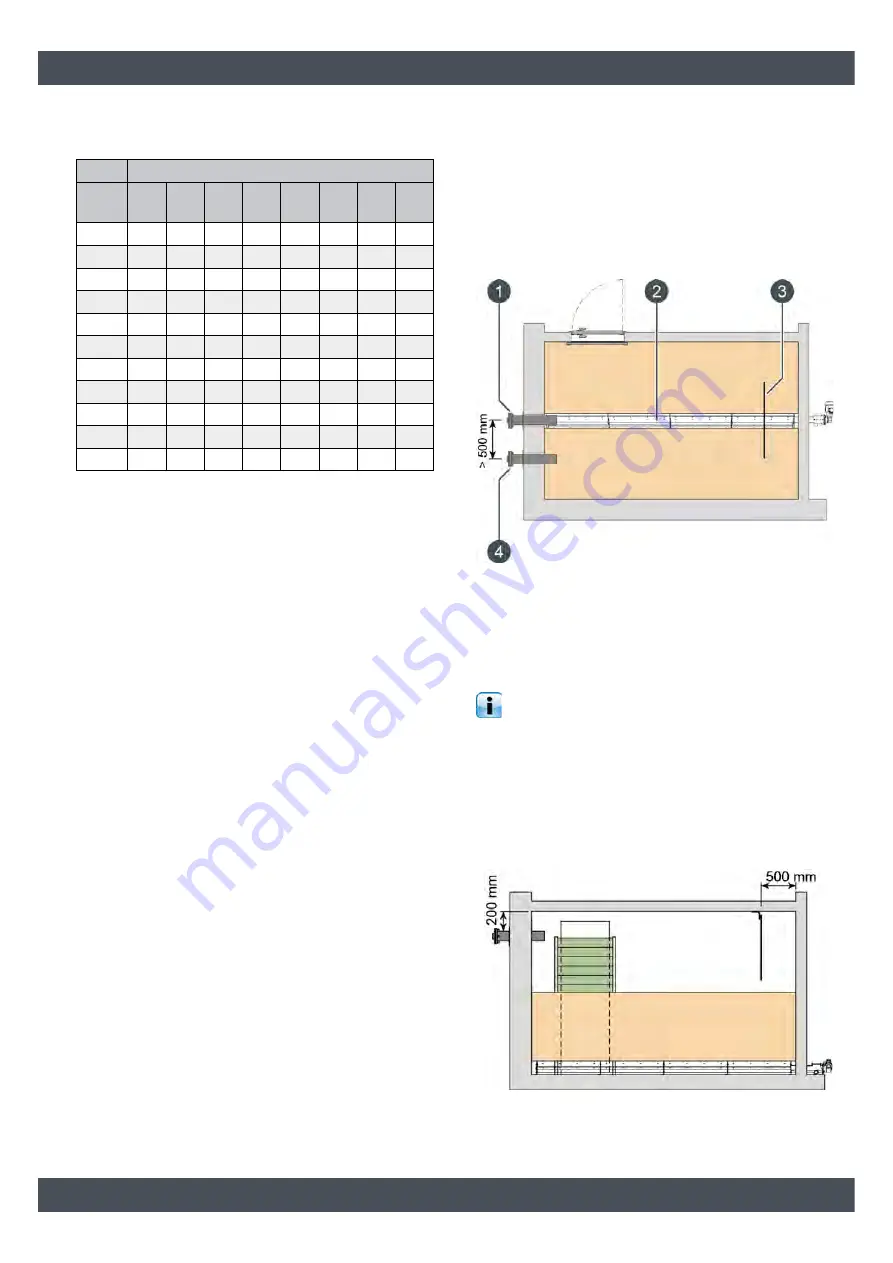
Pellet store
Filling nozzles
37
•
Free space for the conveying system 80 mm
Tab. 6-1: Useful cross section
With the useful cross section of the storeroom, the
storage volume and the storage contents can be
calculated:
•
Storage volume (in m³) = useful cross section (m²)
x room length
•
Amount (in tonnes) = storage volume (m³) x 0.650
6.4
Filling nozzles
Installing the filling nozzles in the narrow side of
the pellet store
Two nozzles are preferably installed in the narrower
outer wall of the pellet store. One for blowing in the
pellets (filling nozzle) in the middle and the other for
back air (back air nozzle) to the side.
Fig. 6-2: Filling nozzles on the short side
1
Filling nozzle
2
Conveyor screw
3
Impact protection mat
4
Return air nozzle
Label the filling nozzle and the suction nozzle so
that the pellet supplier recognises which nozzle
the pellets are blown into.
Opposite the middle filling nozzle, an impact protection
mat is installed 500 mm from the wall to prevent
damage to both pellets and the plasterwork on the wall.
The filling nozzles must be installed 200 mm below the
ceiling to keep the pellets from scraping on the ceiling
during injection.
Usable cross section in m²
Total height of the storeroom (m)
Width
(m)
2.0
2.2
2.4
2.6
2.8
3.0
3.2
3.4
2.0
2.20 2.60 3.00 3.40 3.80 4.20 4.60 5.00
2.2
2.33 2.77 3.21 3.65 4.09 4.53 4.97 5.41
2.4
2.44 2.92 3.40 3.88 4.36 4.84 5.32 5.80
2.6
2.53 3.05 3.57 4.09 4.61 5.13 5.65 6.17
2.8
2.61 3.17 3.73 4.29 4.85 5.41 5.97 6.53
3.0
2.67 3.27 3.87 4.47 5.07 5.67 6.27 6.87
3.2
2.72 3.36 4.00 4.64 5.28 5.92 6.56 7.20
3.4
2.75 3.43 4.11 4.79 5.47 6.15 6.83 7.51
3.6
2.76 3.48 4.20 4.92 5.64 6.36 7.08 7.80
3.8
2.76 3.51 4.27 5.03 5.79 6.55 7.31 8.07
4.0
2.76 3.53 4.33 5.13 5.93 6.73 7.53 8.33