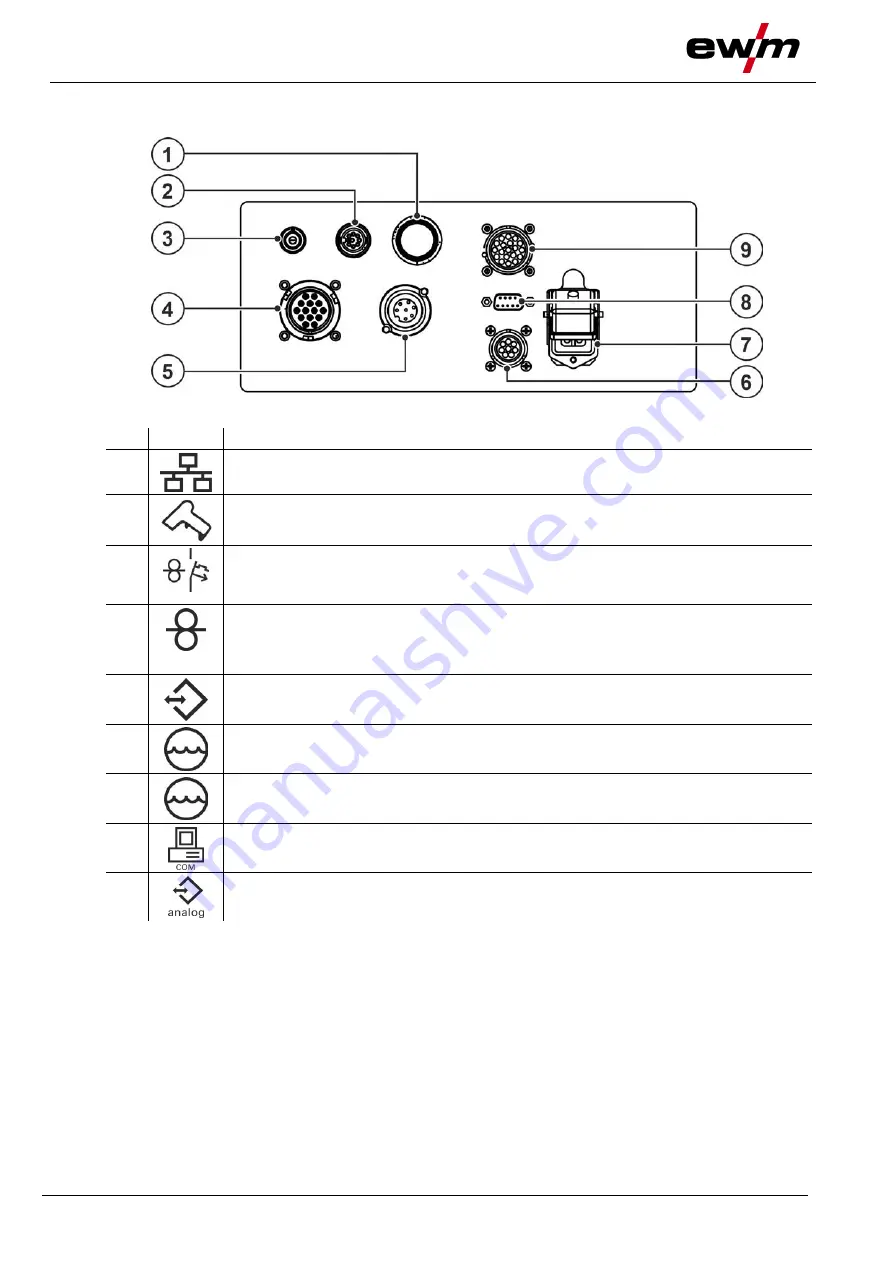
Machine description – quick overview
Front view / rear view
18
099-005664-EW501
22.09.2021
4.1.1 Connection panel
Figure 4-2
Item Symbol Description
0
1
Connection socket - RJ45 - Option
Network connection
> see 5.7 chapter
2
Connection socket for hand scanner - optional
Component identification Xnet
> see 5.9 chapter
3
Key button, Automatic cutout
Wire feed motor supply voltage fuse
(press to reset a triggered fuse)
4
DV1
14-pole connection socket
Wire feeder control cable connection
5
7-pole connection socket (digital)
For connecting digital accessory components
6
8-pole connection socket
Cooling unit control lead
7
4-pole connection socket
Cooling unit voltage supply
8
Connection socket (9-pole) - D-Sub
PC interface
> see 5.8 chapter
9
Connection socket- 19-pole, analogue - optional
Interface for automated welding
> see 5.6.1 chapter