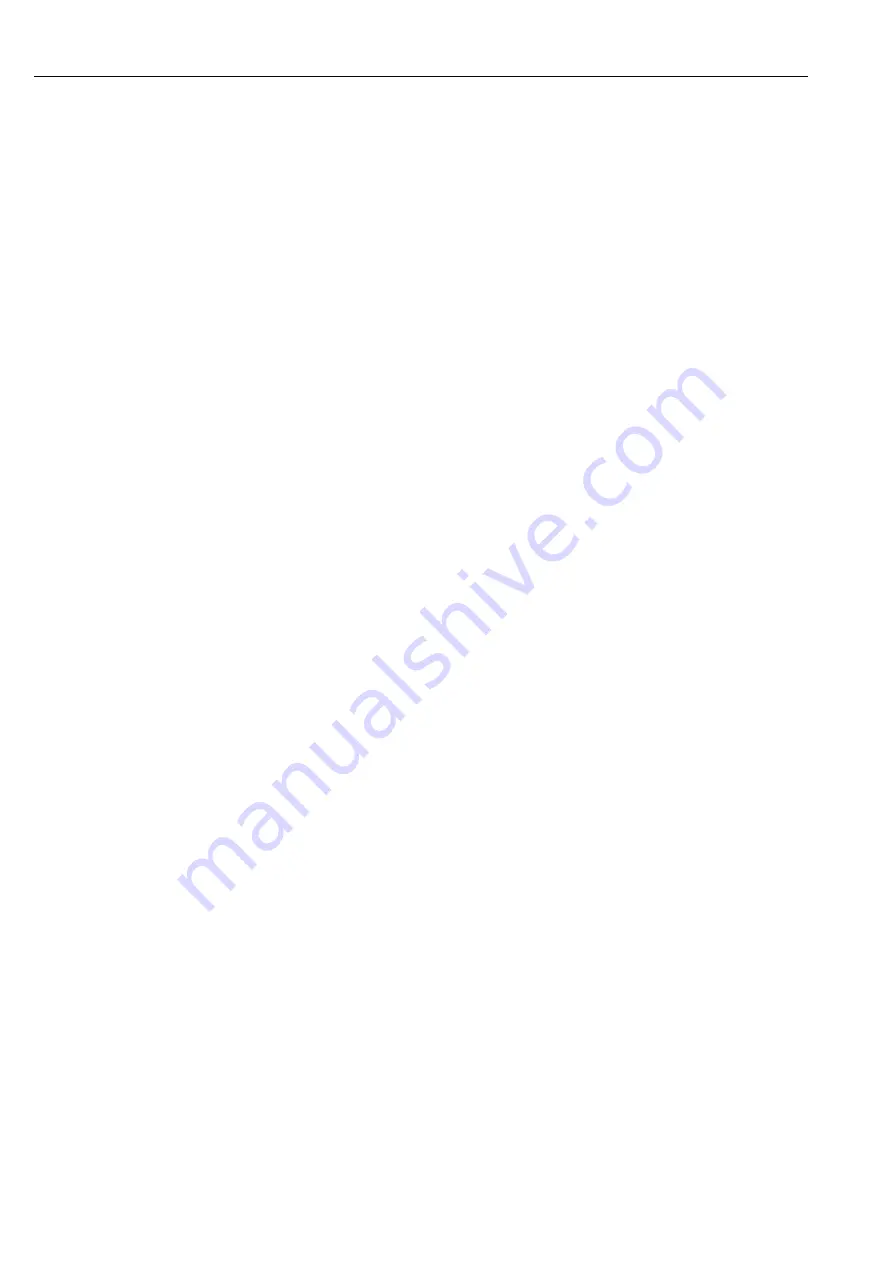
7 Maintenance
TopCal S CPC 300
110
EHauser
7.5
Maintenance of the process assembly
Weekly checks (recommended timeframe):
•
Check the upper section of the assembly for compressed air tightness and mechani-
cal damage.
•
Check the process connection for tightness against the process and mechanical
damage.
•
Check the compressed air lines and connections for tightness and mechanical dam-
age.
Annual checks (recommended timeframe):
•
External cleaning if necessary. To replace seals, the assembly must be clean, dry and,
if necessary, decontaminated.
•
With inductive feedback: test and, if necessary, set switching distance
•
Replacement of the seals not in contact with the medium (recommended: as neces-
sary, at least once a year)
•
Replacement of seals in contact with the medium (at least once a year, no further rec-
ommendations possible, as extremely dependent on process, material and level of
assembly use)
•
End test after completion of maintenance work:
– Assembly moves to measuring and service position?
– Maintenance and measuring feedback signals available? (Check using the
CPM 153 status messages)
– Process connection and compressed air connections tight?
– Does the meter display plausible values?
Replacement of the sealing elements is dependent on the type of assembly. Instructions
for replacement is contained in the appropriate service kit. You can find the necessary
service kit in the operating instructions of your assembly.
7.6
Maintenance of the control unit CPG 300
Weekly checks (recommended timeframe):
•
Check the inside of the compressed air connections for tightness:
– Pneumatic valves
– Pump drive
– Pressure switch.
•
Check level of buffer and cleaning solutions. Top up if necessary.
•
Check the multihose connections of the CPG 300 and assembly for tightness.
Annual checks (recommended timeframe):
•
Retighten the terminals in the cabinet.
•
Also check that the interior and the PCBs are clean, dry and free of corrosion.
– If not: check the seals, screw unions and pumps for leaks and breaks).
•
Test of the level measurement for buffer and cleaner bottles.
•
Replacement of pump sealing elements. Use the sealing kit in the spare parts list on
page 129. The sealing kit contains the appropriate instructions.
!
Note!
•
If there is frequent calibration or cleaning, it may be necessary to replace the pump
seals more often.
•
After maintenance work on the pump, check the conveyed volume by taking
measurements at the outlet.