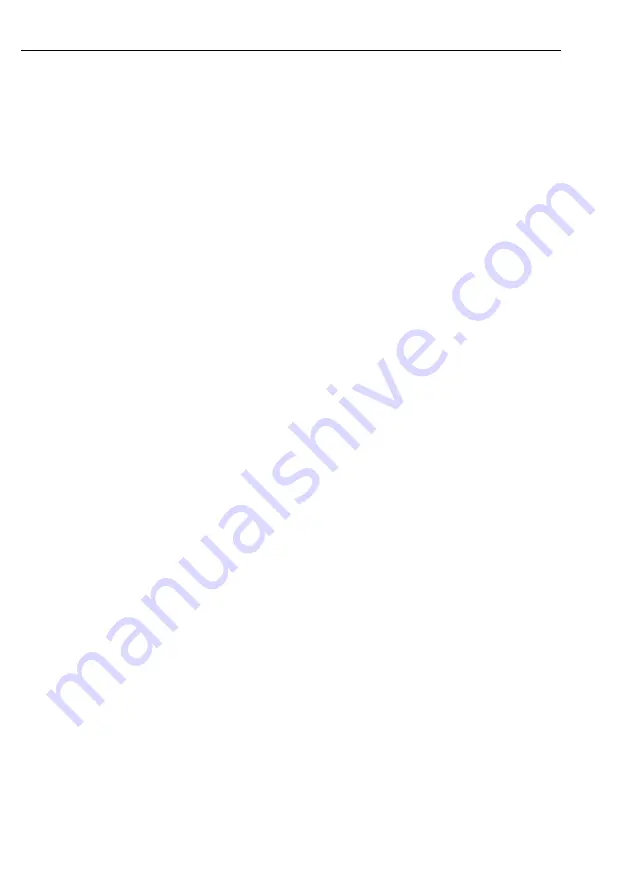
Safety instructions
Proline Prowirl 73
4
Hauser
1
Safety instructions
1.1
Designated use
• The measuring device is used to measure the volume flow of saturated steam, superheated
steam, gases and liquids. If the process pressure and process temperature are constant, the
measuring device can also output the flow as the calculated mass flow and corrected volume
flow.
• Any use other than that described here compromises the safety of persons and the entire
measuring system and is, therefore, not permitted.
• The manufacturer is not liable for damage caused by improper or non-designated use.
1.2
Installation, commissioning and operation
• The measuring device must only be installed, connected, commissioned and maintained by
qualified and authorized specialists (e.g. electrical technicians) in full compliance with the
instructions in these Brief Operating Instructions, the applicable norms, legal regulations and
certificates (depending on the application).
• The specialists must have read and understood these Brief Operating Instructions and must
follow the instructions they contain. If you are unclear on anything in these Brief Operating
Instructions, you must read the Operating Instructions (on the CD-ROM). The Operating
Instructions provide detailed information on the measuring device.
• The measuring device should only be installed in a de-energized state.
• Repairs may only be performed if a genuine spare parts kit is available and this repair work is
expressly permitted.
• If performing welding work on the piping, the welding unit may not be grounded by means
of the measuring device.
1.3
Operational safety
• The measuring device is designed to meet state-of-the-art safety requirements, has been
tested, and left the factory in a condition in which it is safe to operate. Relevant regulations
and European standards have been observed.
• Observe the technical data on the nameplate!
• The technical staff must ensure that the measuring device has been correctly wired and
grounded as per the wiring diagrams.
• With regard to special fluids, including fluids used for cleaning, Hauser will be happy
to assist in clarifying the corrosion-resistant properties of wetted materials.
However, minor changes in temperature, concentration or in the degree of contamination in
the process may result in variations in corrosion resistance. Unsuitable material can lead to
leakage of corrosive process media and injure personnel and/or cause damage in the plant.
For this reason, Hauser does not accept any responsibility with regard to the
corrosion resistance of wetted materials in a specific application. The user is responsible for
the choice of suitable wetted materials in the process. A sensor version which allows the
sensor housing be monitored should be used for critical fluids.