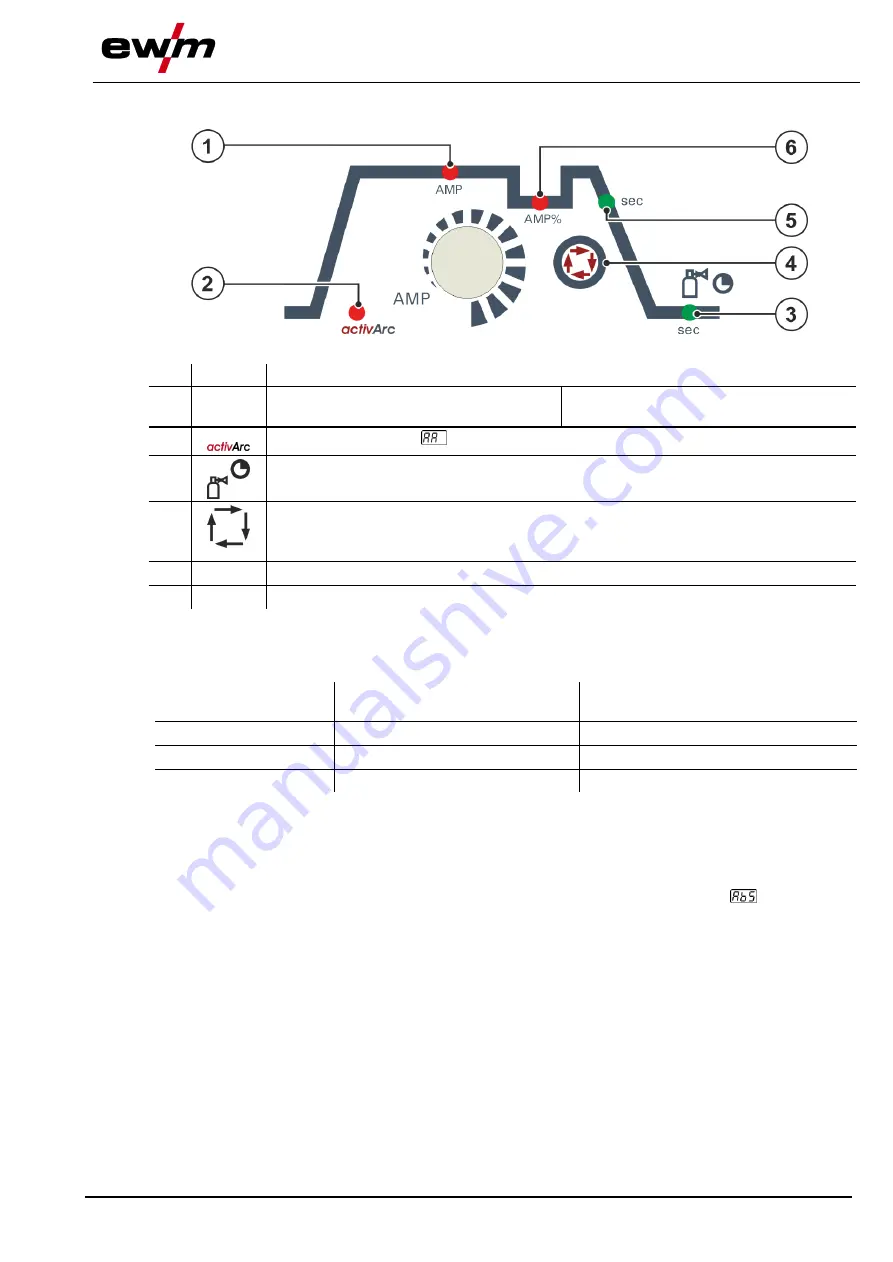
Machine description – quick overview
Machine control – Operating elements
099-000125-EW501
29.9.2022
17
4.2.1 Function sequence
Figure 4-3
Item Symbol Description
0
1
AMP Main current (TIG) / pulse current
I min to I max (1 A increments)
Main current (MMA)
I min to I max (1 A increments)
2
Signal light activArc
> see 5.2.6 chapter
3
Signal light, gas post-flow time
4
Select welding parameters button
This button is used to select the welding parameters depending on the welding process
and operating mode used.
5
sec
Down-slope time (TIG)
6
AMP% Secondary current / pulse pause current
4.2.2 Welding data display
The following welding parameters can be displayed before (nominal values) or during (actual values)
welding.
Parameter
Before welding
(nominal values)
During welding
(actual values)
Welding current
Parameter times
Parameter currents
not possible
possible
4.2.3 Setting the welding current (absolute/percentage)
The welding current for the ignition, secondary, end and hot start current can be set as a percentage of
the main current AMP or as an absolute value. To select the display use the parameter
in the confi-
guration menu
> see 5.8 chapter
.