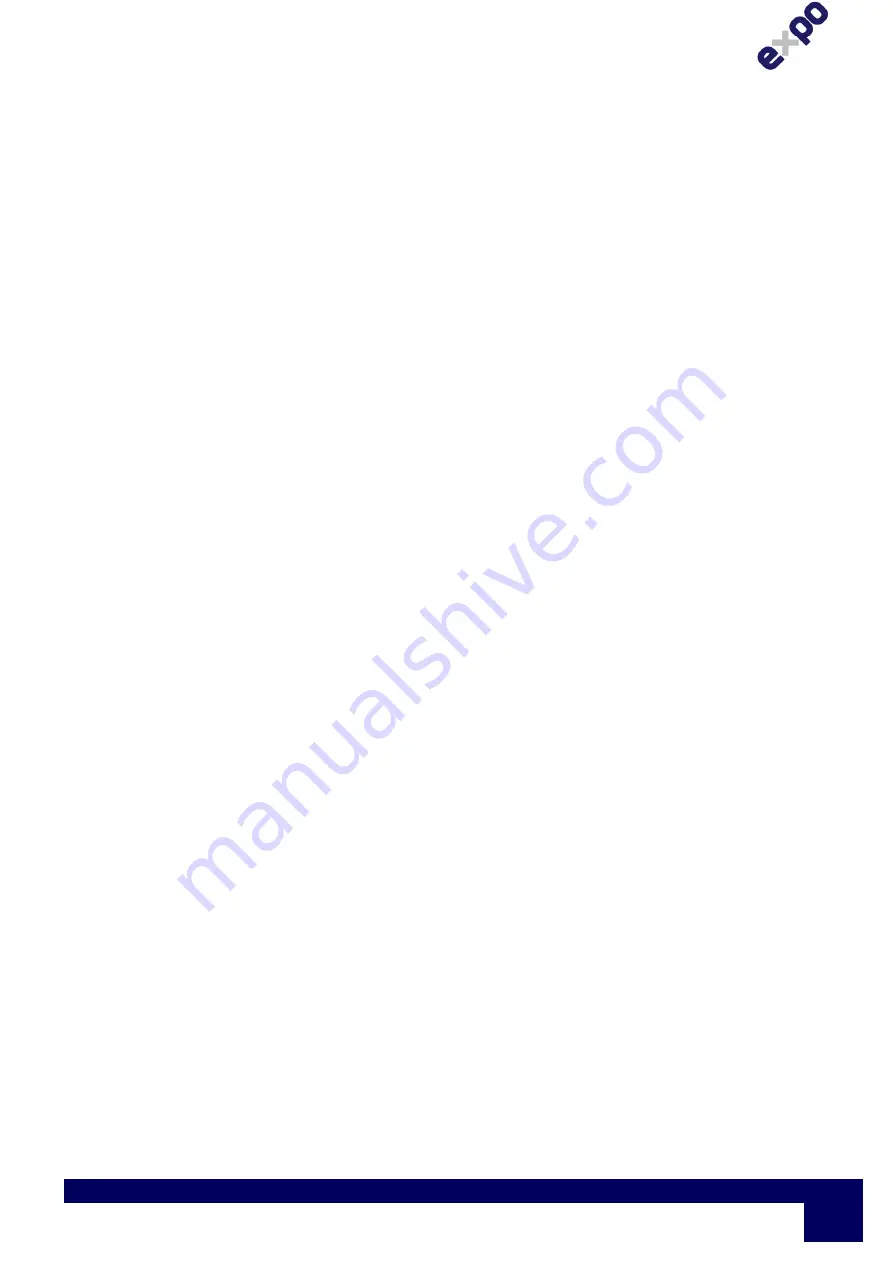
ML442 | v5k
Page
9
Expo Technologies UK
T: +44 (0) 20 8398 8011
E: [email protected]
Expo Technologies US
T: +1 (440) 247 5314
E:[email protected]
Expo Technologies China
T: +86 532 8906 9858
E: [email protected]
Particle Class 1
In each cubic metre of compressed air, the particulate count should not exceed 20,000 particles
in the 0.1 to 0.5 micron size range, 400 particles in the 0.5 to 1 micron size range and 10
particles in the 1 to 5 micron size range.
Humidity or pressure dew point
The dew point, at line pressure, shall be at least 10 °C below the minimum local recorded
ambient temperature at the plant site. In no case, should the dew point at line pressure exceed
+3 °C.
Oil Class 2
In each cubic metre of compressed air, not more than 0.1mg of oil is allowed. This is a total
level for liquid oil, oil aerosol and oil vapour.
When an inert gas is being used to supply the purge system, risk of asphyxiation exists. Refer
to
Application Suitability
section.
Before connection of the air supply to the purge system, the supply pipe work should be flushed
through with instrument quality air to remove any debris that may remain in the pipes. This must
be carried out for at least 10 seconds for every meter of supply pipe.
Unless a supply shut-off valve has been fitted to the MiniPurge
®
system, an external shut-off
valve with the same, or larger, thread size as the Control Unit inlet fitting should be fitted by the
installer to prevent any restriction of purge flow.
The purge air from the MiniPurge
®
Control Unit should be piped within the pressurized
enclosure to ensure purging of potential dead air spots.
The purge system is fitted with an internal regulator factory set to 3 bar feeding the logic.
4.4 Purge Air from CU to PE
When the CU is directly top mounted onto the PE, no connection will normally be necessary, as
the purge air will discharge into the PE directly. When the CU is not top mounted, or where
internal air distribution is necessary a connection should be made from the purge air outlet on
the CU (normally ½” NPT Female), via pipe pressure rated at least to the supply pressure, to
the PE. This should be kept as short as possible and should be adequately sized to ensure that
the full purge flow can be delivered.
4.5 CU to Enclosure Pressure Monitor
When the CU is mounted directly on the top of the PE, no connection will normally be
necessary, as the enclosure pressure monitor point will sense directly inside the PE.
If the CU is not mounted directly on the top of the PE or if there are fans, which may create
localised low-pressure areas within the PE, it is necessary to pipe this connection. The
connection is made to the enclosure pressure sensor fitting (normally 1/8” NPT Female) on the
CU. There is virtually no flow in this circuit, so small bore tube may be used. Expo
recommends 6mm O/D metal tube. Make sure that all connections are free of leaks.
4.6 CU to Flow Sensor
In Continuous Flow
(CF)
systems, a Differential Pressure Sensor is combined with the Minimum
Pressure Sensor and measures the "DP HI (High) / Enclosure Pressure" within the PE and the
pressure in the monitoring device at the back of the SAU "DP LO (Low) SAU Connection". This
connection requires a pipe connection between the CU and the SAU25.