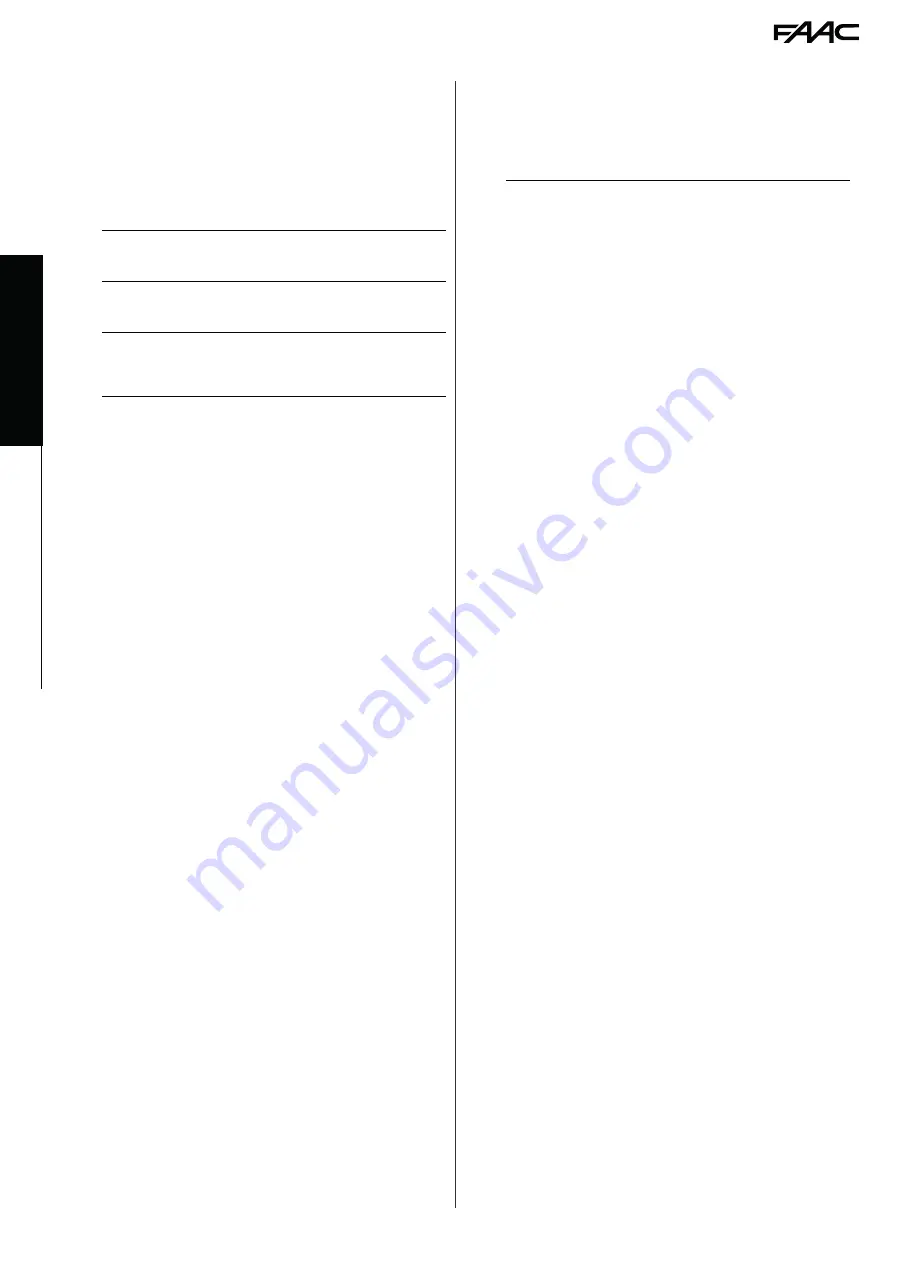
J275 HA 2K20
9
532270 - Rev.A
Tr
ansla
tion of the original instruc
tions
ENGLISH
4. INSTALLATION REQUIREMENTS
4.1 MECHANICAL REQUIREMENTS
The essential mechanical requirements for each bollard are as follows:
-
a pit as indicated in the foundation diagram
-
a flexible conduit suitable for electrical connections
-
a cage and foundation plinth
-
flat ground
The foundation diagram is supplied with the pit and shows a double
unit installation. For information about the foundation diagram for a
multiple bollard configuration, please contact FAAC technical support.
4.2 ELECTRICAL SYSTEM
F
Always shut off the power supply before performing any work.
If the
disconnect switch is not in view, apply a warning sign stating “WARN-
ING - Maintenance in Progress”.
!
The electrical system must comply with applicable legislation in the
country of installation. In Europe, the electrical system must comply
with standard EN 60335.
Use components and materials with a CE marking that are compli-
ant with the Low Voltage Directive 2014/35/EU and EMC Directive
2014/30/EU.
The electrical cables of the system must be of a size and insulation class
that is compliant with current legislation and laid in appropriate rigid
or flexible conduits, either above or below ground.
The automation power supply for each bollard must be fitted with:
- a multi-pole thermal magnetic circuit breaker, with a suitable tripping
threshold, a contact opening distance of at least 3 mm and a breaking
capacity that complies with current regulations
- a 0.03 A differential switch
The thermal magnetic and differential circuit breakers must be located
in areas that are only accessible to authorized personnel.
The metal parts of the structure must be earthed.
Check that the protective earthing system complies with applicable
regulations in the country of installation.
Provide the following for each bollard:
- an FG7OR-0.6/1kV-16G1.5 cable, maximum length 50 m. This code
refers to European standards and describes a cable with ethylene
propylene rubber insulated conductors, PVC outer sheath, nominal
voltage 0.6 kV, maximum voltage 1 kV, 16 conductors, one of which is
an earth, section of conductor 1.5 mm
2
Provide an electronic board for every three bollards.
Provide suitable enclosures for the installation of electronic boards and
electrical components. The containers must have a minimum IP44
protection and must be fitted with a lock or other device to prevent ac-
cess by unauthorized persons. The cable outlets must face downwards.
In the case of a Master-Slave configuration, a cable conduit has to be
installed for the cables that connect the two electronic boards.
Check buried cable plans to ensure that there are no other electrical
cables in proximity to the planned digging/drilling locations to prevent
the risk of electrocution.
Check that there are no pipes in the vicinity as well.
The conduit fittings and the cable glands must prevent the entry of
moisture, insects and small animals.
Protect extension cable connections using junction boxes with an IP67
protection rating or higher.
The bollard must always be visible to prevent it from being hit ac-
cidentally. An adequate lighting system is required.
It is recommended to position the control devices within the field of
view of the automation. This is mandatory in the case of hold-to-run
controls.
The maintained action controls in the hold-to-run mode of operation,
must comply with standard EN 60947-5-1.
The control devices must be located in areas that are only accessible
to authorized personnel.
If an emergency stop button has been installed, it must be EN13850
compliant.
Comply with the following heights from the ground:
- control accessories = minimum 150 cm
- emergency button = maximum 120 cm