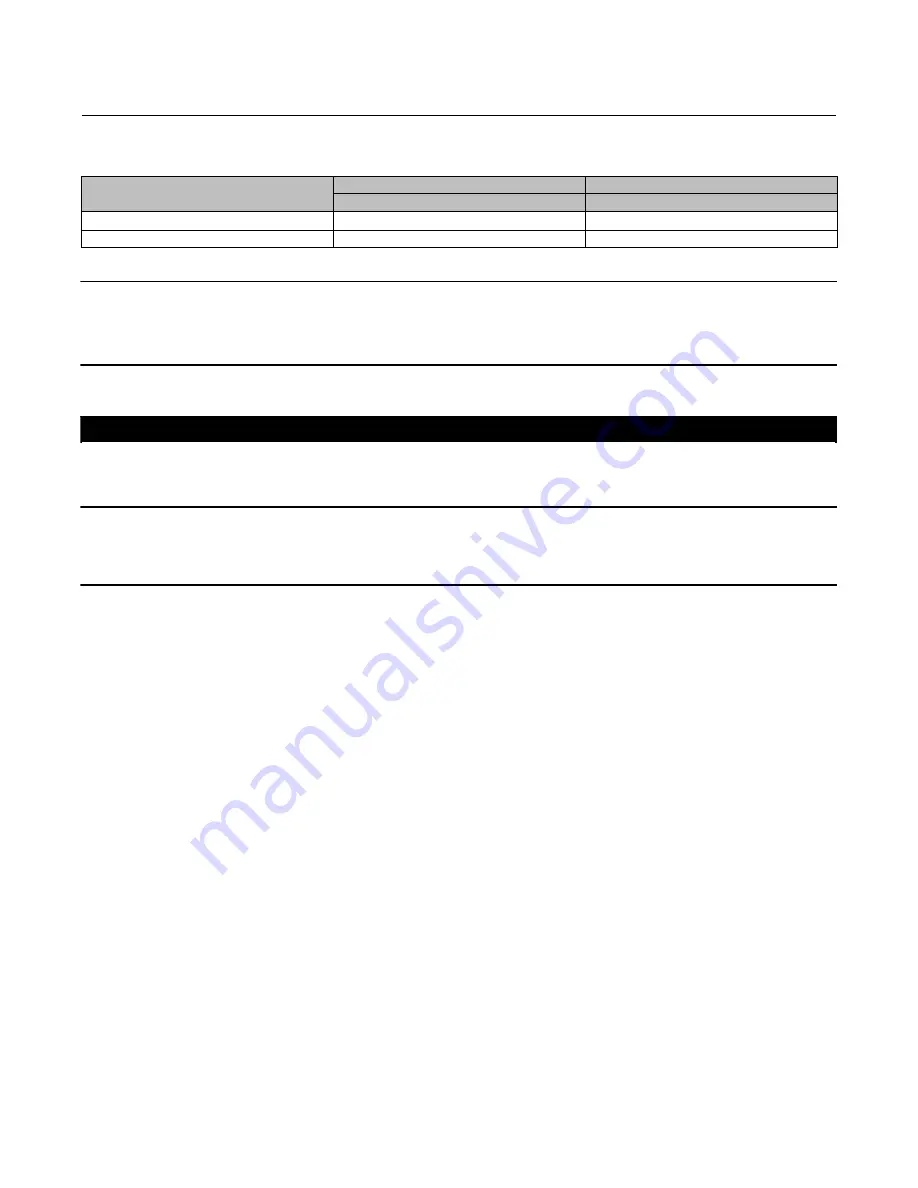
Instruction Manual
D102602X012
657NS Actuator
November 2012
15
Table 6. Size 80 Casing Cap Screw Torque Values
DIAPHRAGM MATERIAL
INITIAL TORQUE
FINAL TORQUE
N
S
m (lbf
S
ft)
N
S
m (lbf
S
ft)
EPDM / Meta-Aramid
41 (30)
82
±
13 (60
±
10)
Nitrile, Silicone, FKM/Meta-Aramid
34 (25)
68 (50)
Note
When you replace actuator diaphragms in the field, take care to ensure the diaphragm casing cap screws are tightened to the
proper load to prevent leakage, but not crush the material. Perform the following tightening sequence with a manual torque
wrench for size 80 actuators.
CAUTION
Overtightening the diaphragm casing cap screws and nuts can damage the diaphragm. Do not exceed the following
maximum torque values for the appropriate diaphragm material: EPDM/Meta-Aramid: 95 N
S
m (70 lbf
S
ft);
Nitrile, Silicone, FKM (fluorocarbon) / Meta-Aramid: 68 N
S
m (50 lbf
S
ft).
Note
Do not use lubricant on these cap screws and nuts. Fasteners must be clean and dry.
6. Fasten the two diaphragm casings together with the cap screws (key 22) and tighten the hex nuts (key 23) in the
following manner. The first four hex nuts tightened should be diametrically opposed and 90 degrees apart. Tighten
these four hex nuts to the initial torque value found in table 6 for the diaphragm material being used.
7. Tighten the remaining hex nuts in a clockwise, crisscross pattern to the initial torque value found in table 6 for the
diaphragm material being used.
8. Repeat this procedure by tightening four hex nuts, diametrically opposed and 90 degrees apart, to the final torque
value that is specified in table 6 for the diaphragm material being used.
9. Tighten the remaining hex nuts in a clockwise, crisscross pattern to the final torque value that is specified in table 6
for the diaphragm material being used.
10. After the last hex nut is tightened, complete another tightening sequence. Tighten in a circular pattern around the
bolt circle to the final torque value that is specified in table 6 for the diaphragm material being used.
11. Once completed, no more tightening is recommended.
12. Thread the spring adjusting screw locknut (key 91) onto the actuator stem (key 10). Place the spring (key 6) on the
casing flange (key 51).
13. Assemble the spring seat and spring seat guide (keys 11 and 36). Place them on the actuator spring (key 6).
14. Lubricate the spring seat race and bearings (keys 39 and 40) with lithium grease (key 53). Place them on the spring
seat.
15. Attach the stem connector (key 26) to the actuator stem so that the connector engages the antirotation guide on
the actuator yoke. Thread the adjusting screw (key 12) onto the actuator stem until the actuator stem (key 10)
extends above the adjusting screw the distance recorded in step 4 of the disassembly procedures for size 80
actuators. Securely tighten the spring adjusting screw locknut (key 91) against the spring adjusting screw (key 12).
16. Connect piping or tubing to the pressure connection in the upper diaphragm casing (key 1). Pressure the actuator,
and if necessary, readjust the spring compression with the adjusting screw (key 12) until the actuator fully strokes
over the bench set pressure range stamped on the actuator nameplate. Remove the stem connector.