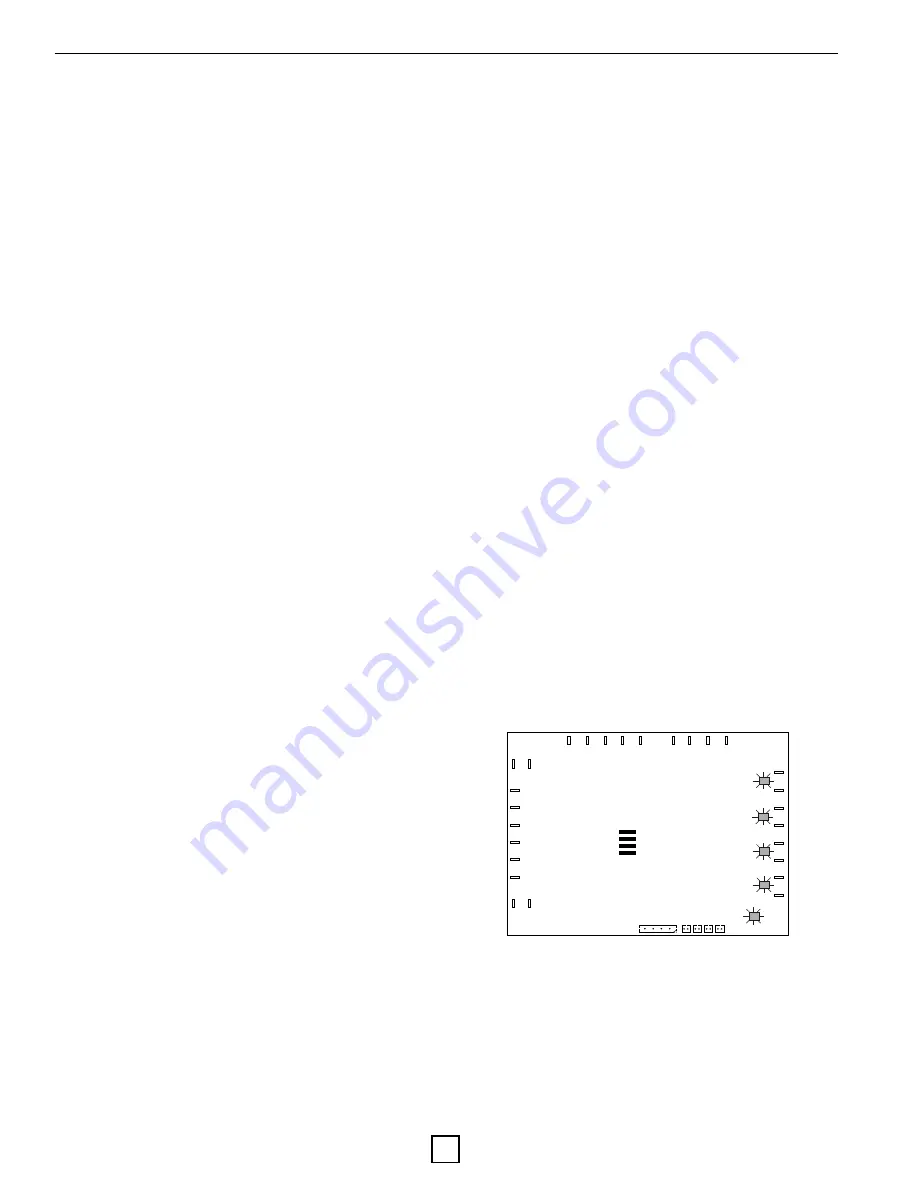
Enertech Global, LLC
22
WS Rev. E Models
Installation and Operations Manual
Features
Enertech Global geothermal heat pump controls leverage a
modular approach for controlling heat pump operation. The
control system uses a combination of printed circuit boards,
depending upon the features equipped in a particular unit.
This approach simplifies installation and troubleshooting, and
eliminates features that are not applicable for some units.
Microprocessor Features and Operations
Enertech Global geothermal heat pump controls provide a
unique modular approach for controlling heat pump
operation. The control system uses one, two, or three printed
circuit boards, depending upon the features of a particular
unit. This approach simplifies installation and troubleshooting,
and eliminates features that are not applicable for some
units.
A microprocessor-based printed circuit board controls the
inputs to the unit as well as outputs for status mode, faults,
and diagnostics. A status LED and LED(s) for each fault are
provided for diagnostics.
A removable low voltage terminal strip provides the
necessary terminals for thermostat connections. Some
models offer an additional removable terminal strip for
accessory wiring connections.
Startup/Random Start
The unit will not operate until all the inputs and safety
controls are checked for normal conditions. A ten to twenty
second random start delay is added at power up and
whenever a Y1 call is received. This avoids multiple units from
being energized at the same time after power loss or other
situations.
Short Cycle Protection (ASC)
A built-in five minute anti-short cycle (ASC) timer provides
short cycle protection of the compressor.
Component Sequencing Delays
Components are sequenced and delayed for optimum space
conditioning performance and to make any startup noise less
noticeable. There is a short delay between the blower motor
and the compressor start up.
Test Mode
The microprocessor control allows the technician to shorten
timing delays for faster diagnostics by removing the TEST
jumper located on the lockout board. It should be reinstalled
for normal operation after testing. The status LED will not be
illuminated during the TEST mode.
Resistance Heat Control
The resistance heat control module contains the appropriate
high-voltage control relays. Low voltage control signals from
the lockout board energize the relays in the resistance heat
module to engage backup resistance heat when necessary.
The lockout board offers a pass through W1 (1st Stage) and a
relay output for W2 (2nd Stage). See staging in sequence of
operation section.
Loop Pump Circuit Breakers
The loop pump(s) and HWG pump are protected by control
box mounted circuit breakers for easy wiring of pumps during
installation. Circuit breakers eliminate the need to replace
fuses.
Section 8: Controls
Safety Controls
The lockout board receives separate signals for high pressure,
low pressure, low load heat exchanger freeze, source heat
exchanger freeze, condensate overflow, and hot gas
temperature limit faults. Upon a continuous 30-second
measurement of all faults, except the high pressure fault, the
compressor operation is suspended. The high pressure fault is
immediate. The combination of LED(s) indicate each fault.
Once the unit is locked out (see fault retry below), an output
of 24VAC is energized on the “L” terminal for remote
indication of a fault at the thermostat.
Flow Switch - FS (If equipped - brazed plate only)
.
A flow switch ensures the source water maintains the
minimum required flow rate. This ensures that pumps are
working and water connections remain intact. The flow
switch will also trip when the source water begins to freeze,
providing additional protection. A Flow Switch is utilized on
units with a BPHE source coil. A Flow Switch is not included
on units utilizing a COAX source coil.
Electronic Condensate Overflow Protection (CO)
(If equipped - Packaged Units Only)
The control board utilizes an impedance sensing liquid sensor
at the top of the drain pan. When water touches the sensor,
CO fault occurs. If the fault is present for 30 continuous
seconds, the lockout board indicates a condensate overflow
fault has occurred.
If water touches the condensate overflow sensor for 30
continuous seconds, the compressor operation will be
interrupted. The control will go into fault retry mode. There
is no delay of switch monitoring at startup.
Low Pressure-LP:
If the low pressure switch is open
continuously for 30 seconds, the compressor operation will
be interrupted, and the control will go into fault retry mode.
At startup, the low pressure switch is not monitored for 30
seconds to avoid nuisance faults. (If the low pressure switch is
open before startup then the unit will not start upon
receiving an Y1 call and will lock out instead.)
Lockout Board Layout
CC
HP
Lockout
Board
HWG W2 G W1 Y2 R_2 R_1 C_2 C_1
AFRZ
TEST
O/V
STATUS
LP
FS
CO
A
C
R
Y1
L
O O
CCG
1
CCG
UART 1 2 3 4
FSW
High Pressure-HP:
If the high pressure switch opens, the
compressor operation will be interrupted, and the control will
go into fault retry mode. There is no delay between the time
the switch opens and the board entering into fault retry
mode. There is also no delay of switch monitoring at startup.
(If the high pressure switch is open before startup then the
unit will not start upon receiving an Y1 call and will lock out
instead.)