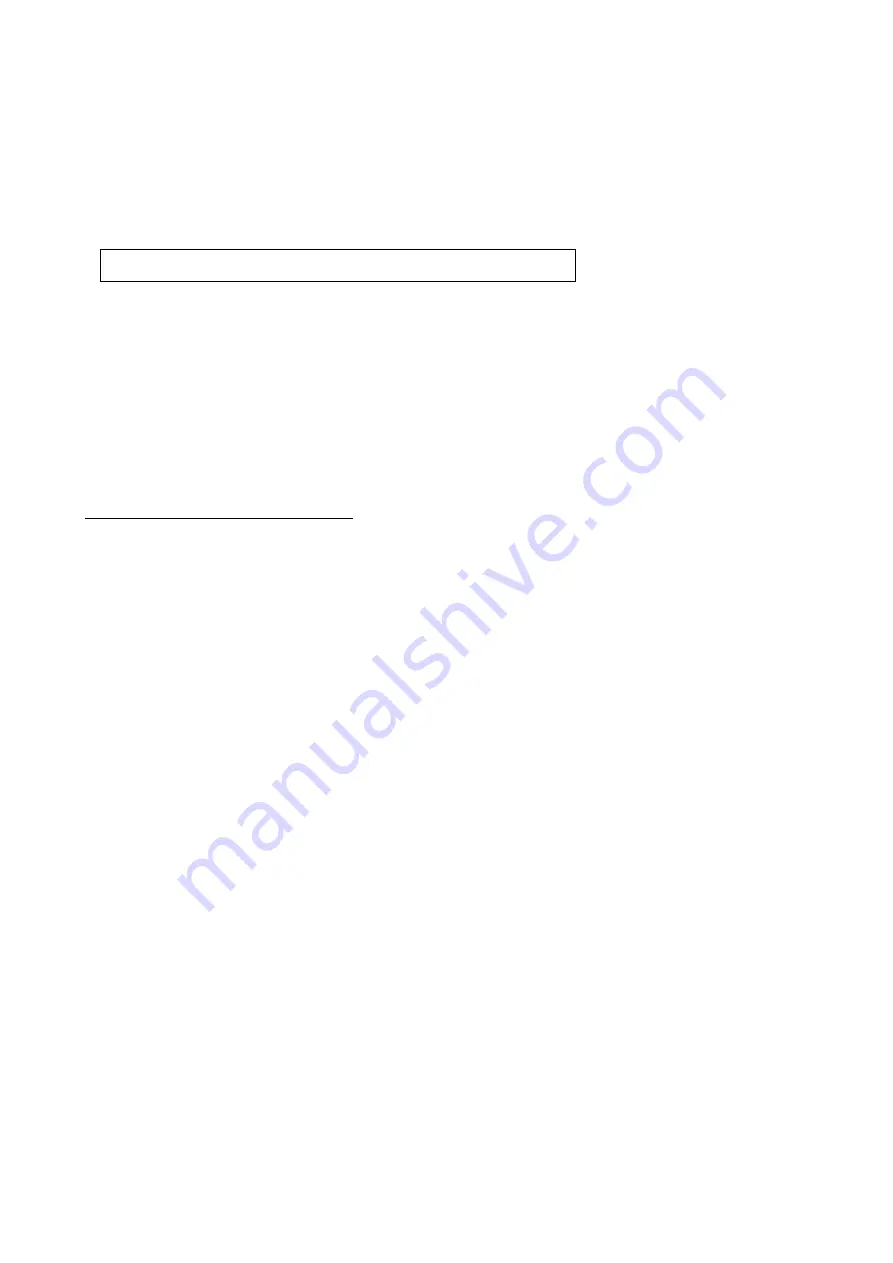
compressor, sealing valve, air extraction and nitrogen injection valves so that all the operations take
place in the right order and with the right timing.
The filling machine has been designed for use by qualified personnel, given that it could constitute a
source of danger to people. Do not leave the machine unsupervised when in use.
The machine should be placed on a firm, flat surface and blocked in place using the brakes on the
front castors.
2.1 PRELIMINARY CHECK The machine is supplied packaged and placed on a pallet, ready for
use. Once you have removed the packaging make sure that all the components are intact and inform
the supplier, if necessary, of any evident defects. Together with the machine you’ll receive this
instruction manual which forms an essential part of the same.
Check manually that the filling arm is not blocked, and if necessary free it of any obstacles
preventing its movement.
2.2 PRE-INSTALLATION CHECK: Before connecting up the machine make sure that the mains
voltage corresponds to that of the machine, as indicated on the data plate of the pump motor.
The electrical safety of this machine is only ensured if it is connected to a functioning earthing
connection system, installed in conformity with current electrical regulations. Checking and
installation of relevant electrical components must be performed by qualified personnel. The use of
multiple plugs or adaptors is not recommended; should the use of such be indispensable only use
products conforming to current safety standards, observing the current capacity and maximum power
limits shown
2.3 INSTALLATION. Position the machine on firm ground beside the wine storage tank and block it
in place using the brakes on the front castors.
Then connect the pump to the tank using the decanting tube. The tubes should be of the rigid and
reinforced type, and should be attached to the pump using hose clamps for the purpose, making sure
that there are no bottlenecks which might prevent the regular flow of liquid.
It is important to use the hose clamps in that they ensure the correct functioning of the pump and
prevent leaks of liquid which might cause damage to the pump itself or to those surrounding it.
One of the standard fittings installed on the pump is a hose connection fitting for tubes of d.20; upon
request the pump can be supplied with a hose connection fitting of d.30. The use of decanting tubes
of dimensions other than those indicated is not recommended in that they might impair the proper
functioning of the machine.
Proceed by checking that the switch on the control panel is in the central “0” position, and connect
the power supply cable of the control panel to the electricity socket.
At this point the compressor should start to move; if it does not, open the air release tap situated
above the compressor and close it again as soon as the compressor starts. If the compressor still fails
to start check the values indicated on the pressure gauges situated on the compressor and if they
indicate zero press the start button on the front of the compressor itself.
The compressor stops on its own as soon as it reaches the pressure in the tank. (with reference to the
maintenance operations of the compressor see the attached compressor manual).
Open the valve or the tap which the decanting tube is connected to, so as to enable the tubes to fill up
partially.
2. POSITIONING, CHECKING AND INSTALLATION
Summary of Contents for BB 20
Page 17: ......