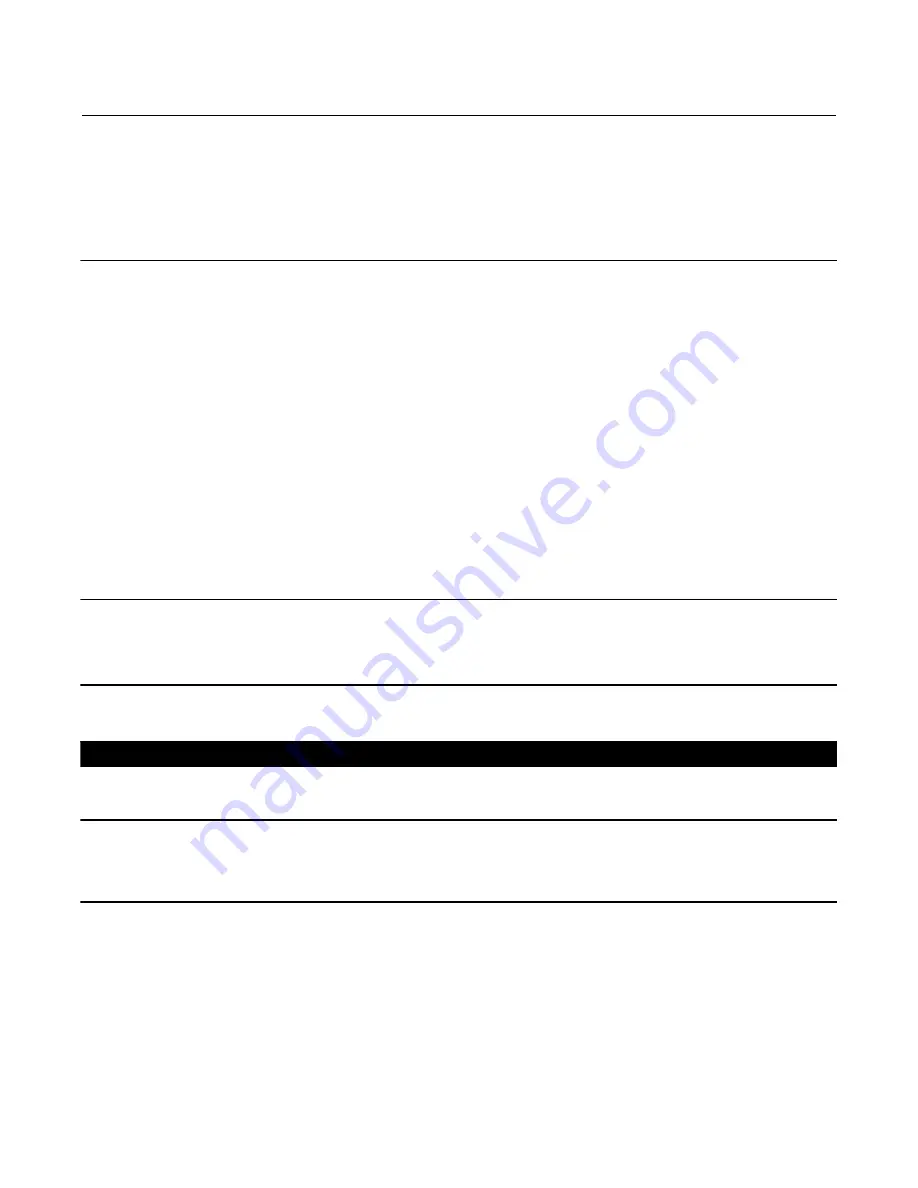
Instruction Manual
D102602X012
657NS Actuator
November 2012
11
D
Use lock-out procedures to be sure that the above measures stay in effect while you work on the equipment.
D
The valve packing box may contain process fluids that are pressurized,
even when the valve has been removed from the
pipeline.
Process fluids may spray out under pressure when removing the packing hardware or packing rings, or when
loosening the packing box pipe plug.
D
Check with your process or safety engineer for any additional measures that must be taken to protect against process
media.
Replacement of the Elastomeric Parts
Size 40, 45, and 70 Actuators
Perform the following if it is desired to replace only the elastomeric parts of the 657NS actuator, and no other
maintenance is necessary. The diaphragm is the only elastomeric part in the size 40, 45, and 70 actuators. Key number
references are shown in figure 2 for size 40 and 45 actuators and in figure 3 for size 70 actuators.
1. Isolate the control valve from the line pressure, release pressure from both sides of the valve body, and drain the
process media from both sides of the valve. Reduce the actuator loading pressure to atmospheric pressure, and
remove the tubing or piping from the top of the upper diaphragm casing (key 1).
2. Remove the diaphragm casing cap screws and nuts (keys 22 and 23), and lift off the upper diaphragm casing.
3. Take out the diaphragm (key 2), and install a new one.
Note
When you replace actuator diaphragms in the field, take care to ensure the diaphragm casing cap screws are tightened to the
proper load to prevent leakage, but not crush the material. Perform the following tightening sequence with a manual torque
wrench for size 40, 45, and 70 actuators.
CAUTION
Overtightening the diaphragm casing cap screws and nuts (keys 22 and 23) can damage the diaphragm. Do not exceed a
torque of 27 N
S
m (20 lbf
S
ft) when performing this tightening procedure.
Note
Do not use lubricant on these cap screws and nuts. Fasteners must be clean and dry.
4. Place the upper diaphragm casing (key 1) into position, and replace the diaphragm casing cap screws and nuts (keys
22 and 23). Tighten the hex nuts (key 23) in the following manner. The first four hex nuts tightened should be
diametrically opposed and 90 degrees apart. Tighten these four hex nuts to 13 N
S
m (10 lbf
S
ft).
5. Tighten the remaining hex nuts in a clockwise, crisscross pattern to 13 N
S
m (10 lbf
S
ft).
6. Repeat this procedure by tightening four hex nuts, diametrically opposed and 90 degrees apart, to a torque of 27
N
S
m (20 lbf
S
ft).
7. Tighten the remaining hex nuts in a clockwise, crisscross pattern to 27 N
S
m (20 lbf
S
ft).