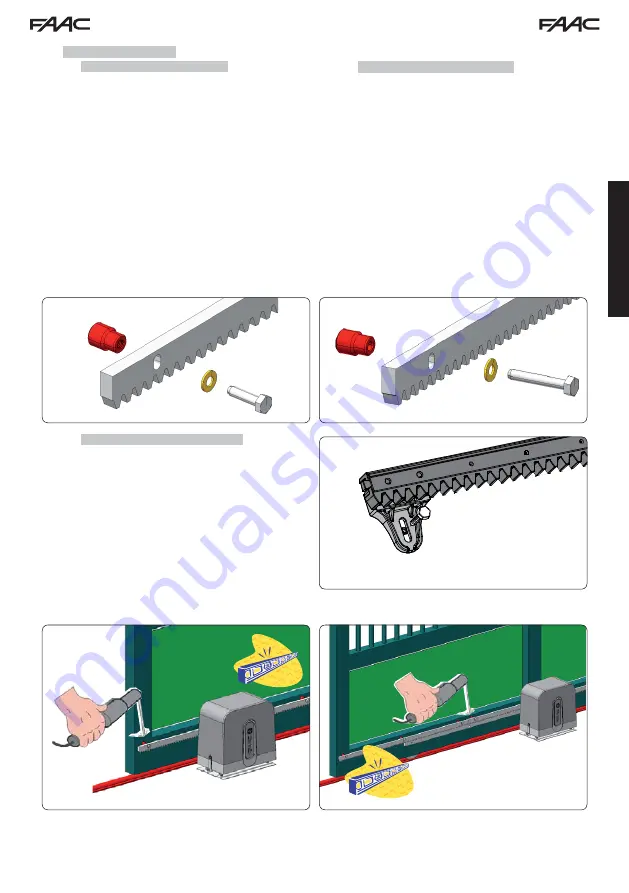
C720-C721
7
732568 - Rev.E
Fig. 11
Fig. 12
Fig. 13
Fig. 14
Fig. 15
ENGLISH
T
ranslation of the original instructions
5.4 INSTALLING THE RACK
5.4.1 STEEL RACK TO WELD (Fig.11)
1. Place the three threaded pawls on the rack element, posi-
tioning them at the top of the slot. In this way, the slot play
will enable any adjustments to be made.
2. Manually take the leaf into its closing position.
3. Lay the first piece of rack level on the pinion and weld the
threaded pawl on the gate as shown in Fig. 14.
4. Move the gate manually, checking if the rack is resting on
the pinion, and weld the second and third pawls.
5. Bring another rack element near to the previous one, using a
piece of rack (as shown in Fig. 15), to synchronise the teeth
of the two elements.
6. Move the gate manually and weld the three threaded pawls,
thus proceeding until the gate is fully covered.
5.4.2 STEEL RACK TO SCREW (Fig. 12)
1. Manually take the leaf into its closing position.
2. Lay the first piece of rack level on the pinion and place the
spacer between the rack and the gate, positioning it at
the top of the slot. In this way, the slot play will enable any
adjustments to be made.
3. Mark the drilling point on the gate. Drill a Ø 6.5 mm hole and
apply thread with a Ø 8 mm male tap. Screw the bolt.
4. Move the gate manually, checking if the rack is resting on
the pinion, and repeat the operations at point 3.
5. Bring another rack element near to the previous one, using
a piece of rack (as shown in figure 15) to synchronise the
teeth of the two elements.
6. Move the gate manually and carry out the securing opera-
tions as for the first element, thus proceeding until the gate
is fully covered.
5.4.3 NYLON RACK TO SCREW (Fig. 13)
1. Manually take the leaf into its closing position.
2. Lay the first piece of the rack level on the pinion and mark
the drilling point on the gate; drill Ø 5.2 mm and screw in
the self-tapping screw provided with its reinforcing plate.
3. Move the gate manually, checking if the rack is resting on
the pinion, and repeat the operations at point 2.
4. Couple another rack element and fit to the previous ele-
ment.
5. Move the gate manually and carry out the securing opera-
tions as for the first element, thus proceeding until the gate
is fully covered.
Summary of Contents for C720
Page 1: ...C720 C721 C720 C721...