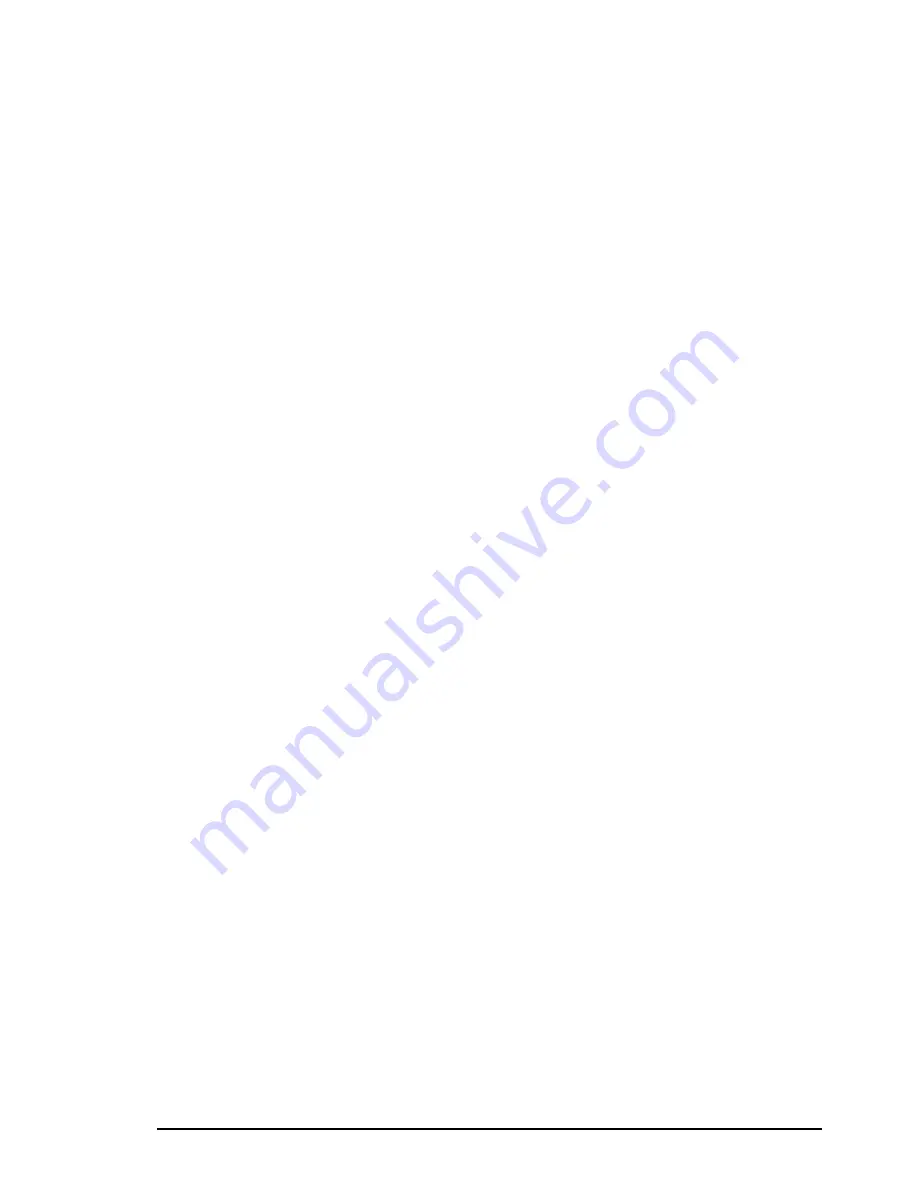
ADJUSTMENT
Rev. B
4-13
Step 1:
Remove the paper, ribbon cartridge, and ribbon mask holder from the printer. Then confirm the
ALPHA value written on the print head nose.
Step 2:
Close the top cover.
ALPHA Value Write Mode :
Step 3:
Turn the printer on while pressing the Tear Off, Micro Feed (v), and Front/Rear switches. At this
time the printer performs PG home position seek. and the carriage moves to the 15 column.
Step 4:
The panel indicates the current ALPHA adjustment value (Refer to Table 4-1.).
Step 5:
Write the ALPHA value written on the print head into the memory.
•
Press the Micro Feed (v) switch to increment value by +1.
•
Press the Micro Feed (^) switch to decrement the value by -1.
Step 6: 1) When you finish the adjustment (such as you have replaced the print head.), press the LF/FF
Load SW, then the ALPHA value is written to the EEPROM and finish the adjustment mode.
Then turn the power off and install the ribbon mask holder and the ribbon cartridge.
2) When you continue the BETA values write operation, press the Pause SW, then the ALPHA
value is written to the EEPROM and enter to the BETA values write mode.
BETA Values Write Mode :
Step 7:
Open the top cover and inset the 0.43 mm thickness gauge into the space between the platen
and the print head nose. (At this time, never shift the print head. If done it, return to Step 3.)
Step 8:
Contact the tension gauge to the hole of the thickness gauge and pull it straight to the right.
Step 9:
Hold the thickness gauge gradually with the print head nose by pressing the below switch.
•
Press the Micro Feed (v) switch to increment value by +1.
•
Press the Micro Feed (^) switch to decrement the value by -1.
The panel indicates the current BETA3’ adjustment value (Refer to Table 4-1.).
Step 10:
Set the BETA3’ value when the tension gauge indicates the 150 (135 - 165) gf, the tension gauge
can move to right in a degree.
Step 11:
After complete BETA3’ adjustment, press Pause SW to enter next step.
Step 12:
Close the print head nose to the platen by pressing the below switch.
•
Press the Micro Feed (v) switch to increment value by +1.
•
Press the Micro Feed (^) switch to decrement the value by -1
The panel indicates the current BETA2 adjustment value (Refer to Table 4-1.).
Step 13:
After complete BETA2 adjustment, press Pause SW to enter next step.
Step 14:
Inset the 0.43 mm thickness gauge into the space between the platen and the print head nose.
Step 15:
Hold the thickness gauge gradually with the print head nose by pressing the below switch.
•
Press the Micro Feed (v) switch to increment value by +1.
•
Press the Micro Feed (^) switch to decrement the value by -1.
The panel indicates the current BETA3 adjustment value (Refer to Table 4-1.).
Step 16:
After complete BETA3 adjustment, press Pause SW to enter next step.
Step 17:
Inset the 0.80 mm thickness gauge into the space between the platen and the print head nose.
Step 18:
Hold the thickness gauge gradually with the print head nose by pressing the below switch.
•
Press the Micro Feed (v) switch to increment value by +1.
•
Press the Micro Feed (^) switch to decrement the value by -1.
The panel indicates the current BETA4 adjustment value (Refer to Table 4-1.).
Step 19:
After complete BETA4 adjustment, press Pause SW then all of measured BETA values written
to the EEPROM, and turn the printer power off.
Note:
When either the measured BETA values (BETA2, BETA3, and BETA4) are out of range
(Refer to Table 4-1.) or the below formula is not satisfied, the printer sounds five beeps
and not written the values to the EEPROM.
Formula:
A1 = 0.43 / (BETA3 - BETA2)
and
0.0134 < A1 < 0.0187
A2 = (0.80 - 0.43) / (BETA4 -BETA3)
and
0.0115 < A2 < 0.0195
Step 20:
Install the ribbon mask holder and the ribbon cartridge.
Summary of Contents for DFX-8500 - Impact Printer
Page 52: ......
Page 54: ......
Page 90: ......
Page 152: ......
Page 172: ......
Page 174: ......
Page 202: ......
Page 205: ...MAINTENANCE Rev B 6 3 Figure 6 2 Lubrication and Adhesive Diagram 1 ...
Page 206: ...DFX 8500 Rev B 6 4 Figure 6 3 Lubrication and Adhesive Diagram 2 ...
Page 207: ...MAINTENANCE Rev B 6 5 Figure 6 4 Lubrication and Adhesive Diagram 3 ...
Page 208: ......
Page 210: ......
Page 220: ......
Page 221: ......
Page 222: ......
Page 223: ......
Page 224: ......
Page 225: ...APPENDIX Rev B A 21 A 3 Component Layout Figure A 7 C204 MAIN Board Component Layout 1 ...
Page 226: ...DFX 8500 Rev B A 22 Figure A 8 C204 MAIN Board Component Layout 2 ...
Page 229: ...APPENDIX Rev B A 25 Figure A 13 C204 PSB Board Component Layout ...
Page 230: ...DFX 8500 Rev B A 26 Figure A 14 C204 PSE Board Component Layout ...
Page 236: ...DFX 8500 Rev B A 32 Figure A 16 Exploded Diagrams 1 ...
Page 237: ...APPENDIX Rev B A 33 Figure A 17 Exploded Diagrams 2 ...
Page 238: ...DFX 8500 Rev B A 34 Figure A 18 Exploded Diagrams 3 ...
Page 239: ...APPENDIX Rev B A 35 Figure A 19 Exploded Diagrams 4 ...
Page 240: ...DFX 8500 Rev B A 36 Figure A 20 Exploded Diagrams 5 ...
Page 241: ...APPENDIX Rev B A 37 Figure A 21 Exploded Diagrams 6 ...
Page 242: ...DFX 8500 Rev B A 38 Figure A 22 Exploded Diagrams 7 ...
Page 243: ...APPENDIX Rev B A 39 Figure A 23 Packing Material ...
Page 245: ...EPSON SEIKO EPSON CORPORATION ...