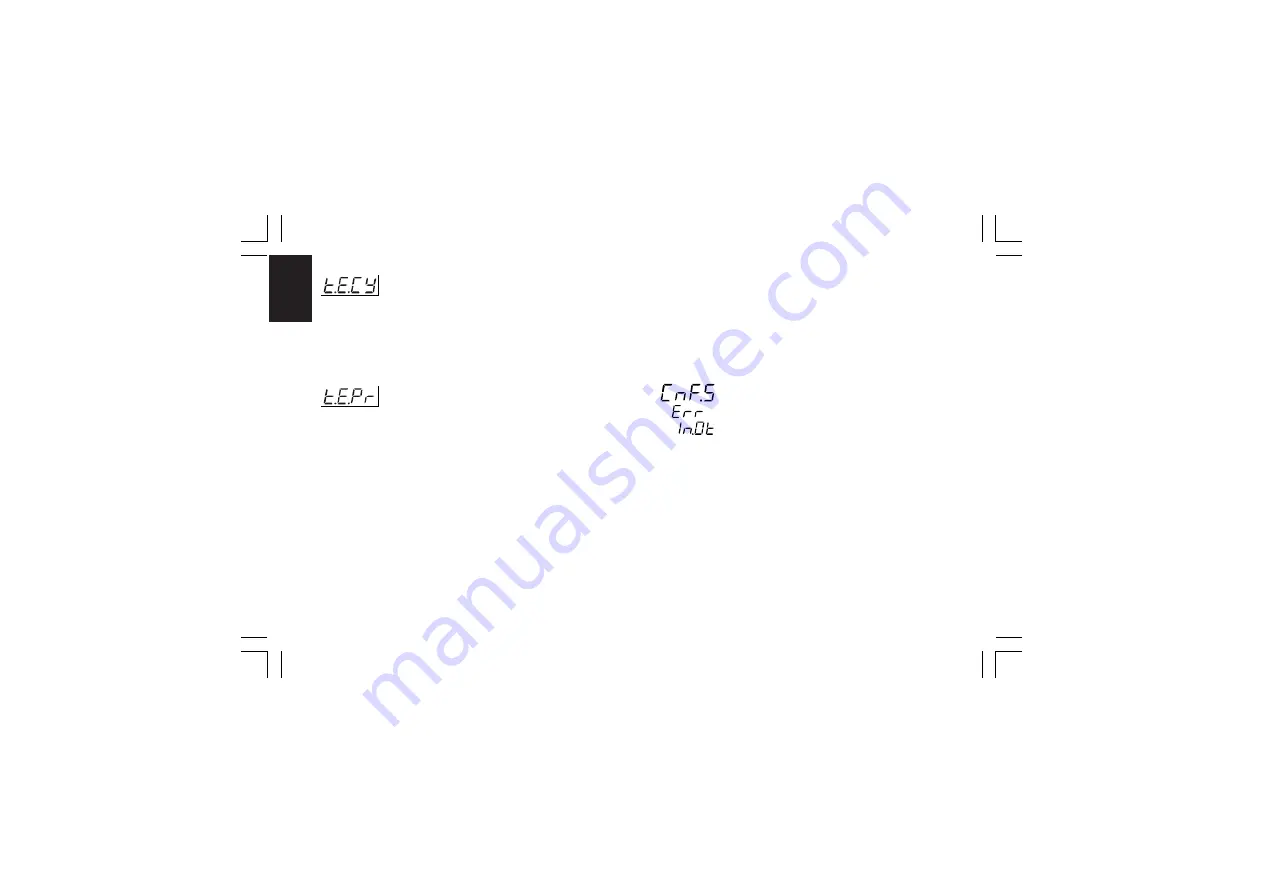
60
CnF. 6CnF. 6CnF. 6CnF. 6CnF. 6
- Time for the "End of cycle" annunciator
- Time for the "End of cycle" annunciator
- Time for the "End of cycle" annunciator
- Time for the "End of cycle" annunciator
- Time for the "End of cycle" annunciator
- [C.H11]
- [C.H11]
- [C.H11]
- [C.H11]
- [C.H11]
Available only when one of the Events is programmed as "End
of cycle" annunciator.
Range: from 0 to 240 s.
- Time for the "End of profile" annunciator
- Time for the "End of profile" annunciator
- Time for the "End of profile" annunciator
- Time for the "End of profile" annunciator
- Time for the "End of profile" annunciator
- [C.H12]
- [C.H12]
- [C.H12]
- [C.H12]
- [C.H12]
Available only when one of the Events is programmed as "End
of profile" annunciator.
Range: from 0 to 240 s. Above this limit, the display will show
"InF" and, at the end of the last programmed
cycle, the Event output is forced in ON
condition until a new RUN command is
detected.
General notes about configuration group 5
General notes about configuration group 5
General notes about configuration group 5
General notes about configuration group 5
General notes about configuration group 5
1) Digital input function selection should be “consistent” with other
configuration parameters otherwise this digital input will remain
unused.
2) Changing menu the device will check that the same function is
not assigned to more than one digital input (exception made for
digital inputs used for program selection), otherwise the display
will show:
Pushing the FUNC pushbutton, verify (and modify when
necessary) all the group 5 configuration parameters in order
to satisfy the previously described condition.
CnF. 5CnF. 5CnF. 5CnF. 5CnF. 5
XKP-1-D1.pmd
25/05/2006, 11.28
60