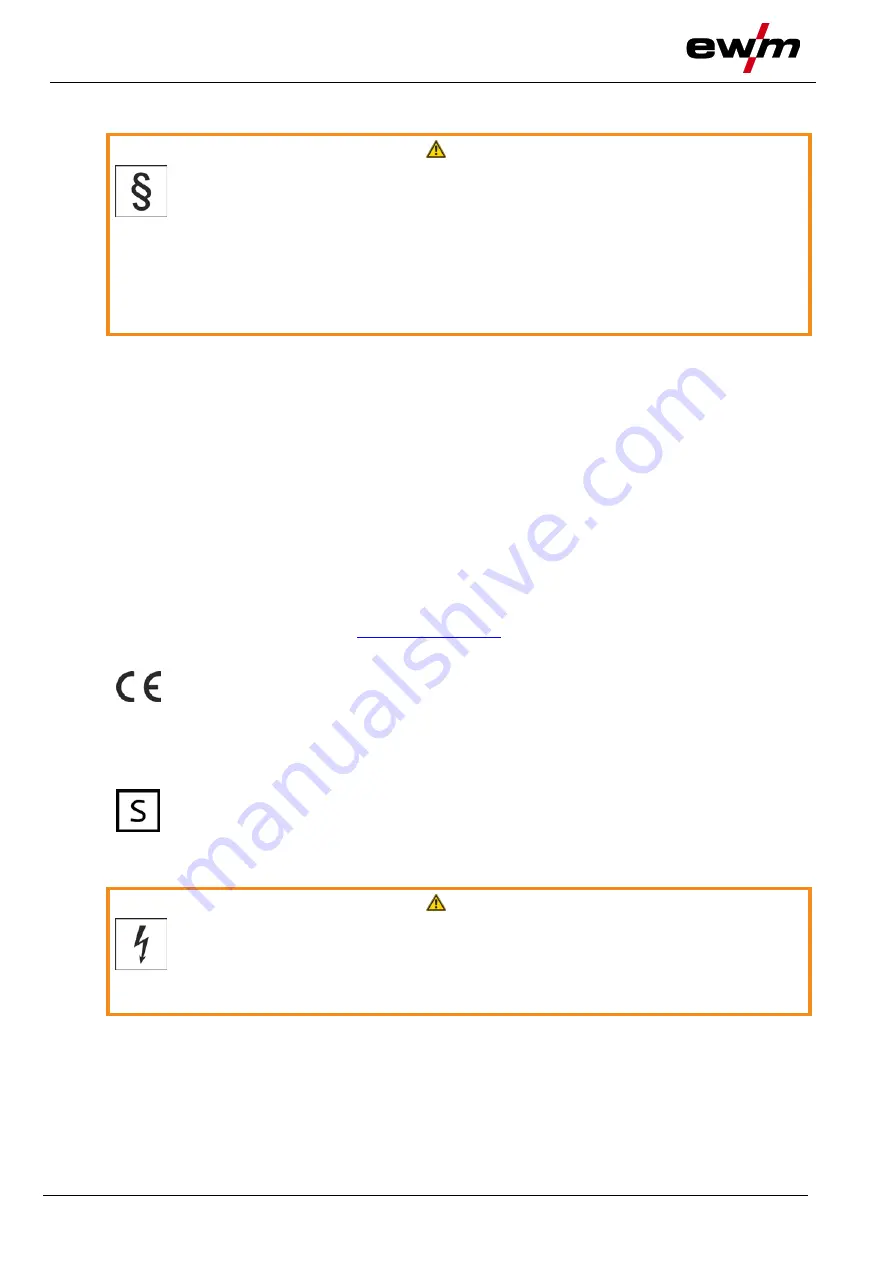
Intended use
Applications
12
099-005546-EW501
7.12.2020
3
Intended use
WARNING
Hazards due to improper usage!
The machine has been constructed to the state of the art and any regulations and
standards applicable for use in industry and trade. It may only be used for the welding
procedures indicated at the rating plate. Hazards may arise for persons, animals and
material objects if the equipment is not used correctly. No liability is accepted for any
damages arising from improper usage!
• The equipment must only be used in line with its designated purpose and by trained or
expert personnel!
• Do not improperly modify or convert the equipment!
3.1 Applications
Arc welding machine for GMAW welding with TIG welding and lift arc (touch starting) or MMA welding as
secondary process. It may be possible to expand the functionality by using accessories (see the
documentation in the relevant chapter).
3.2 Software version
These instructions apply to the following software version:
0.5.9.0
The software version of the machine control can be displayed in the machine configuration menu
(menu Srv)
> see 5.5 chapter
.
3.3 Documents which also apply
3.3.1 Warranty
For more information refer to the "Warranty registration" brochure supplied and our information regarding
warranty, maintenance and testing at
3.3.2 Declaration of Conformity
This product corresponds in its design and construction to the EU directives listed in the
declaration. The product comes with a relevant declaration of conformity in the original.
The manufacturer recommends carrying out the safety inspection according to national and
international standards and guidelines every 12 months.
3.3.3 Welding in environments with increased electrical hazards
Power sources with this marking can be used for welding in an environment with increased
electrical hazard (e.g. boilers). For this purpose, appropriate national or international regulations
must be followed. The power source must not be placed in the danger zone!
3.3.4 Service documents (spare parts and circuit diagrams)
WARNING
Do not carry out any unauthorised repairs or modifications!
To avoid injury and equipment damage, the unit must only be repaired or modified by
specialist, skilled persons!
The warranty becomes null and void in the event of unauthorised interference.
• Appoint only skilled persons for repair work (trained service personnel)!
Original copies of the circuit diagrams are enclosed with the unit.
Spare parts can be obtained from the relevant authorised dealer.
3.3.5 Calibration/Validation
An original certificate is enclosed with the product. The manufacturer recommends calibration / validation
at intervals of 12 months.