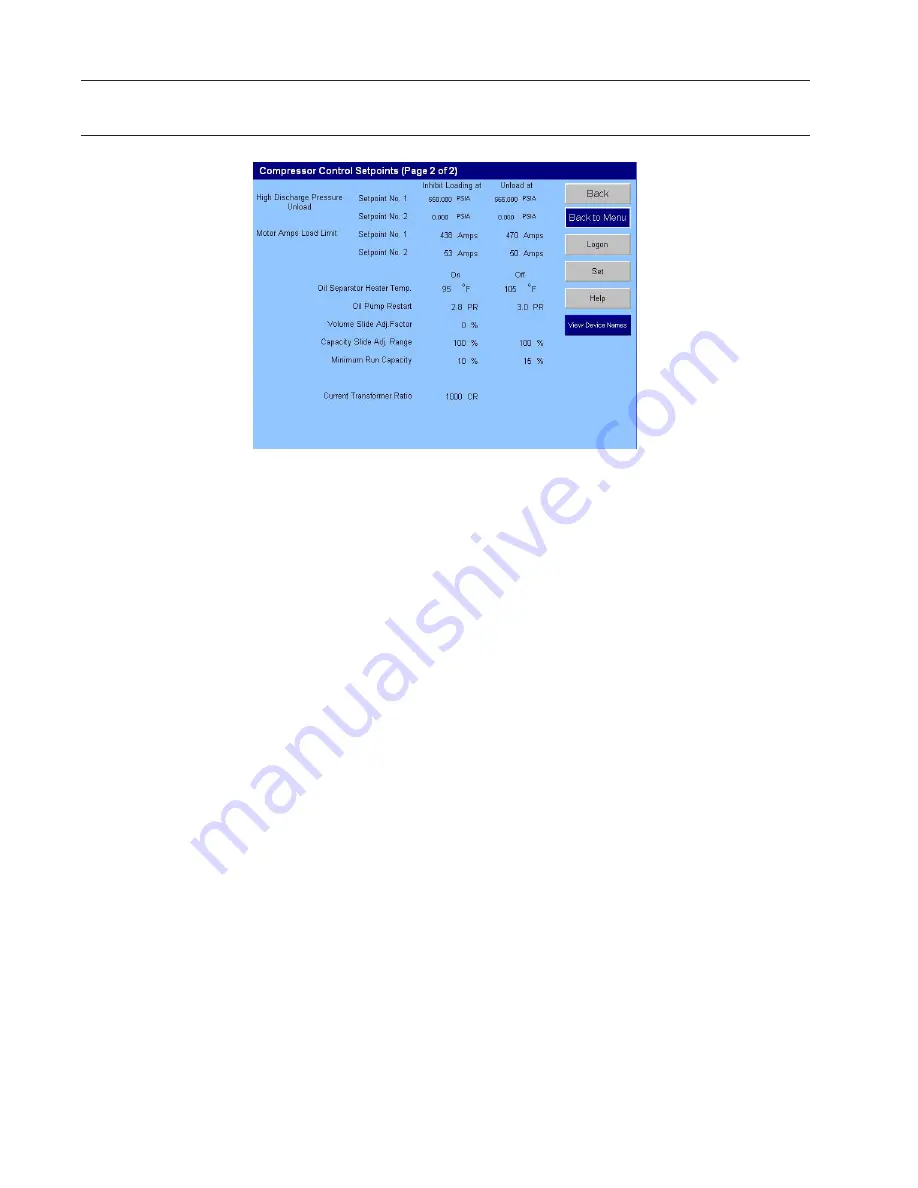
32
Additional Compressor Controls
·
High Discharge Pressure Unloading Setpoints
– Active in Suction Pressure or Process Tempera-
ture Capacity Control mode. These setpoints
limit the compressor from loading at high
discharge pressure conditions. They override
the Suction Pressure or Process Temperature
Capacity Control setpoints. The capacity of the
compressor will decrease when the discharge
pressure is at or above the ON set point. When
the OFF setpoint is reached, the compressor will
stop from unloading any further.
·
Motor Amp. Load Limit Setpoints
– This control
limit is the motor full load current draw and the
maximum current draw. This control limit will
only prevent the compressor from loading and
does not shut down the compressor if the maxi-
mum current draw setpoint is exceeded. The
actual values entered may depend on particular
circumstances. The function of the setpoint is
as follows:
If the motor is operating at the full load amper-
age (FLA) setting, the compressor is prevented
from loading. If the motor amps exceed the
MAX setpoint, the compressor is forced to un-
load until the current is at 1.0625 times above
the FLA setting. If the motor being used has a
service factor below 1.0625, use a value for the
FLA that is 10% lower than the MAX value.
·
Oil Separator Heater Temperature
– This con-
trol limit determines when the oil separator
heater is energized. A decrease in oil separator
temperature below the ONsetpoint energizes
the oil separator heater. On an increase in oil
separator temperature above the OFF setpoint,
the oil heater is de-energized.
·
High Discharge Pressure Unloading Setpoints
–
Active in Suction Pressure or Process Tempera-
ture Capacity Control mode. These setpoints
limit the compressor from loading at high
discharge pressure conditions. They override
the Suction Pressure or Process Temperature
Capacity Control setpoints. The capacity of the
compressor will decrease when the discharge
pressure is at or above the ON set point. When
the OFF setpoint is reached, the compressor will
stop from unloading any further.
·
Motor Amp. Load Limit Setpoints
– This control
limit is the motor full load current draw and the
maximum current draw. This control limit will
only prevent the compressor from loading and
does not shut down the compressor if the maxi-
mum current draw setpoint is exceeded. The
actual values entered may depend on particular
circumstances. The function of the setpoint is as
follows: If the motor is operating at the full load
amperage (FLA) setting, the compressor is pre-
vented from loading. If the motor amps exceed
the MAX setpoint, the compressor is forced to
unload until the current is at 1.0625 times above
the FLA setting. If the motor being used has a
service factor below 1.0625, use a value for the
FLA that is 10% lower than the MAX value.
Summary of Contents for VSG & VSSG
Page 1: ...1 VSG VSSG Single Screw Compressor Software Manual Compact Logix PLC ...
Page 2: ...2 ...
Page 4: ...4 ...
Page 14: ...14 ...
Page 21: ...21 Discharge Pressure Control There are three options for the Compressor Control Setpoints ...
Page 22: ...22 Suction Pressure Control ...
Page 23: ...23 Process Temperature Control ...
Page 39: ...39 Instrument Calibration ...
Page 46: ...46 ...
Page 68: ...68 ...
Page 69: ......
Page 70: ......
Page 71: ......
Page 72: ......
Page 73: ......
Page 74: ......
Page 75: ......
Page 76: ......
Page 77: ......
Page 79: ......
Page 81: ......
Page 82: ......
Page 83: ......
Page 84: ......
Page 85: ...69 ...