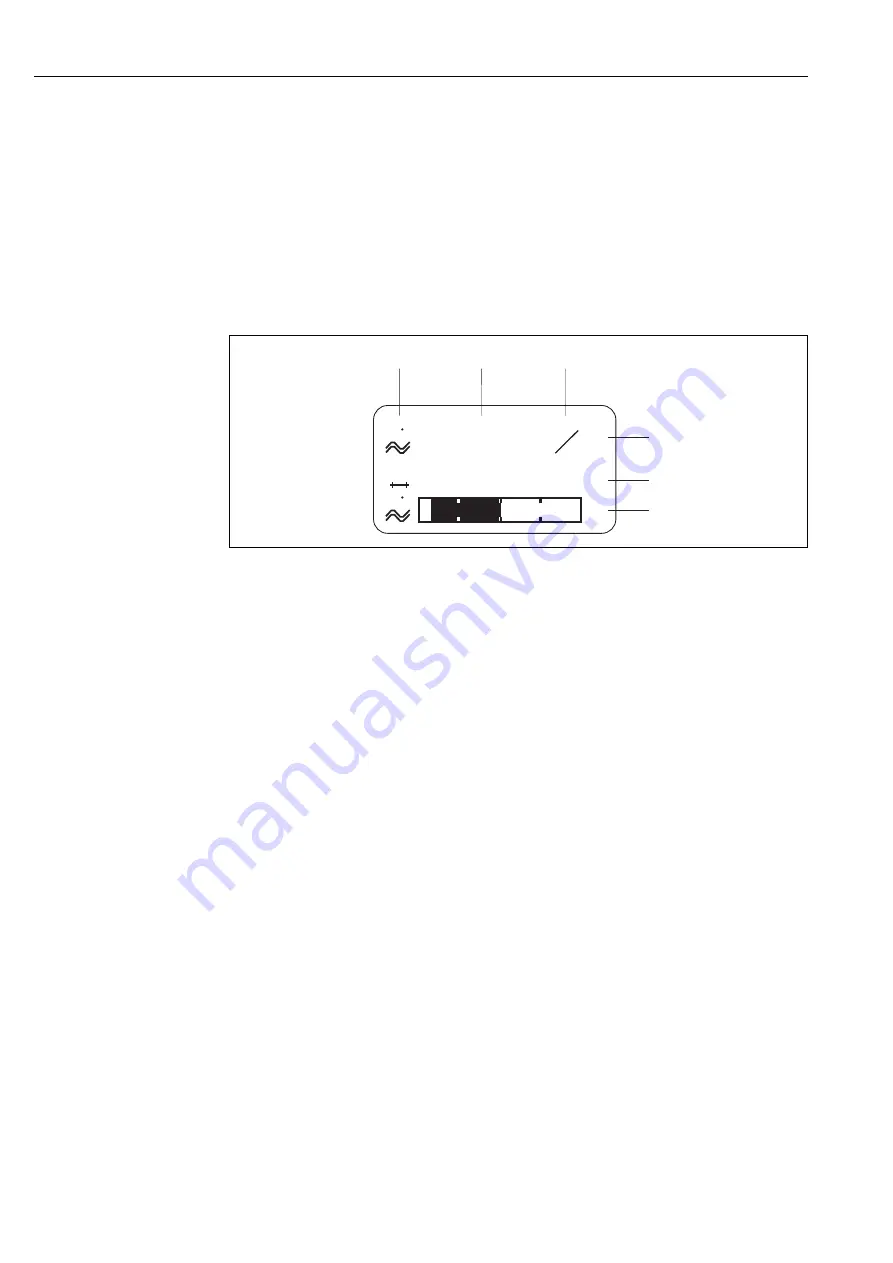
Operation
Proline Promag 55 FOUNDATION Fieldbus
54
Hauser
5.2.2
Display (operating mode)
The display area consists of three lines in all; this is where measured values are displayed, and/or
status variables (direction of flow, bar graph, etc.). You can change the assignment of display lines
to variables at will in order to customize the display to suit your needs and preferences (
→
see the
"Description of Device Functions" manual).
Multiplex mode:
A maximum of two different display variables can be assigned to each line. Variables multiplexed in
this way alternate every 10 seconds on the display.
Error messages:
Display and presentation of system/process errors
a0001173
Fig. 41:
Typical display for normal operating mode (HOME position)
1
Main line shows main measured values, e.g. flow
2
Supplementary line shows supplementary measured or status variables, e.g. totalizer reading.
3
Information line shows additional information on measured or status variables,
e.g. bar graph representation of the full scale value attained by the flow rate
4
"Info icons" field shows additional information in the form of icons on the measured values displayed. A complete
overview of all icons and their meaning can be found on
5
"Measured values" field shows the current measured values
6
"Engineering unit" field shows the engineering units and time units defined for the current measured values.
!
Note!
In the HOME position, you can use the
OS
keys to call up a list containing the following
information:
• Totalizer values (including overflow)
• Tag name (DEVICE PD-TAG)
OS
key
→
queries individual values in the list
Simultaneously press Esc key (
X
)
→
Return to the HOME position
1
4
5
6
2
3
+24.502
+1863.97
x
x
y
y
–50
+50
%
v
v
3
S