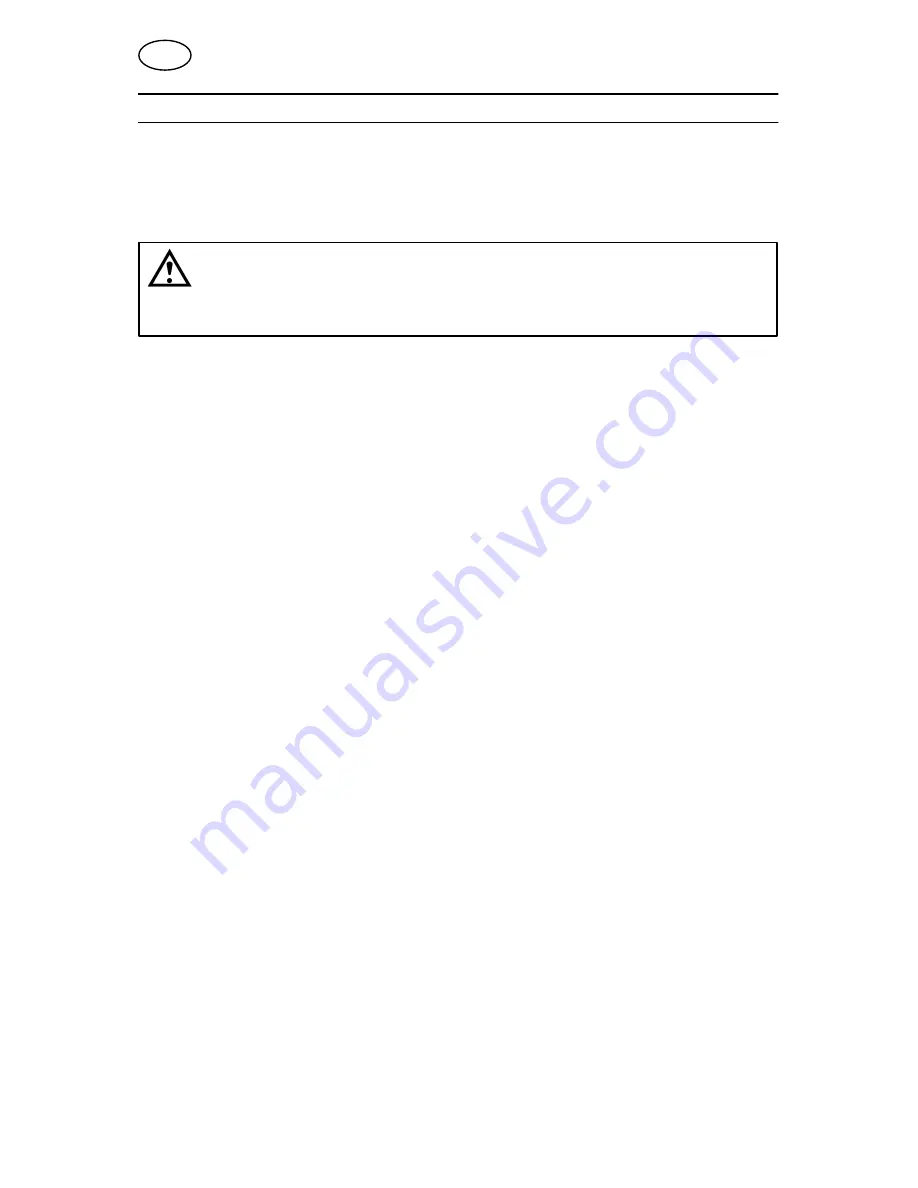
© ESAB AB 2012
- 14 -
bb01de
6
MAINTENANCE
Regular maintenance is important for safe, reliable operation.
Only those persons who have appropriate electrical knowledge (authorized
personnel) may remove the safety plates to connect or carry out service,
maintenance or repair work on welding equipment.
CAUTION
All guarantee undertakings from the supplier cease to apply if the customer attempts any
work to rectify any faults in the product during the guarantee period.
6.1
Welding power source
Check regularly that the welding power source is not clogged with dirt.
How often and which cleaning methods apply depend on:
S
welding process
S
operation time
S
placement
S
surrounding environment
The power source should be regularly blown clean using dry compressed air at
reduced pressure, see page 21. This should be done more frequently in dirty
environments.
Clogged or blocked air inlets and outlets otherwise result in overheating.
Orderingnumber for dust filter see page 26.
GB
Summary of Contents for Aristo 1000 AC/DC SAW
Page 2: ...2...
Page 17: ...ESAB AB 2012 17 bb01cable...
Page 18: ...ESAB AB 2012 18 bb01cable...
Page 19: ...ESAB AB 2012 19 bb01cable...
Page 20: ...ESAB AB 2012 20 bb01cable...
Page 21: ...ESAB AB 2012 Cleaning 21 bb01clean...
Page 22: ...ESAB AB 2012 Diagram 22 bb01e...
Page 23: ...ESAB AB 2012 Assembly instructions 23 bb01as...
Page 24: ...ESAB AB 2012 Connection instruction 24 bb01c...
Page 29: ...29 notes NOTES...
Page 30: ...30 notes NOTES...
Page 31: ...31 notes NOTES...