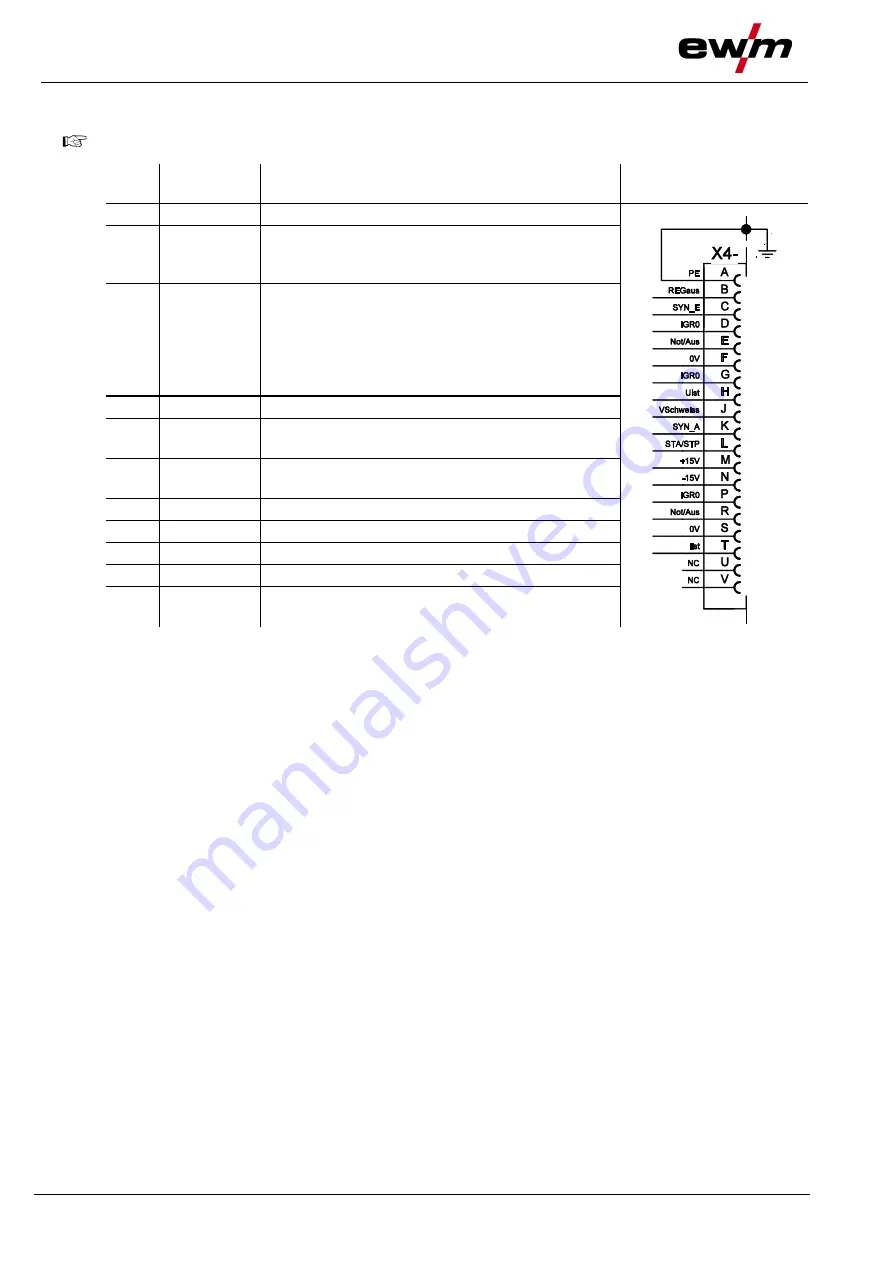
Design and function
Interfaces for automation
72
099-005504-EW501
20.11.2015
5.14.1 Automation interface
These accessory components can be retrofitted as an option - See 9 Accessories chapter.
Pin
Input /
output
Description
Diagram
A
Output
PE
Connection for cable shielding
D
Output
(open
collector)
IGRO
Current flows signal I>0 (maximum load 20
mA / 15 V)
0 V = welding current flows
E
+
R
Input
Not/Aus Emergency stop for higher level shut-down
of the power source.
To use this function, jumper 1 must be
unplugged on PCB M320/1 in the welding
machine. Contact open
welding current
off
F
Output
0 V
Reference potential
G/P
Output
I>0
Power relay contact, galvanically isolated
(max. +/-15 V / 100 mA)
H
Output
Uist
Welding voltage, measured against pin F,
0-10 V (0 V = 0 V; 10 V = 100 V)
L
Input
Str/Stp Start = 15 V / Stop = 0 V
1)
M
Output
+15 V
Voltage supply (max. 75 mA)
N
Output
-15 V
Voltage supply (max. 25 mA)
S
Output
0 V
Reference potential
T
Output
Iist
Welding current, measured on pin F;
0-10 V (0 V = 0 A, 10 V = 1000 A)
1
) The operating mode is given by the wire feed unit (the start / stop function equates to pressing
the torch trigger and is used in mechanised applications, for example).