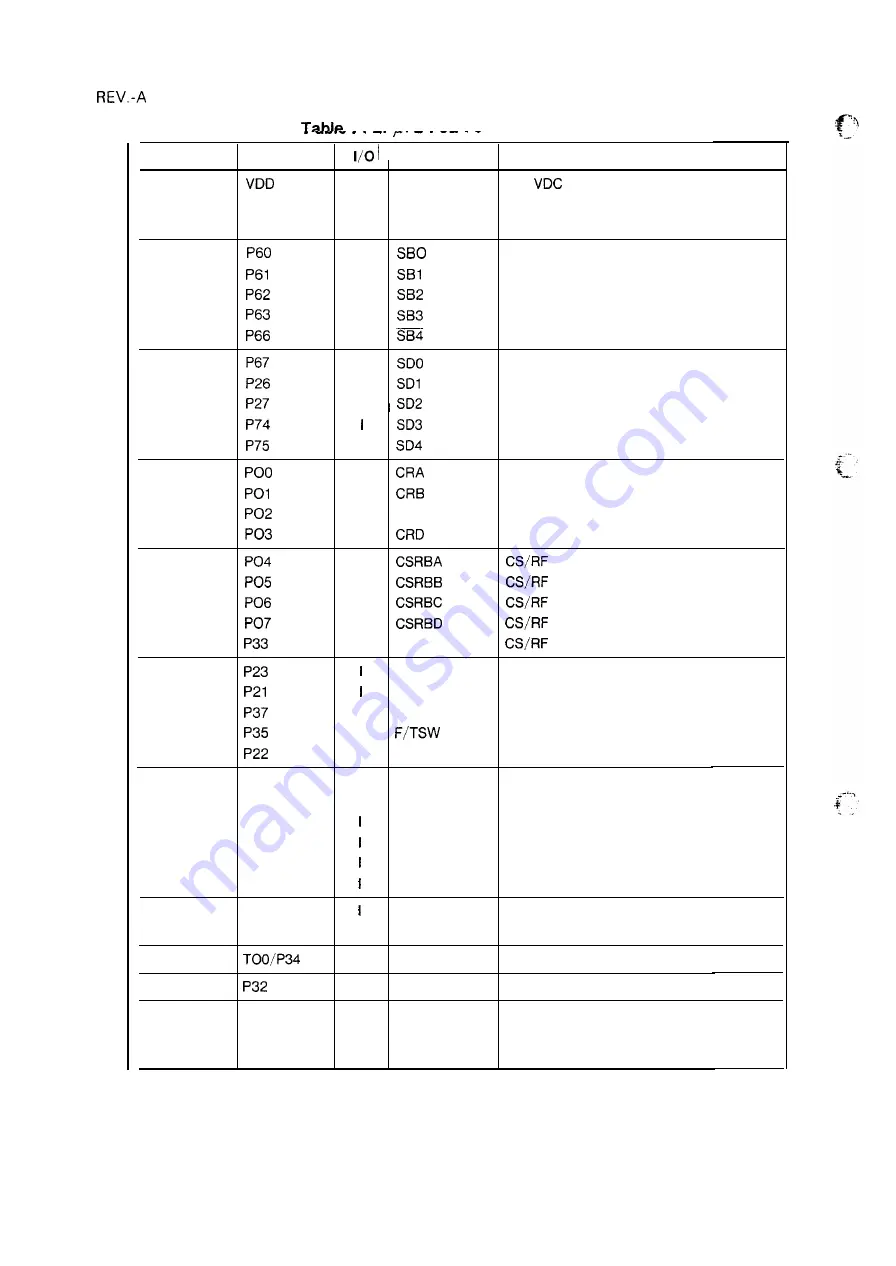
A-2. IIPD78213
Terminal Functions
Pin No.
Terminal
Signal Name
Description
49
I
+5
17, 32
Vss
—
Ground
48
1. c.
–
I
Ground
13
o
Switch bank O
12
o
Switch bank 1
11
o
Switch bank 2
10
o
Switch bank 3
7
o
Switch bank 4
6
I
Switch data O
42
I
Switch data 1
43
I
Switch data 2
53
Switch data 3
52
I
Switch data 4
62
o
CR motor coil A drive pulse
63
o
CR motor coil B drive pulse
64
o
CRC
CR motor coil C drive pulse
1
o
CR motor coil D drive pulse
2
o
motor coil A drive pulse
3
o
motor coil B drive pulse
4
o
motor coil C drive pulse
5
o
motor coil D drive pulse
47
o
CSRBENB
motor drive/hold switch s
39
CSHOM
CS sensor signal
37
PESW
PE sensor signal
61
I
GAPSW
PG sensor signal
59
I
F/T sensor signal
38
I
CRHOM
CR HP sensor signal
51
AVREF
I
Analog port reference voltage
50
AVSS
Analog port ground
57
ANO
TEMP
Printhead temperature detection
56
AN1
HDVLT
+35 V line voltage detection
55
AN2
VR2
VR2 adjustment value detection
54
AN3
VRI
VR1 adjustment value detection
16
x l
External oscillator (9.83 MHz)
15
x2
—
58
o
HPW
Printhead coil trigger pulse
46
o
P512
P-ROM (6A) address bus 15
9
RD
o
Read strobe
8
WR
o
W r i t e s t r o b e
3 5
A S T B
o
A L E
A d d r e s s l a t c h e n a b l e
A-4
Summary of Contents for LQ-1060
Page 1: ...EPSON TERMINAL PRINTER L Q 8 6 0 1 0 6 0 TECHNICAL MANUAL ...
Page 5: ...REVISION TABLE REVISION DATE ISSUED I CHANGE DOCUMENT I I 1st issue I v ...
Page 68: ...cc o REV A N N n 1 cc b I al cc u co n4 2 1 Figure 2 14 Main Switching 2 21 ...
Page 79: ...REV A Table 2 20 State of Module 1 1 I W stay E H H L H d O s H H 4 2 32 ...
Page 203: ...Figure 5 6 MONPS MONPSE Board Voltage Waveforms 5 17 ...
Page 204: ...REV A Fiaure 5 6 MONPS MONPSE Board Voltage Waveforms z L 5 18 ...
Page 205: ...Figure 5 6 MONPS MONPSE Board Voltage Waveforms 5 19 ...
Page 248: ...REV A A 3 DRAWINGS 3 J32 J TI g 4 Figure A 27 MONPS Board Component Layout A 34 ...
Page 250: ... 2 1 1 1 1 I A b 2 Ozaz 1202 C O ZZH Z UOEE vu I 1 Figure A 29 MONPS Board Circuit Diagram ...
Page 252: ...L t g Figure A 31 JUNMM Board Component Layout A 38 ...