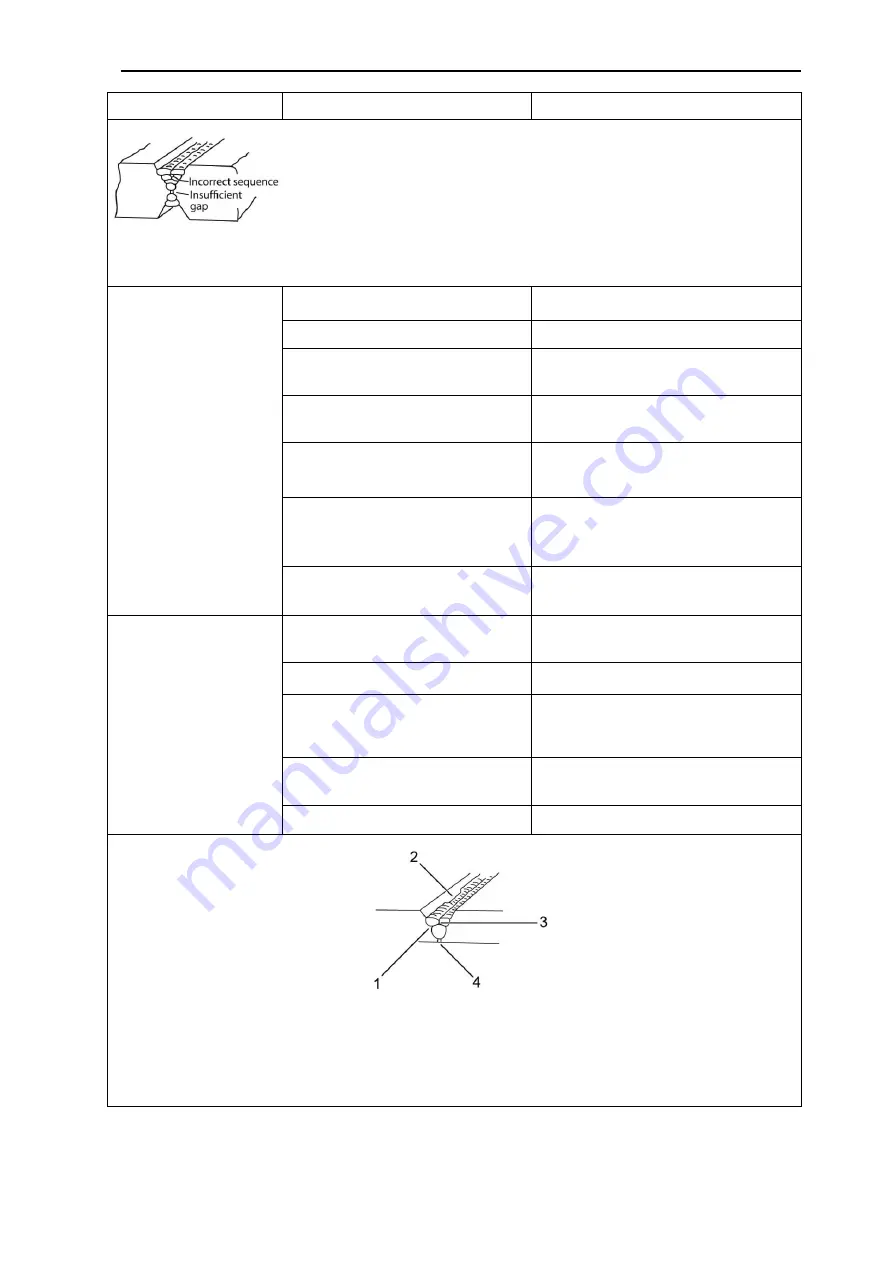
8 TROUBLESHOOTING
0463 766 001
-
75
-
© ESAB AB 2021
Type of fault
Cause
Corrective action
Figure 83: Example of insufficient gap or incorrect sequence
A groove has been
formed in the base
metal adjacent to
the toe of a weld
and has not been
filled by the weld
metal (undercut).
The welding current is too high.
Reduce the welding current.
The welding arc is too long.
Reduce the length of the welding arc.
The angle of the electrode is
incorrect.
Electrode should not be inclined
less than 45° to the vertical face.
Joint preparation does not allow
correct electrode angle.
Allow more room in the joint for
manipulation of the electrode.
The electrode is too large for the
joint.
Use smaller gauge electrode.
Insufficient deposit time at the edge
of weave.
Pause for a moment at the edge
of the weave to allow weld metal
build-up.
The power source is set for MIG
(GMAW) welding.
Set the power source to MMA
(SMAW) mode.
Portions of the weld
run do not fuse to
the surface of the
metal or edge of the
joint.
Small electrodes used on a heavy
cold plate.
Use larger electrodes and preheat
the plate.
The welding current is too low.
Increase the welding current.
Wrong electrode angle.
Adjust the angle so the welding
arc is directed more into the base
metal.
Travel speed of the electrode is too
high.
Reduce the travel speed of the
electrode.
Scale or dirt on joint surface.
Clean the surface before welding.
Figure 84: Example of lack of fusion
1 Lack of side fusion, scale dirt, small electrode, 3 Lack of inter-run fusion amperage too low
2 Lack of fusion caused by dirt, electrode angle, 4 Lack of root fusion
incorrect, rate of travel too high