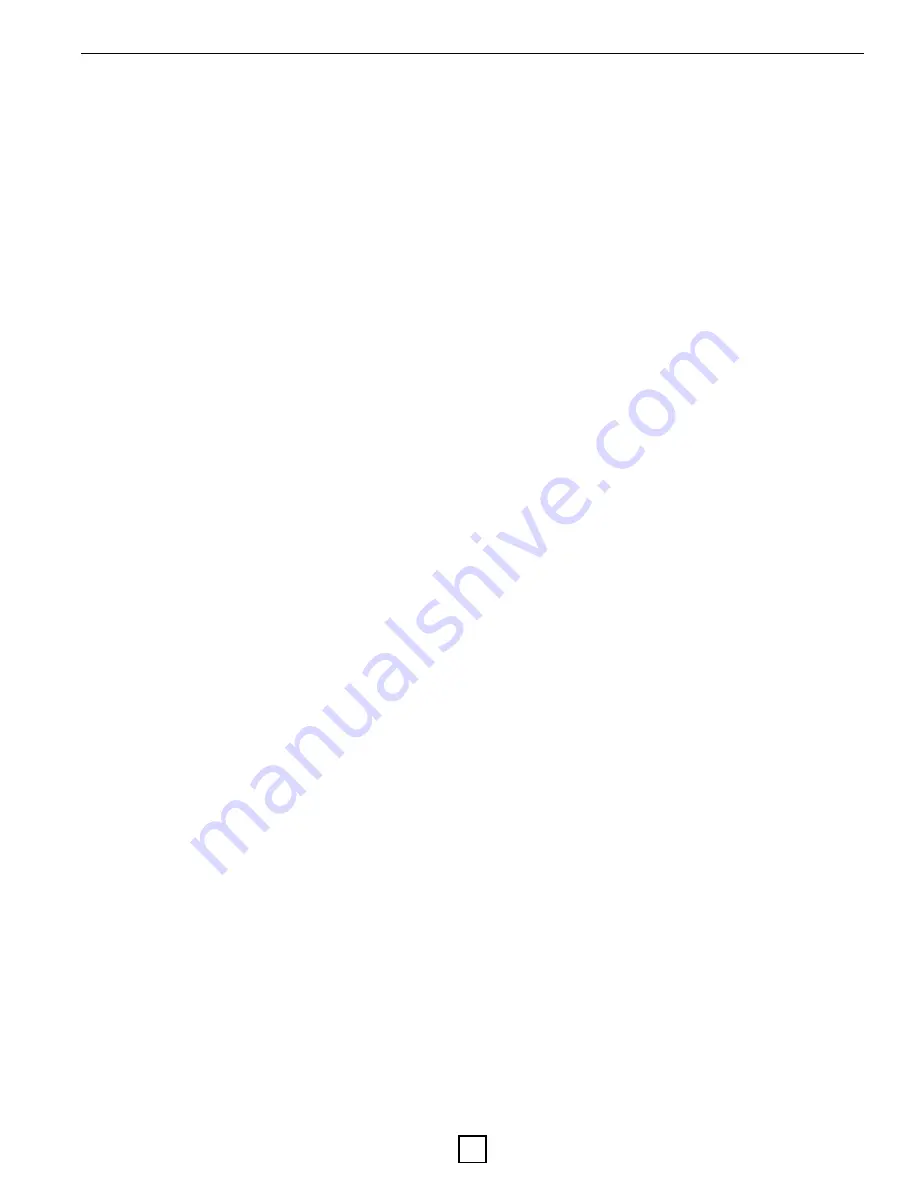
Enertech Global, LLC
25
WS Rev. E Models
Installation and Operations Manual
Section 8: Controls
Diagnostics
The lockout board includes five LEDs (Green-HP, Orange-LP,
Red-FS, Yellow-CO, Green-Status) for fast and simple control
board diagnosis. Refer to the LED Identification table for LED
function.
Lockout Board Jumper Selection
The lockout board includes four jumpers for field selection of
various board features.
Load/Source Temperature Sensing (FS)
When the FS jumper is installed (T1 and T4 monitored, FS
terminals ignored), the board operates in the load and source
heat exchanger temperature sensing mode. When the FS
jumper is removed, the board monitors the flow switch to
ensure adequate flow through the heat exchanger.
Factory
set, NOT field selectable.
Anti-Freeze (A-FRZ)
When the jumper is installed, the board operates in open
loop mode. The setpoint for the source heat exchanger freeze
sensor is 30°F. When the A-FRZ jumper is removed, the board
operates in the closed loop mode. The setpoint for the source
heat exchanger freeze sensor is 12°F.
Test Mode (TEST)
When the TEST jumper is installed, the board operates in the
normal mode. When the jumper is removed, the board
operates in test mode, which speeds up all delays for easier
troubleshooting. While in the test mode the T1 & T4 sensors
will be checked for the proper location based on
temperature. Sensors are swapped if T1>T4 in cooling or
T1<T4 in heating. This fault will only show up in the test
mode. When service is complete, the jumper must be
re-installed in order to make sure the unit operates with
normal sequencing delays. While the test jumper is removed,
the status light (bottom green) will remain off. If the test
jumper is not re-installed the control will revert to normal
mode after one (1) hour, green status light blinking.
Over/Under Voltage Disable (O/U)
When the O/U jumper is installed, the over/under voltage
feature is active. When the jumper is removed, the over/
under voltage feature is disabled. On rare occasions,
variations in voltage will be outside the range of the over/
under voltage feature, which may require removal of the
jumper. However, removal of the jumper could cause the unit
to run under adverse conditions, and therefore should not be
removed without contacting technical services. An over/
under voltage condition could cause premature component
failure or damage to the unit controls. Any condition causing
this fault must be thoroughly investigated before taking any
action regarding the jumper removal.
Likely causes of an over/under voltage condition include
power company transformer selection, insufficient entrance
wire sizing, defective breaker panel, incorrect 24VAC
transformer tap (unit control box), or other power-related
issues.
Sequence of Operation
The description below is based on Water-to-Water Units, Two
Stage Compressor. Timings assume the ASC timer is expired.
If the ASC timer is not expired the accessory, compressor,
and loop pump operation do not start until the ASC timer is
expired.
Heating 1st Stage
The Accessory (A) terminal output is energized after the
random start timer (10s-20s) expires. Next, after another 10s
delay, the compressor first stage and the loop pump(s) are
energized.
Heating 2nd Stage, (Y1, Y2)
After the Y2 call is received, the second stage of the
compressor is energized.
Cooling Operation
The reversing valve is energized for cooling operation.
Terminal “O” from the thermostat is connected to the
reversing valve solenoid.
Cooling 1st stage (Y1, 0)
The Accessory (A) terminal output is energized after the
random start timer (10s-20s) expires then the first stage
compressor and the loop pump(s) are energized 10 seconds
after A.
Cooling 2nd Stage (Y1, Y2, O)
After the Y2 call is received, the second compressor is
energized.