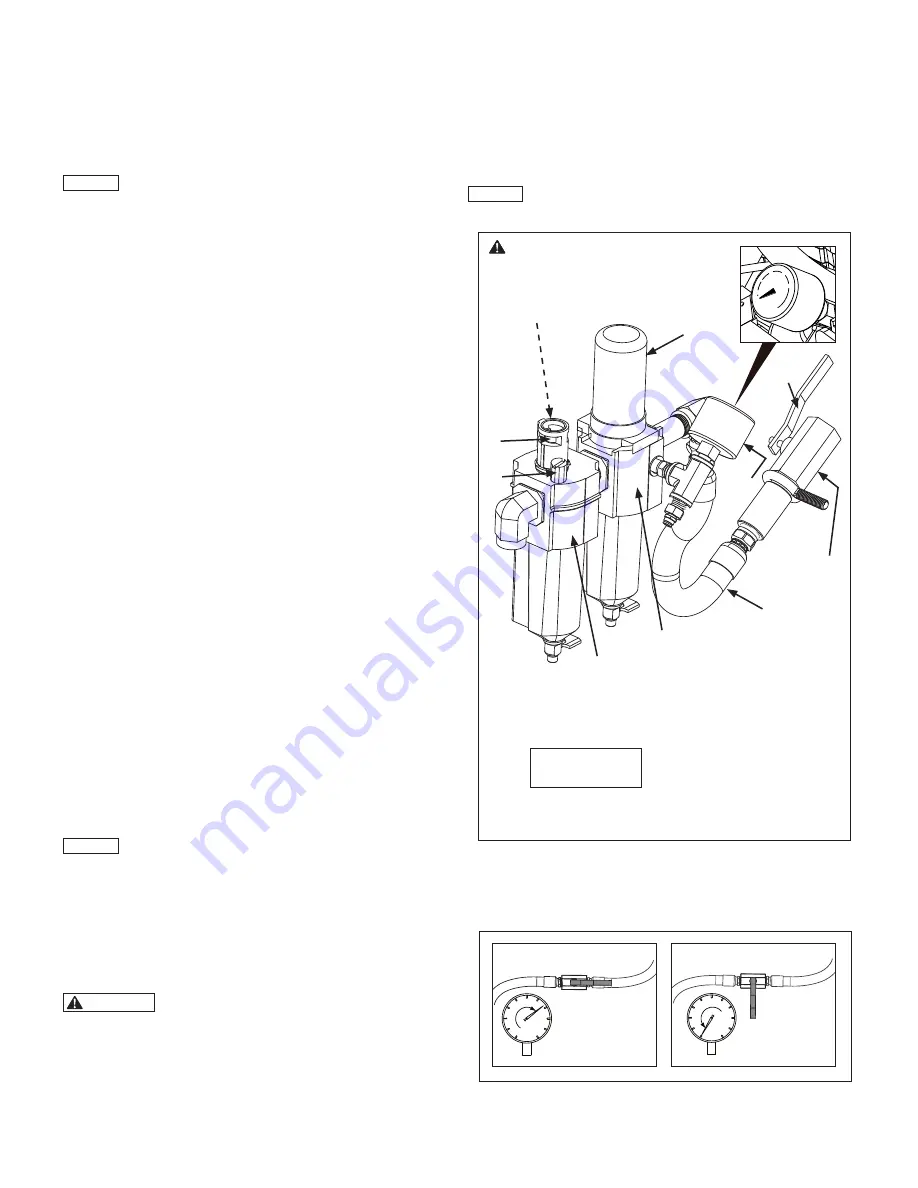
5
5.0 ASSEMBLY AND SETUP
5.1 Important Receiving Instructions
Visually inspect all components for shipping damage. Shipping
damage is not covered by warranty. If shipping damage is found,
notify carrier at once. The carrier is responsible for all repair and
replacement costs resulting from damage in shipment.
NOTICE
The jack rear access cover must be removed to gain
access to various components and service items discussed in
sections 5.2 through 5.4. Refer to Section 7.1 for cover removal
instructions.
5.2 Hydraulic Oil Level
Before using the jack or connecting the air supply, remove the
oil fill plug from the hydraulic reservoir and check the oil level.
Add additional hydraulic oil to reservoir if oil level is low. See
Section 7.3 for oil level diagram, oil specifications and additional
instructions.
5.3 Compressed Air Requirements
The compressed air system used with the jack must be capable
of providing 80 - 100 psi [5,5 - 6,9 bar] @ 130 CFM [3681 l/min].
The jack is equipped with an air filter/regulator assembly, which
consists of an air regulator, pressure gauge and moisture trap.
See Figure 3, items B, I and J.
A short hose connects the filter/regulator to the air-shuto
ff
valve.
The air inlet connection is a 1/2 inch NPT female thread. See
Figure 3, items K, L and M. Refer to Figure 4 for shut-o
ff
valve
positions.
For e
ffi
ciency of output and reliable operation, an air supply
line of not less than 0.82 inch [20,8 mm] internal diameter is
recommended. (Nominal Pipe Size - 3/4 inch pipe).
Check the air pressure gauge with the pendant UP button
depressed and the jack air motor running. Be sure there is NO
load on the cylinder. This will provide an accurate dynamic air
pressure reading.
The minimum dynamic air pressure required to operate the jack
will vary, but is typically about 50 to 60 psi [3,4 - 4,1 bar].
Approximately 90 to 100 psi [6,2 to 6,9 bar] dynamic air pressure
will be needed for the jack to achieve its rated 200 ton [1779 kN]
lifting capacity.
Lifting speed and torque can be adjusted using the knob located
at the top of the filter/regulator. To prevent damage to jack
pneumatic components, the regulator air pressure setting should
not exceed 120 psi [8,3 bar].
NOTICE
Pressure settings of above 120 psi [8,3 bar] will result
in reduced air motor life and will void the Enerpac product
warranty.
5.4 Air Lubrication
The jack pneumatic system is equipped with an automatic air
line lubricator. See Figure 3, items A, F, G and H. Lubricated air
is necessary to provide lubrication for the air motor and to help
prevent rust formation.
WARNING
Be certain that regulator air pressure gauge
indicates zero (0) psi/bar before removing lubricator fill plug.
Lubricant may spray from fill opening if fill plug is removed
while system is pressurized, even when air hose has been
disconnected and air shut-o
ff
valve is in the closed position.
Serious eye injury and/or skin penetration could result. If any
pressure is indicated, relieve pressure as described in
Section 7.2 of this manual.
Before using the jack, check the lubricant level in the sight gauge
on the air line lubricator. Add additional lubricant if low. Refer to
Section 7.6 for air lubricant recommendations and additional air
lubricator information.
After the air supply hose has been connected, observe the oil
flow through the oil drip window while the cylinder is in motion.
Verify that the lubricator drip speed is set at 4 to 5 drops per
minute.
NOTICE
Air motor must be running and cylinder must be
moving up or down when checking lubricator oil drip speed.
0
Figure 4, Air Shut-Off Valve Positions
OPEN
CLOSED
NOTICE:
NOTICE
CAUTION
WARNING
DANGER
Be sure air pressure gauge (item J)
indicates zero (0) psi/bar before
removing lubricator fill plug (item F).
Figure 3, Filter/Regulator, Air Line Lubricator
and Air Shut-off Valve
I
M
K
L
B
H
A
J
F
G
Key:
A. Air Line Lubricator
B. Air Filter/Regulator
(with moisture trap)
F. Lubricator Fill Plug
G Oil Drip Window
H. Oil Drip Speed Control
(inside oil drip housing)
I. Air Regulator Knob
J. Air Pressure Gauge
K. Air Inlet Hose
L. Air Inlet Connection
(1/2 inch NPT)
M. Air-shuto
ff
Valve
Note:
See Fig. 13
for items C, D and E.