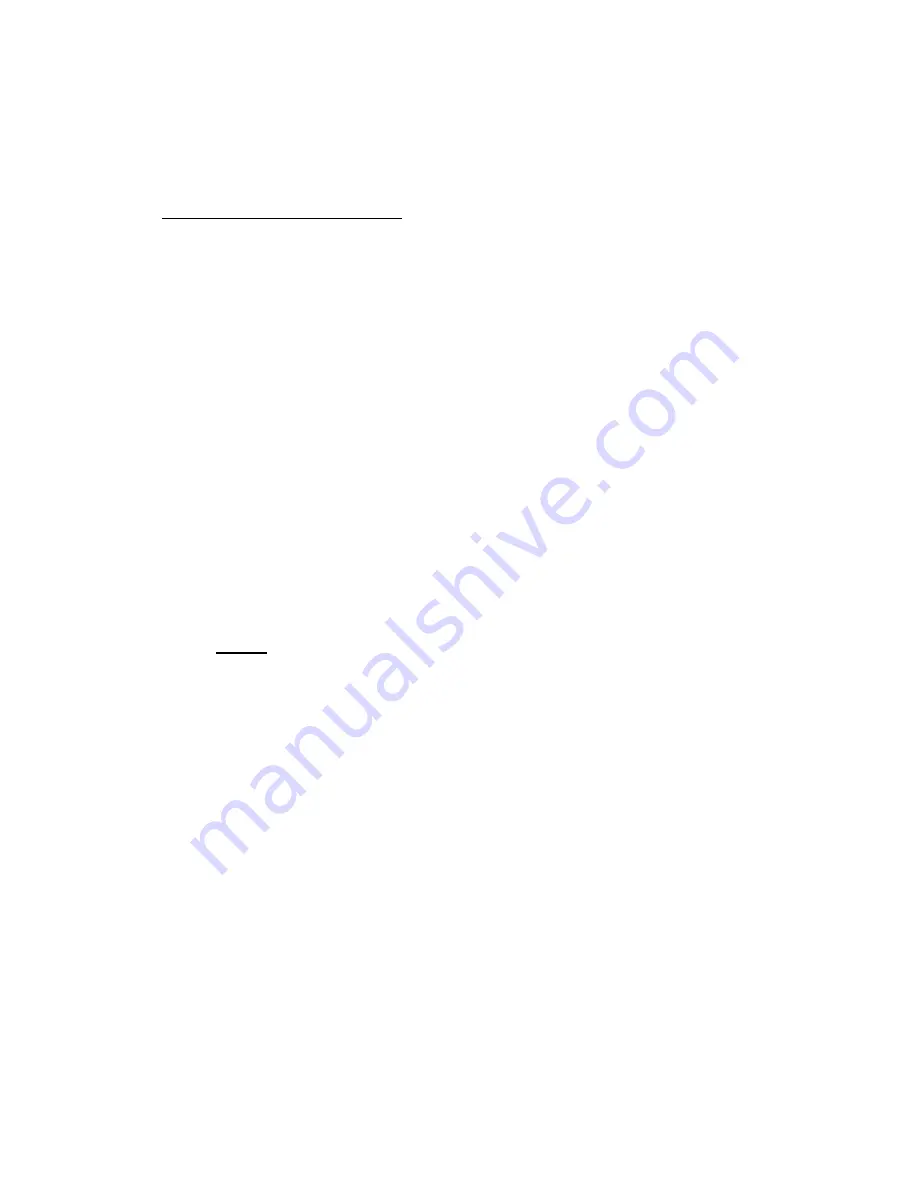
Page 6
SPCL36104-S Suction System
2.15
Run the system “dry” (without media) as described in Section 5.0. This step is important to
verify that the system is ready for media.
2.16
ABRASIVE MEDIA LOADING
This system is designed to use aluminum oxide.. The amount of media needed to operate the
system is approximately 5 cubic feet. With the optional Makeup Hopper, 10 cubic feet of
media is required. Changes may be required before the system is capable of using a different
type or size of media.
To fill the system, the following procedure should be followed:
2.16.1 Press the red “SYSTEM OFF” pushbutton.
2.16.2 Open the abrasive loading door located on top of the Storage Hopper. Fill the Storage
Hopper until the media is up to the bottom of the screen inside the hopper.
2.16.3 (Optional) Open the Makeup Hopper door. The Makeup Hopper may be filled to the
top.
2.16.4
Close and secure the Storage Hopper, Reclaimer, and Media Makeup Hopper doors.
2.16.5 Press the green “SYSTEM ON” pushbutton.
NOTE:
Never let the Storage Hopper media level get below one half full.