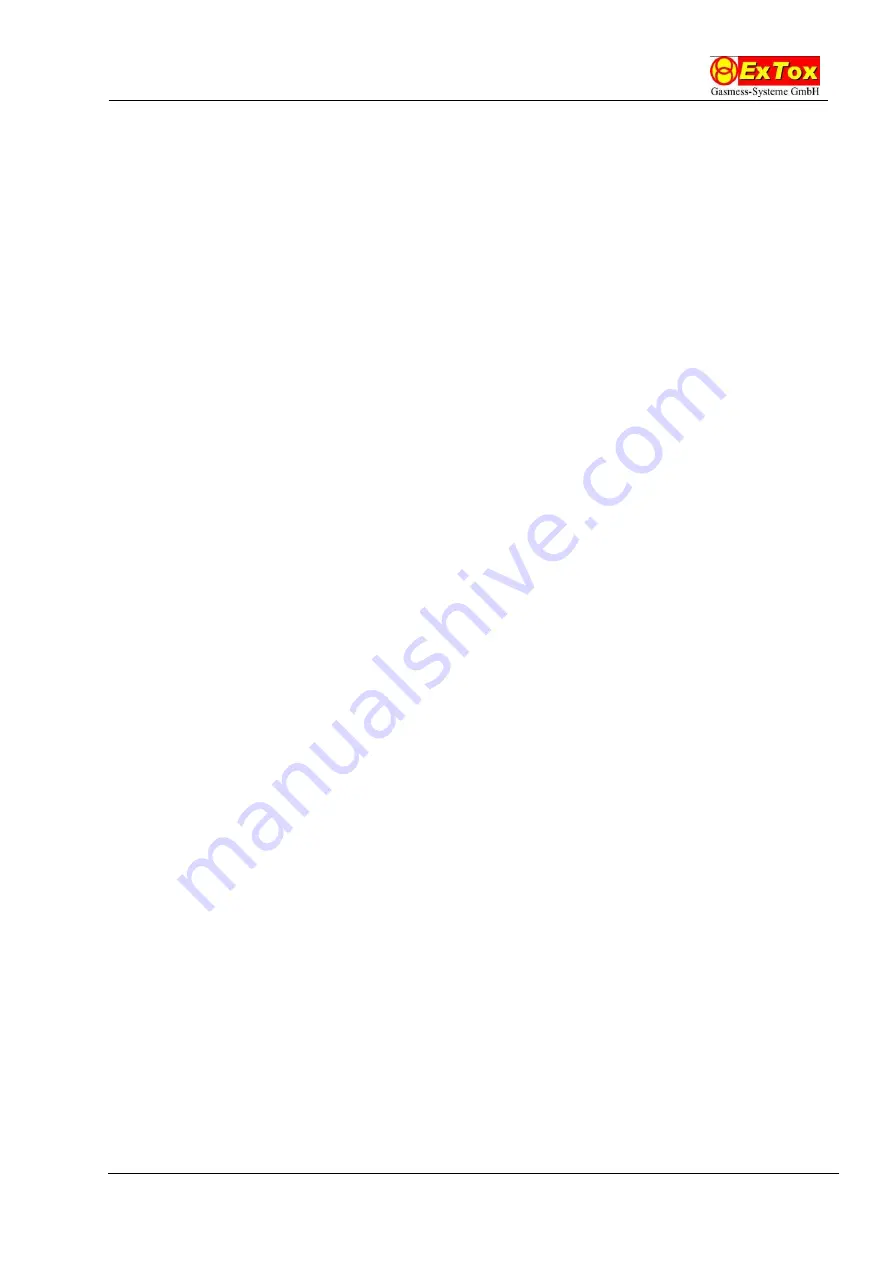
Instruction Manual
ExTox IMC-8/-4
BA_IMC-8_-4_e_2019-12-17.docx
Page 19 of 22
Dust Filter
The dust filter is integrated in the housing of flow rate monitoring. The condition of the filter can
easily be checked in the inspection glass. This test should be done regularly in intervals which
depend on the dust load of the measured gas. For exchange of the used filter inlet the inspection
glass can be removed. When closing you have to ensure correct installation of the sealing and
the inspection glass. Please also check tightness.
6.2
Housing Fans
The housing fans are equipped with a dust protection mat which should be cleaned regularly
from dust. Therefore remove plug cover and clean mat.
The redundant ventilation of housing including monitoring of fans avoids safely the formation of
potentially explosive mixtures in case of leakages in the IMC. The state of the fans is detailed
indicated on the display of the control unit ("FAN"). In case even one of the fan fails the status
indication changes from "OK" to "FAULT" and a fault of control unit is indicated at the control
unit.
6.3
Condensate Trap incl. Hose Pump
The condensate removal is automatically done via the hose pump (standard for Biogas and KAT-
Types). Nevertheless we recommend checking the condensate trap and hose line regularly on
possible blockages. Condensate traps and hose lines should be cleaned on demand. It has to be
ensured that the measured gas flow is not interfered. For this purpose it might be necessary to
disconnect hose lines. After connecting everything again please check tightness of sample line.
Please make sure that the condensate can drain off failure free and depending on composition of
condensate even safe from the connection at the bottom of the housing.
6.4
Measured Gas Cooler incl. Automatic Removal of Condensate
Gas dehumidification is done by means of a Peltier cooler. The temperature of measured gas is
factory sided adjusted to +5 °C and monitored. During the warm-up phase a fault message is
issued until the cooler reaches operation temperature.
The measured gas cooler meets the high requirements of the industrial process analysis. The
responsiveness of the temperature monitoring is a sign for the fact that the measured gas com-
poses of very high temperatures or of a very high condensate load. It is the same with clearly
higher measured gas volume streams.
The cooler is nearly maintenance free.
The condensate removal is automatically done via the hose pump. We recommend checking the
hose line regularly on possible blockages. Condensate traps and hose lines should be cleaned on
demand. It has to be ensured that the measured gas flow is not interfered. For this purpose it
might be necessary to disconnect hose lines. After connecting everything again please check
tightness of sample line.
Please make sure that the condensate can drain off failure free and safe from the connection at
the bottom of the housing.
6.5
Flame Arrestor
It has to be ensured that the flame arrestors are not clogged with dust or condensate. In other
aspects they are maintenance free.
Please note that the measured gas for standard construction of the flame arrestor should only
contain flammable gases of ignition protection up to IIB3, such as for example methane. Please
ask ExTox who assists you anytime for special gas mixtures.
As an option we could offer a flame arrestor for ignition protection IIC, such as for mixtures with
significant contents of hydrogen.
6.6
Enclosures Heating with Thermostat Control
The nominal temperature can be adjusted in a range of +5°C to +30 °C by means of a
regulator. The temperature should be that high that no formation of condensate inside the
housing will occur.
6.7
Data Logger, Data Interfaces, Customer Specific Modifcations
You will find detailed information to these topics in the separate documentation.