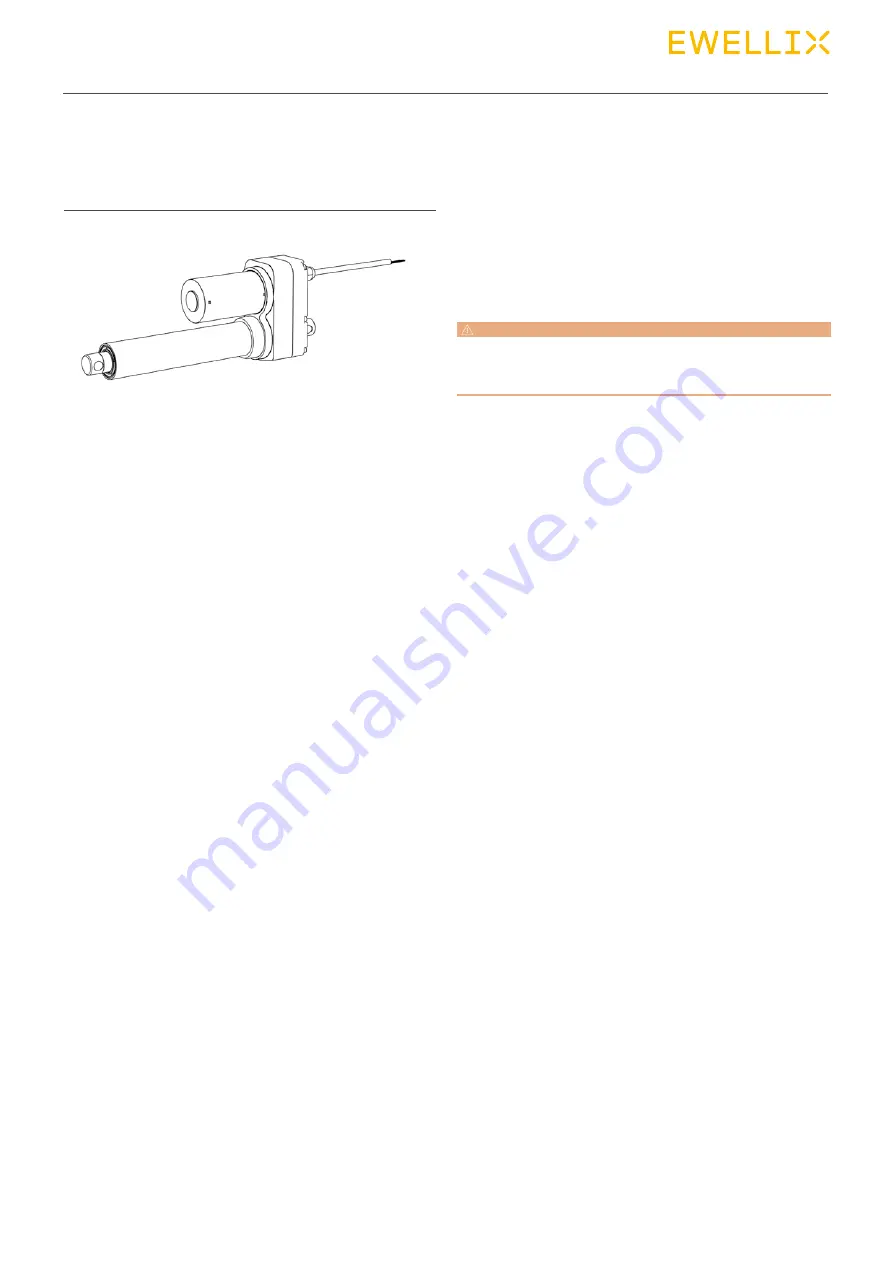
15
4.0 Structure a n d fun ctio n
4.2 Brief description
Overview
This actuator is to be used exclusively for installation into a
dynamic centric-compression or tensile-loaded lift.
The linear actuator consists of a motor part (4), a gear unit
(7) and a linear unit (3), connected with each other.
The actuator consists of a direct current motor with helical
gear which sets in motion a gear transmission system. Via
the driving screw and nut, the rotation of gear is transformed
into a linear motion of the actuator.
The front hinge head (1) and the rear hinge head (6) transmit
the actuator power to both sides of the application.
Depending the CAHB-2xE version, the extension tube can
rotate and must be fasten on the application to avoid the ro-
tation and provide the linear movement. In option for the
CAHB-2xE, the tube can get an anti rotation. The anti-rota-
tion of the tube is a standard feature of the CAHB-2xS
Fig. 11
4.3 Special features
Mechanical overload protection
The actuator contains a mechanical overload protection unit
(clutch).This overload protection unit will activate if the linear
unit of the actuator overloads. This activation will avoid to
push or pull over the maximum force defined on the data-
sheet and will protect the motor and gear unit from being
damaged.
CAUTION
Continued operation of the clutch can result in overheating and
damage to the linear actuator. If clutch activates, switch off power
immediately.
Integrated controller (S design only)
The smart version has a built-in electronics controller with
H-bridge and 2 micro controllers . This integrated controller
provides multiple functions described bellow.
Unique true absolute position sensor
(S design only)
A unique absolute positioning system equipped all smart
CAHB-2xS . Based on gears and no contact sensors, the
tube position generate an absolute signal in-stead of an in-
cremental signal. The actuator will never lose the position
even if the tube of the actuator is moving when the actuator
is not powered. No need of calibration to keep the full per-
formance during the ac-tuator life.
Electronic overload protection
(S design only)
An electronics over load protection limits the current draw by
a current cut-off, so the force that the actuator can push or
pull. The temperature effect on the performance is compen-
sated by the micro controller after a calibration done at the
end of line test of the actuator assembly line.
Soft start / soft stop (S design only)
The soft start and soft stop with a ramp up and ramp down
during 200 ms is set on the controller in order to limit the dy-
namic effect of the acceleration and dec-celaration and get
a smooth movement.