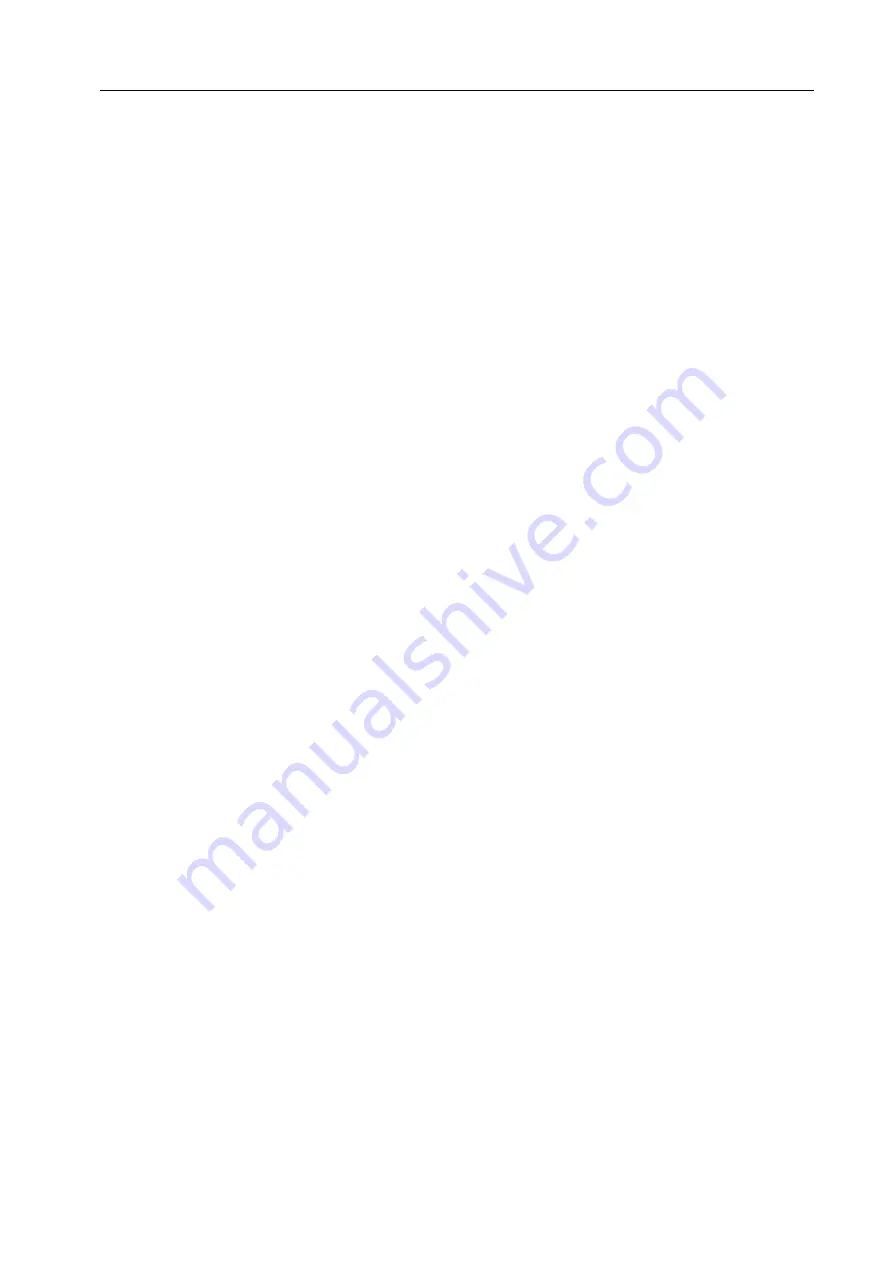
Scara Mechanical Unit Manual
Document Version:
Error! Unknown
document property name.
(
Error!
Unknown document property
name.
)
© 2020
Error! Unknown document property name.
All right reserved.
v
(5)
To shut off power to the robot system, pull out the power plug from the power source. Be sure to
connect the AC power cable to a power receptacle. DO NOT connect it directly to a factory power
source.
(6)
Before performing any replacement procedure, turn OFF the Controller and related equipment, and
then pull out the power plug from the power source. Performing any replacement procedure with
the power ON is extremely hazardous and may result in electric shock and/or malfunction of the
robot system.
(7)
Do not insert or pull out the motor connectors while the power to the robot system is turned ON.
Inserting or pulling out the motor connectors with the power ON is extremely hazardous and may
result in serious bodily injury as the Robot may move abnormally and may result in electric shock
and/or malfunction of the robot system.
(8)
Whenever possible, only one person should operate the robot system. If it is necessary to operate
the robot system with more than one person, ensure that all people involved communicate with
each other as to what they are doing and take all necessary safety precautions.
(9)
Joint #1, #2 and #4: repeatedly operating the joint in a motion angle less than 5 degrees may result
in shortage bearing oil film and shorten the service life of joint. To avoid shortening the service life
of joint, please move the joint over 50 degrees for about 5 to 10 times per day.
(10)
Joint #3: if arm moving distance of up and down is shorter than 10mm, please move the joint over
half of the maximum motion range for about 50 times per day.
(11)
When the robot is operating at a low speed (about 5~20% of rated speed), continuous vibration (or
sympathetic vibration) may occur as the direction of arm and end effector load. The following
measures may reduce vibration caused by natural vibration frequency of arm.
•
Change operating speed
•
Change teaching point
•
Change the load of end effector
(12)
Vibration of the front end of the arm may increase when J3-axis upper side or lower side is moving,
according to the weight and inertia of the grippers. This is due to an increased distance between
the end and head of the shaft, which leads to a change in inertia. Adjust speed etc. according to
item 11 when this vibration causes negative effect on robot operation.
(13)
Do not touch Joint #3 and Joint #4 directly by hand during greasing and teaching. Touch Joint #3
and Joint #4 frequently may cause rust.
(14)
When tear down the adhesive tape or seal on the oil paint surface of the robot and the cabinet, be
careful that damage to the paint may occur.
(15)
The surface of the robot may be heated when operating with high payload or high speed. Pay
attention to second injury due to unintentionally touch of heated parts. Perform maintenance when
the robot is cooled down.