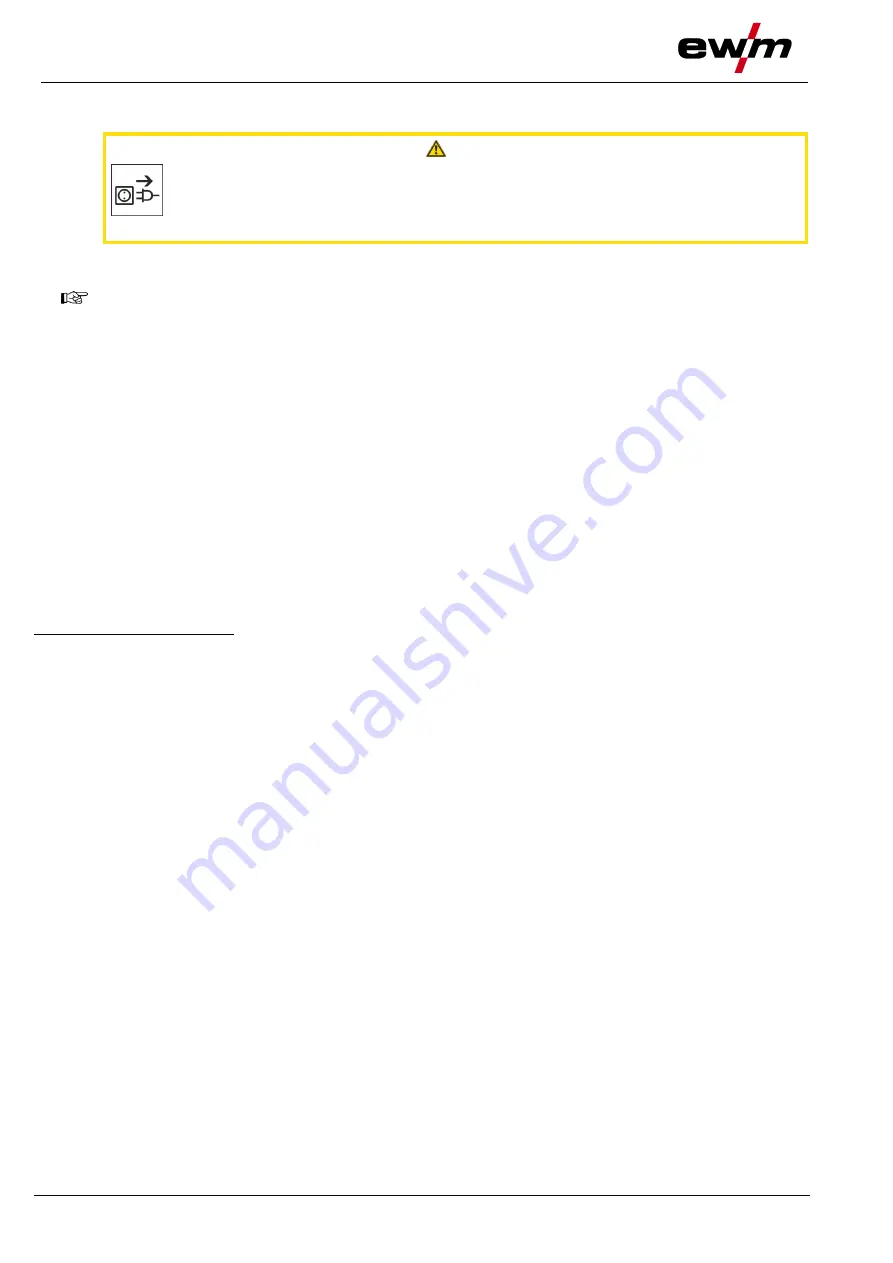
Design and function
Transport and installation
10
099-008232-EW501
26.05.2020
5.2 Transport and installation
CAUTION
Risk of accidents due to supply lines!
During transport, attached supply lines (mains leads, control cables, etc.) can cause
risks, e.g. by causing connected machines to tip over and injure persons!
• Disconnect all supply lines before transport!
5.2.1 Ambient conditions
Equipment damage due to contamination!
Unusually high amounts of dust, acids, corrosive gases or substances can damage the machine
(observe maintenance intervals > see 6.2 chapter).
• Avoid large amounts of smoke, steam, oily fumes, grinding dust and corrosive ambient air!
5.2.1.1 In operation
Temperature range of the ambient air:
• -10 °C to +40 °C (-13 F to 104 F)
[1]
Relative humidity:
• up to 50 % at 40 °C (104 F)
• up to 90 % at 20 °C (68 F)
5.2.1.2 Transport and storage
Storage in a closed area, temperature range of the ambient air:
• -25 °C to +55 °C (-13 F to 131 F)
[1]
Relative humidity
• up to 90 % at 20 °C (68 F)
[1]
Ambient temperature dependent on coolant! Observe the coolant temperature range of the torch coo-
ling
5.3 Functional characteristics
Liquid-cooled plasma torch for gas shielded arc welding of high-quality steels, copper and titanium alloys
of different material thicknesses. Essentially, all metals can be welded that can be welded using the TIG
process (DC). This also includes titanium, zirconium, gold, silver and copper with its alloys.
Operation requires the use of a power source in conjunction with a circulating-air or recooling unit. Trade
and industry use the diversity of this process.
5.3.1 Procedure
In physics, a plasma is an electrically conductive gas consisting of a mixture of molecules, electrons,
atoms and ions. Depending on the plasma gas used, temperatures of 15,000 to 20,000 K are reached in
the plasma jet.
The welding torch works on the principle of the transferring arc. The arc burns between electrode and
workpiece during welding and is constricted by the plasma nozzle, the composition and the amount of
shielding gas used. This enables joints to be made with high quality at high working speeds.
To make the path between the electrode and the workpiece electrically conductive, the pilot arc is first ig-
nited inside the torch between the electrode and the plasma nozzle by applying high-frequency high vol-
tage. The pilot gas is ionised, emerges from the plasma nozzle and makes the path between the electro-
de and the workpiece electrically conductive. When the ionised gas jet touches the workpiece surface, the
main circuit is closed. This forms the main arc between electrode and workpiece and the welding process
begins.
The good cooling of the torch and the high welding speed help to keep the heat-affected zone and the
thermal distortion of the material to be processed low.
Indirect electrode cooling ensures easy and fast electrode replacement. If handled correctly, no coolant
water can get into the interior of the torch when changing the electrode leading to ignition failure and re-
duction of the service life of electrode and nozzle.