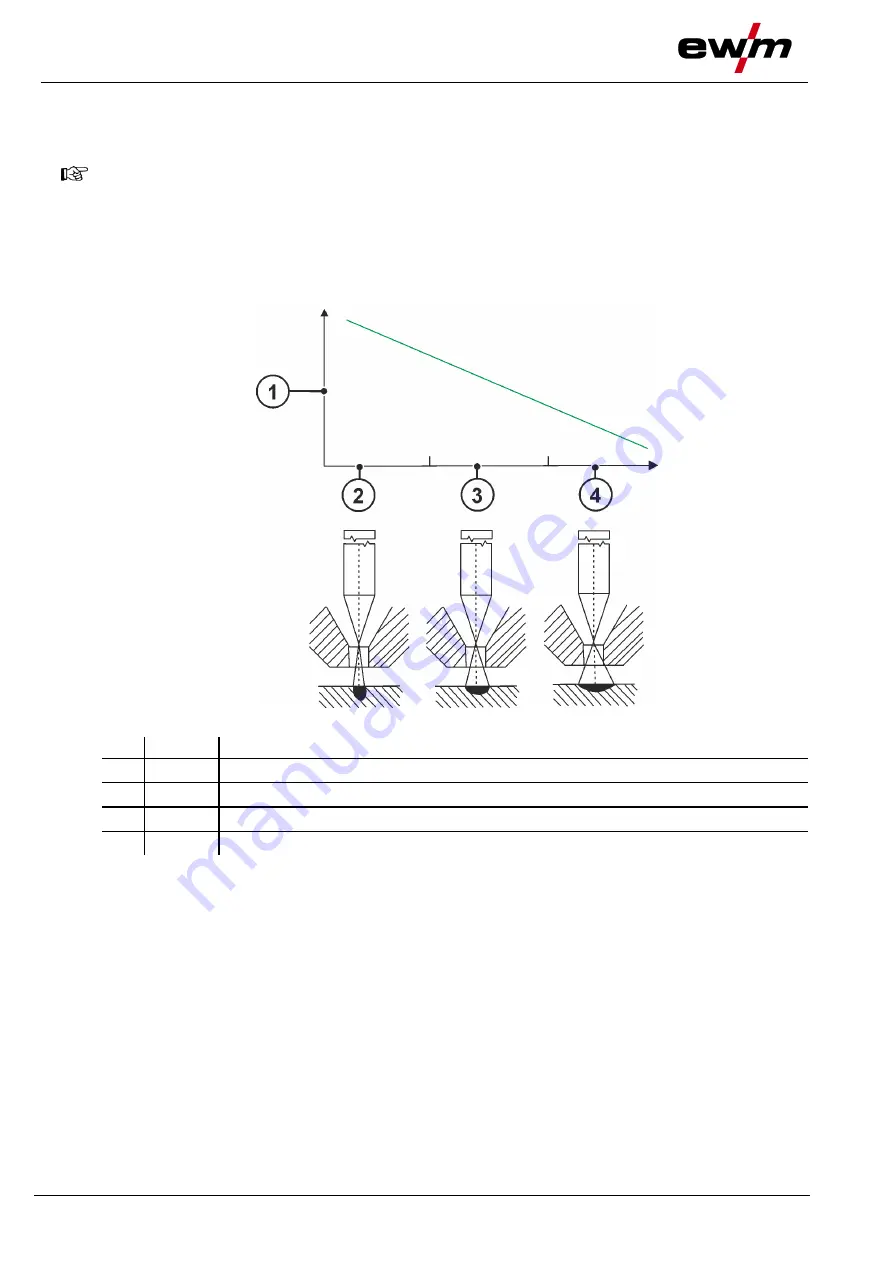
Design and function
Tables of current carrying capacity
16
099-008232-EW501
26.05.2020
• Place the shielding gas cylinder into the relevant cylinder bracket.
• Secure the shielding gas cylinder against falling over.
Use only 2-stage bottle pressure regulators with bar display on the output side.
Argon is usually used as the arc-forming gas. It is easier to ionise and, therefore, allows a low-energy arc.
In some cases, a mixture of argon with up to 10% hydrogen or helium may be used. Larger additions may
destroy the welding torch.
The amount of plasma gas required is directly related to the nozzle aperture. The larger the nozzle
aperture, the more plasma gas is required. A plasma gas quantity that is too low leads to premature wear
of the plasma nozzle.
Figure 5-7
Item Symbol Description
0
1
Plasma gas quantity
2
deep penetration (small seam width)
3
medium penetration
4
shallow penetration (large seam width)
A reduced quantity of plasma gas (pos. 2 to 4) results in a softer arc characteristic and a shallow penetra-
tion. A reduced quantity of plasma gas (pos. 4 to 2) results in a shallow penetration.
5.7.3 Shielding gas
Argon is usually used as shielding gas. To fully achieve the desired constriction effect, up to 10%, in spe-
cial cases up to 30%, hydrogen must be added to the shielding gas. This reduces the surface tension of
the weld pool and thereby promotes wettability.
The materials copper or copper-containing alloys and the reactive metals titanium, tantalum and zirconi-
um are an exception. In these cases, helium is used as an additive instead of hydrogen.
5.7.4 Forming gas
The forming gas protects the underside of the seam from oxidation and prevents the root from sagging
excessively thanks to its supporting effect. Depending on the materials to be welded, the following gas
mixtures are used.
• Ar
• Ar/H
2
• N
2
/H
2