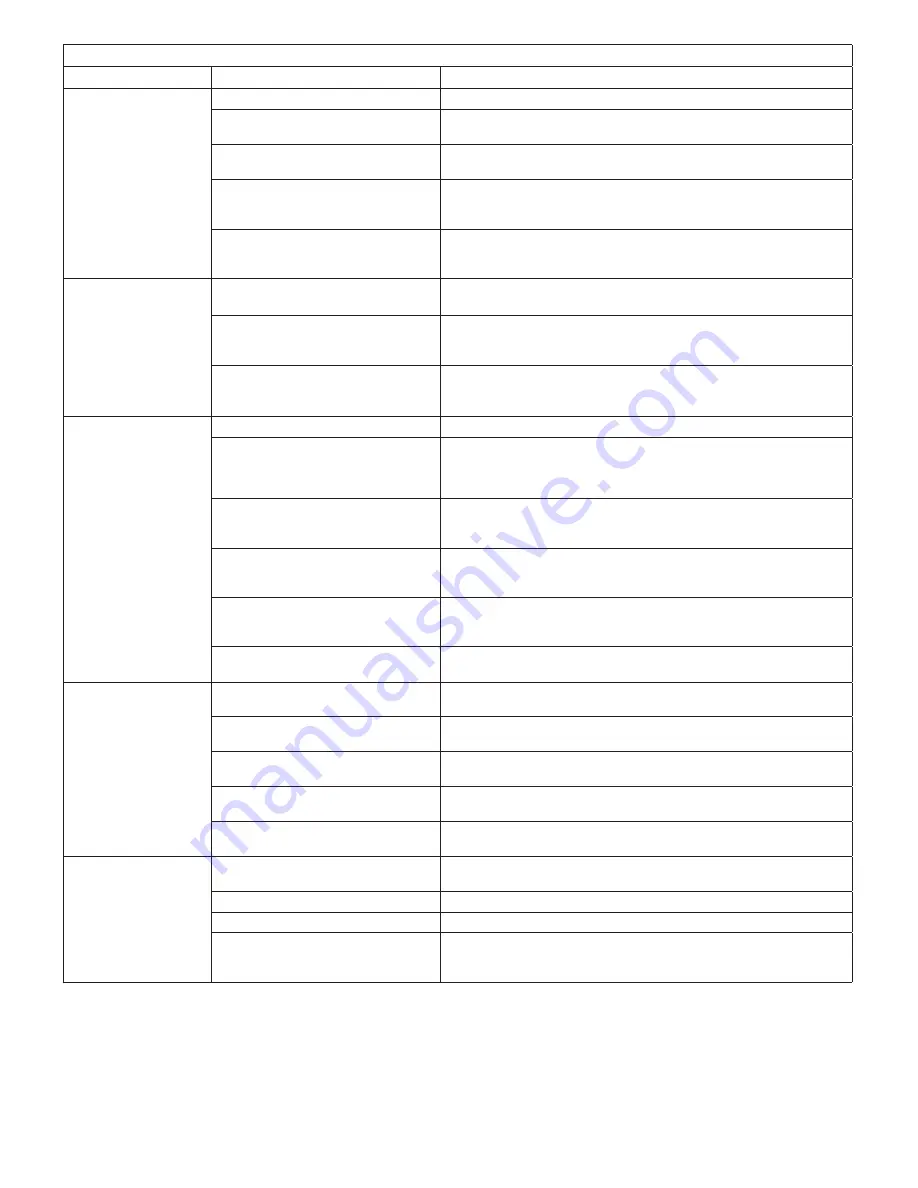
19
Table 10 - Troubleshooting Guide (Continued)
Symptom
Possible Cause
Solution
7. Cylinder stops
retracting when lock
nut contacts cylinder
housing. Does not fully
retract.
a. Lock nut not turning.
Refer to Step 9 of troubleshooting.
b. Lock nut spin-up sensor dirty or
plugged.
Have lock nut spin-up sensor checked by Enerpac Authorized Service
Center. Verify that sensor ports and air lines are not dirty or blocked.
c. Pneumatic system air line lubricator is
overfilled.
Drain excess lubricant from air line lubricant bowl. Do not operate jack for 8
to 12 hours to clear excessive lubricant from jack pneumatic control circuit.
d. Pneumatic control circuit components
leaking, worn, damaged or out of
adjustment.
Have pneumatic control circuit inspected by Enerpac Authorized Service
Center. Repair or replace components as required.
e. Hydraulic system components
leaking, worn, damaged or out of
adjustment.
Have hydraulic system inspected by Enerpac Authorized Service Center.
Repair or replace components as required.
8. Lock nut turns too
slowly when cylinder is
retracted.
Cylinder stops part-
way and will not fully
retract.
a. Lock nut not turning freely on cylinder
threads.
Clean and lubricate cylinder threads. Refer to Section 7.9.
b. Lock nut drive train components are
worn or loose.
Have Enerpac Authorized Service Center inspect condition of lock nut drive
chain, sprockets and related components. Repair or replace components
as required.
c. Cylinder lowering too fast.
Have Enerpac Authorized Service Center inspect the counterbalance
valve and related hydraulic system components. Adjust, repair or replace
components as required.
9. Lock nut not turning.
a. Cylinder threads need lubrication.
Clean and lubricate cylinder threads. Refer to Section 7.9.
b. Lock nut drive chain derailed, broken
or worn.
Inspect lock nut drive chain. Reinstall or replace chain as required.
Determine if other problems may have caused drive chain wear or failure.
c. Lock nut drive components are worn
or loose.
Have Enerpac Authorized Service Center inspect condition of lock nut drive
chain, sprockets and related components. Repair or replace components
as required.
d. Lock nut position sensors dirty or
plugged.
Check the spin-up sensor and Proximity-2 sensor. Verify that sensor ports
and air lines are not dirty or blocked. Refer to step 10 of troubleshooting if
ice has formed on or inside sensors.
e. Pneumatic control circuit components
leaking, worn, damaged or out of
adjustment.
Have pneumatic control circuit inspected by Enerpac Authorized Service
Center. Repair or replace components as required.
f. Hydraulic system components leaking,
worn, damaged or out of adjustment.
Have hydraulic system inspected by Enerpac Authorized Service Center.
Repair or replace components as required.
10. Ice formation at
pump air mu
ffl
er.
or
Ice formation at lock
nut position sensors.
a. Water in the air filter bowl.
Check air filter bowl for water. Drain water from bowl if present.
b. Air filter element dirty.
Clean or replace air filter element (inside filter/regulator).
c. Air line lubricator is empty.
Fill lubricant bowl with anti-freeze lubricant. Refer to Section 7.6 for
additional information.
d. Air line lubricator drip speed
incorrect.
Adjust the lubricator drip speed to 4 to 5 drops per minute.
e. Air supply contains excessive water.
Reduce amount of water in air supply.
11. Jack is di
ffi
cult to
roll on wheels.
a. Low tire inflation pressure.
Check tire inflation pressure. Add air if low.
Pressure should be 90 psi [6,2 bar].
b. Wheel bearings need lubrication.
Apply grease to wheel bearings. See Section 7.8.
c. Wheel lock nut out of adjustment.
Loosen lock nut until wheel rotates freely.
d. Caster wheels worn or stuck.
Inspect caster wheels for wear. Verify that each caster wheel rotates and
pivots freely. Lubricate bearings with a high quality wheel bearing grease.
Replace caster wheels if worn or damaged. See Section 7.8.