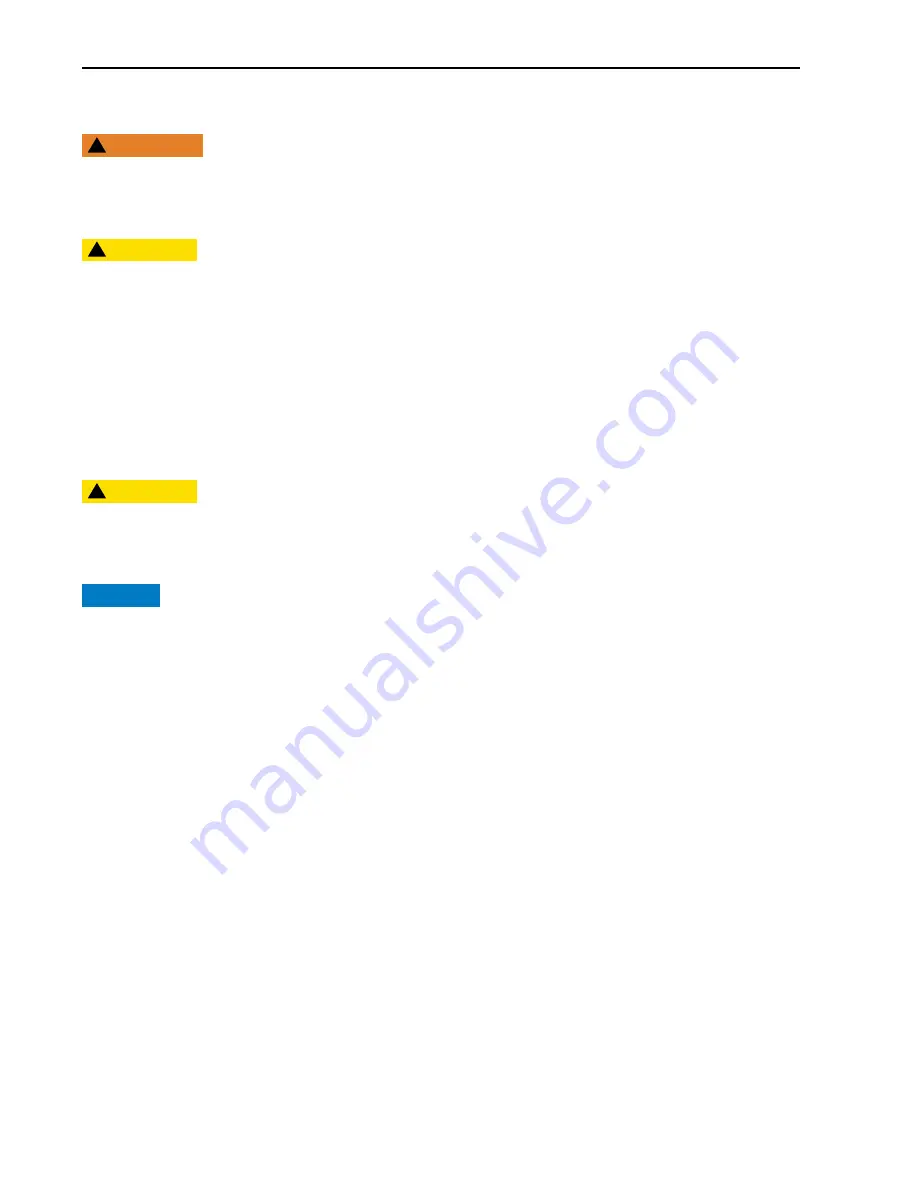
Maintenance
Liquiline System CAT860
28
Hauser
11
Maintenance
WARNING
!
Electrical voltage
Possible risk of serious or fatal injury
‣
De-energize the device before opening it.
CAUTION
!
Risk of injury/infection from medium leakage or unclean filter
‣
Before carrying out any maintenance work, ensure that the automatic cleaning function is
deactivated
‣
Before carrying out any maintenance work, ensure that the sample line is unpressurized and
that it is empty and has been rinsed.
‣
Clean the filter immediately every time it is removed from the process; only store cleaned
filters.
11.1
Cleaning
CAUTION
!
Risk of injury from cleaning solutions
‣
Wear protective clothes, goggles, and protective clothing.
‣
When disposing of unused cleaning solution, please comply with the local regulations.
NOTICE
Prohibited cleaning agents
Danger of damaging the housing surface or housing seal!
‣
For cleaning purposes, never use concentrated mineral acids or bases.
‣
Never use organic cleaners such as benzyl alcohol, methanol, methylene chloride, xylene or
concentrated glycerol cleaner.
‣
Never use high-pressure steam for cleaning purposes.
11.1.1 Housing
Only clean the front of the housing with commercially available cleaning agents.
The front is resistant to the following as per DIN 42 115:
• Ethanol (short periods)
• Diluted acids (max. 2% HCl)
• Diluted bases (max. 3% NaOH)
• Soap-based household cleaners
Summary of Contents for Liquiline System CAT860
Page 2: ......
Page 41: ...Liquiline System CAT860 Endress Hauser W Warnings 4 Weight 38 Wiring 21 ...
Page 42: ...Liquiline System CAT860 42 ...
Page 43: ......