ...Fig 8 4 Control circuit all models except part wind start p 1 of 3 50 4B0280D TIF ...
Page 53: ...Fig 8 4 Control circuit all models except part wind start p 2 of 3 51 4B0280E TIF ...
Page 55: ...Fig 8 5 Control circuit part wind start models only p 1 of 3 53 4B0280H TIF ...
Page 56: ...Fig 8 5 Control circuit part wind start models only p 2 of 3 54 4B0280I TIF ...
Page 58: ...Fig 8 6 Safety circuit portion of control circuit all models 56 4B0280G TIF ...
Page 65: ......