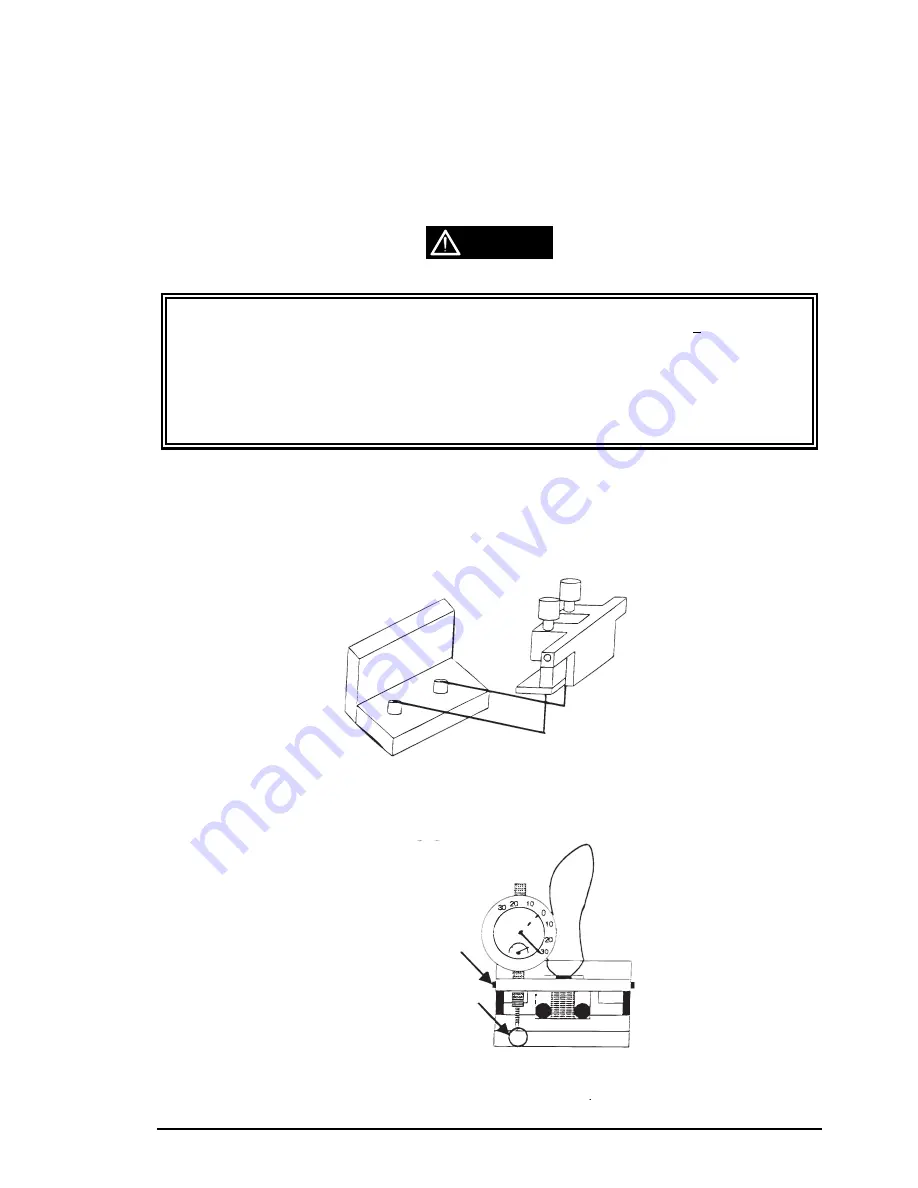
ADJUSTMENT
Rev. B
4-5
4.1.5 Carriage Guide Shaft Parallelism Adjustment
The rear carriage guide shaft must be parallel to the platen. If it is not, printing may be abnormal because
paper is not fed evenly at the left and right sides of the platen. A paper jam may occur. This adjustment is
required when the rear carriage guide shaft is removed during carriage mechanism disassembly, the
parallelism adjust lever is moved, or the platen is removed. Do not remove the printer mechanism (If remove
the printer mechanism from the lower case, the adjust value will be out of order when you reassemble the
printer mechanism to the lower case.) Also, it is necessary to remove the tension roller shaft before
performing this adjustment. (Refer to Section 3.2.6.7.)
The parallelism is adjusted so that the difference between the distances (from the rear carriage guide
shaft to the platen measured at the two positions shown in Figure 4-5) is less than + 0.015 mm. Since
this value is extremely small, you must use the two dial gauges, dial gauge base, and dial gauge
master supplied by EPSON. Do not adjust the parallelism using any other method.
;
Dial gauges (x 2) #F610 (Part No. B1019466)
;
Dial gauge base #F611 (Part No. B1019467)
;
Dial gauge master #F612 (Part No. B1019468).
Before performing the carriage guide shaft parallelism adjustment, you must assemble the two dial gauges,
dial gauge base, and dial gauge master to form one tool. Follow these steps:
Step 1: Attach the two thumb screws for the dial gauge base to the dial gauge master. To eliminate any play
between the dial gauge base and the dial gauge master, pull the tie band to secure the dial gauge
base and the dial gauge master before you securing the thumb screws.(Do procedure with two men.)
Step 2: Attach a dial gauge needle to the surface of the dial gauge master (approx. 2.00 mm depth), then
tighten the hexagonal screw securing the dial gauge to the dial gauge base.
CAUTION
Figure 4-5. Set Dial Gauge to Dial Gauge Base
1. Attach the gauge needle
to the master surface.
2. Tighten the hexagonal
screw.
Figure 4-6. Dial Gauge Set Up 1
Summary of Contents for DFX-8500 - Impact Printer
Page 52: ......
Page 54: ......
Page 90: ......
Page 152: ......
Page 172: ......
Page 174: ......
Page 202: ......
Page 205: ...MAINTENANCE Rev B 6 3 Figure 6 2 Lubrication and Adhesive Diagram 1 ...
Page 206: ...DFX 8500 Rev B 6 4 Figure 6 3 Lubrication and Adhesive Diagram 2 ...
Page 207: ...MAINTENANCE Rev B 6 5 Figure 6 4 Lubrication and Adhesive Diagram 3 ...
Page 208: ......
Page 210: ......
Page 220: ......
Page 221: ......
Page 222: ......
Page 223: ......
Page 224: ......
Page 225: ...APPENDIX Rev B A 21 A 3 Component Layout Figure A 7 C204 MAIN Board Component Layout 1 ...
Page 226: ...DFX 8500 Rev B A 22 Figure A 8 C204 MAIN Board Component Layout 2 ...
Page 229: ...APPENDIX Rev B A 25 Figure A 13 C204 PSB Board Component Layout ...
Page 230: ...DFX 8500 Rev B A 26 Figure A 14 C204 PSE Board Component Layout ...
Page 236: ...DFX 8500 Rev B A 32 Figure A 16 Exploded Diagrams 1 ...
Page 237: ...APPENDIX Rev B A 33 Figure A 17 Exploded Diagrams 2 ...
Page 238: ...DFX 8500 Rev B A 34 Figure A 18 Exploded Diagrams 3 ...
Page 239: ...APPENDIX Rev B A 35 Figure A 19 Exploded Diagrams 4 ...
Page 240: ...DFX 8500 Rev B A 36 Figure A 20 Exploded Diagrams 5 ...
Page 241: ...APPENDIX Rev B A 37 Figure A 21 Exploded Diagrams 6 ...
Page 242: ...DFX 8500 Rev B A 38 Figure A 22 Exploded Diagrams 7 ...
Page 243: ...APPENDIX Rev B A 39 Figure A 23 Packing Material ...
Page 245: ...EPSON SEIKO EPSON CORPORATION ...