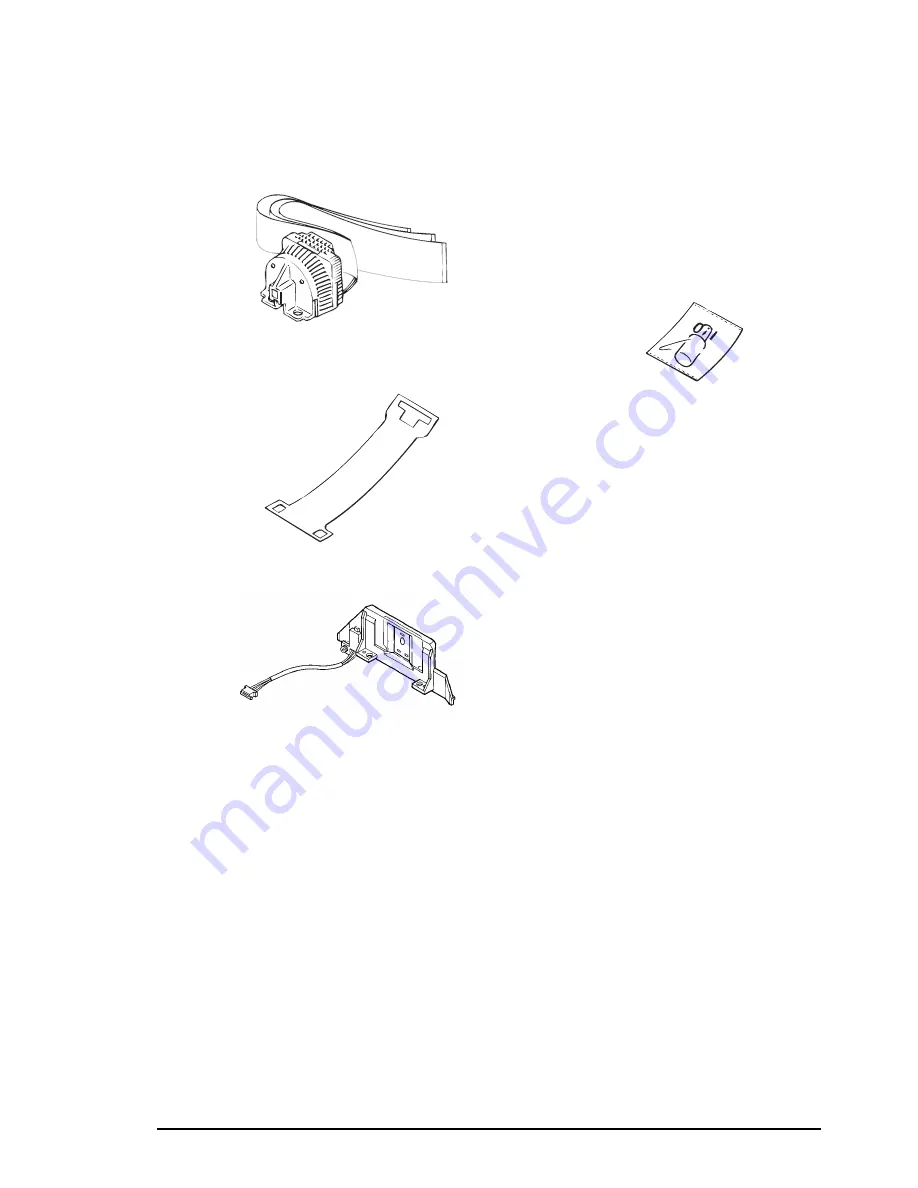
DISASSEMBLY AND ASSEMBLY
Rev. B
3-9
3.2.2 Printhead and Ribbon Mask Assembly Removal
The printhead can be changed without disassembling the entire unit.
Use the exclusive printhead kit for printhead exchange on the DFX-8500. When you receive the kit, check
that all of the following are included.
P r i n t h e a d U n i t
O i l ( O - 2 )
H e a d C a b l e P r o t e c t i o n S h e e t
R i b b o n M a s k A s s e m b l y
Figure 3-8. Printhead Kit
The description hereafter is the same as the above instruction Manual, so you may refer to this section or
to the Instruction Manual.
Summary of Contents for DFX-8500 - Impact Printer
Page 52: ......
Page 54: ......
Page 90: ......
Page 152: ......
Page 172: ......
Page 174: ......
Page 202: ......
Page 205: ...MAINTENANCE Rev B 6 3 Figure 6 2 Lubrication and Adhesive Diagram 1 ...
Page 206: ...DFX 8500 Rev B 6 4 Figure 6 3 Lubrication and Adhesive Diagram 2 ...
Page 207: ...MAINTENANCE Rev B 6 5 Figure 6 4 Lubrication and Adhesive Diagram 3 ...
Page 208: ......
Page 210: ......
Page 220: ......
Page 221: ......
Page 222: ......
Page 223: ......
Page 224: ......
Page 225: ...APPENDIX Rev B A 21 A 3 Component Layout Figure A 7 C204 MAIN Board Component Layout 1 ...
Page 226: ...DFX 8500 Rev B A 22 Figure A 8 C204 MAIN Board Component Layout 2 ...
Page 229: ...APPENDIX Rev B A 25 Figure A 13 C204 PSB Board Component Layout ...
Page 230: ...DFX 8500 Rev B A 26 Figure A 14 C204 PSE Board Component Layout ...
Page 236: ...DFX 8500 Rev B A 32 Figure A 16 Exploded Diagrams 1 ...
Page 237: ...APPENDIX Rev B A 33 Figure A 17 Exploded Diagrams 2 ...
Page 238: ...DFX 8500 Rev B A 34 Figure A 18 Exploded Diagrams 3 ...
Page 239: ...APPENDIX Rev B A 35 Figure A 19 Exploded Diagrams 4 ...
Page 240: ...DFX 8500 Rev B A 36 Figure A 20 Exploded Diagrams 5 ...
Page 241: ...APPENDIX Rev B A 37 Figure A 21 Exploded Diagrams 6 ...
Page 242: ...DFX 8500 Rev B A 38 Figure A 22 Exploded Diagrams 7 ...
Page 243: ...APPENDIX Rev B A 39 Figure A 23 Packing Material ...
Page 245: ...EPSON SEIKO EPSON CORPORATION ...