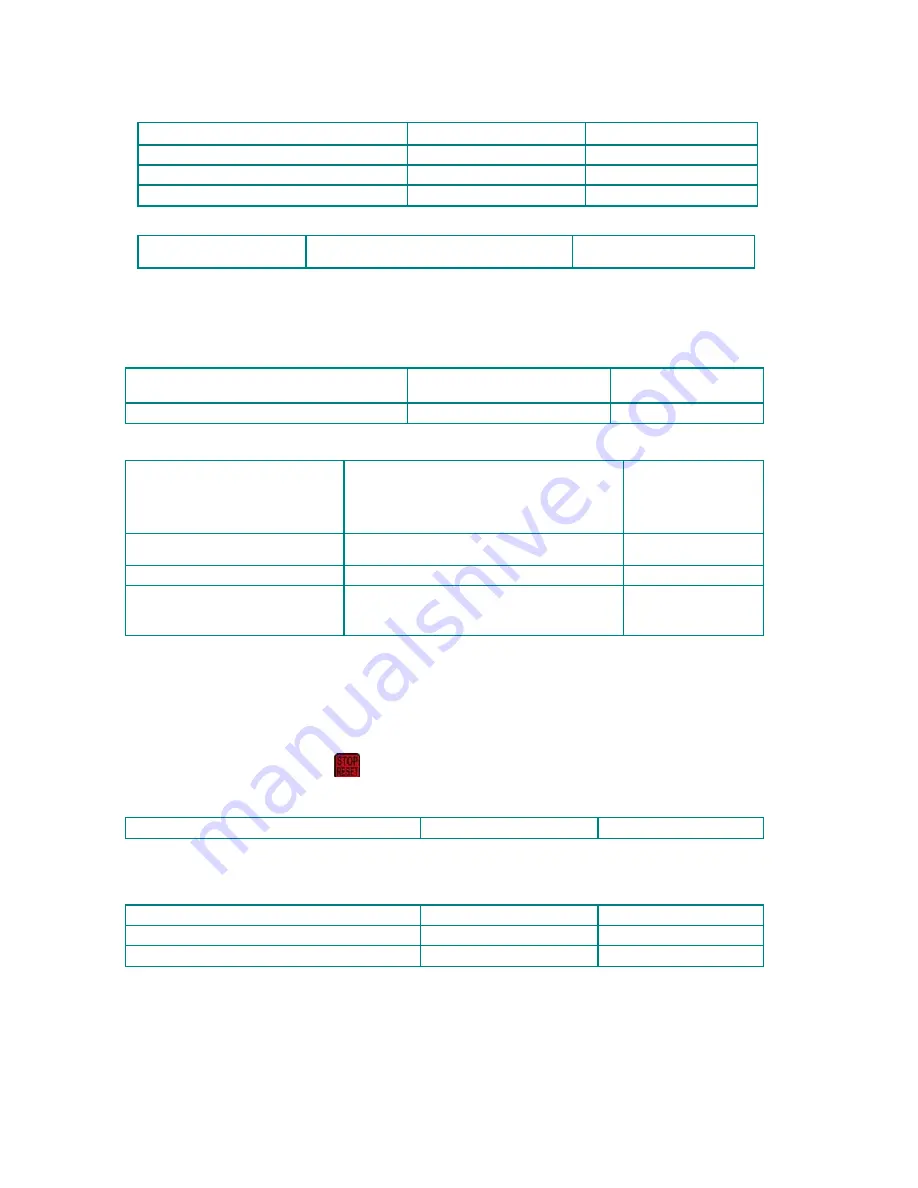
17) Parameter group A00: PID controller setup
PID controller parameter setting
FA19
Proportional gain
P
Range: 0.00…10.00
Default setting: 0.3
FA20
Integration time
I
(sec.)
Range: 0.1…100.0 sec.
Default setting: 0.3 sec.
FA21
Differential time
D
(sec.)
Range: 0.00…10.00
Default setting: 0.0 sec.
FA22
Controller cycle time / scan-rate (sec.)
Range: 0.1…10.0 sec.
Default setting: 0.1 sec.
Reversing lock for negative controller results
FA23
Reversing lock
Selection 0: Reversing not allowed
Default setting: 0
1: Reversing allowed
Specific pump controller parameter
Specific functions for dual pump booster station control are available in E2000+ inverters. Please ask for
detailed description and configuration proposals
Master / Slave interchange
FA24
Interchange time: units
Selection: 0: hours
Default setting: 0
1: minutes
FA25
Interchange time setting (hours / min.)
1....9999
Default setting: 100 h
Idling / lack of water protection
FA26
Lack of water protection
Selection: 0: No protection
1: Sensor signal through digital input
Default setting: 0
concept
2: Controller algorithm
3: Motor idling current detection
FA27
Current limit for lack of water
Range: 10…150 %
Default setting: 80%
detection (% of rated current)
FA28
Recheck delay time (sec.)
Range 0.0…3000 sec.
Default: 60 sec.
FA66
Delay time for lack of water
Range: 0…60 sec.
Default setting: 2 sec.
message (FA26=3)
FA26=1:
Lack of water is triggered through digital input (function assignation code
30
)
– it will stop the inverter and
display
EP1
. The „Water OK“ signal through a different digital input (function assignation code
31
) will reset the system.
FA26=1:
there is no delay for fault trigger.
FA26=2:
In case the controller reaches the maximum frequency, and the motor current still remains below the value
in
FA27,
the controller will interpret the situation as lack of water.
EP2
will show up on the display. The inverter will
stop
immediately.
FA26=3:
Detection via motor current measuring only. If the motor current falls below the value in
FA66,
the fault will be
triggered with delay, set in
FA66.
Inverter will stop and
EP3
will show up on the display.
FA28
Recheck time, timeframe for the inverter to recheck, if lack of water condition still persists, before it restarts. It is anytime
possible to reset the system, pressing.
Controller dead band +/- % of the set point
FA29
Dead band setting (% of set-point)
Range: 0.0 - 10.0 %
Default setting: 2.0
If the feed -back (actual value) stays within the dead band, the controller does not make any activity, and it keeps the
output frequency constant. The FA29 parameter is used also for starting/stopping the fixed speed pump
– see below
Dual pump booster control (one pump inverter controlled, one pump fixed speed)
FA30
Delay-time to start inverter pump (sec.)
Range: 2.0 - 999.9 sec.
Default setting: 20.0
FA31
Delay-time, to start fixed speed pump (sec.)
Range: 0.1 - 999.9 sec.
Default setting: 30.0
FA32
Delay-time to stop fixed speed pump (sec.)
Range: 0.1 - 999.9 sec.
Default setting: 30.0
If the feed- back value (actual value) exceeds the limits, given by FA29, the fixed pump will be started or respectively
stopped. Start /Stop delay time is set by
FA31
and
FA32.
E2000+_Rev.02 -E- SOFT Rev. 5.09
- 66 -
© 2016-06-KPP-EURADRIVES EUROPE GmbH
Summary of Contents for E2000-0004 S2B
Page 24: ...2016 06 KPP EURADRIVES EUROPE GmbH...
Page 27: ...E2000 _Rev 02 D SOFT Rev 5 09 22 2016 06 KPP EURADRIVES EUROPE GmbH...
Page 47: ...2016 06 KPP EURADRIVES EUROPE GmbH...
Page 49: ...2016 06 KPP EURADRIVES EUROPE GmbH...
Page 55: ...2016 06 KPP EURADRIVES EUROPE GmbH...
Page 63: ...2016 06 KPP EURADRIVES EUROPE GmbH...