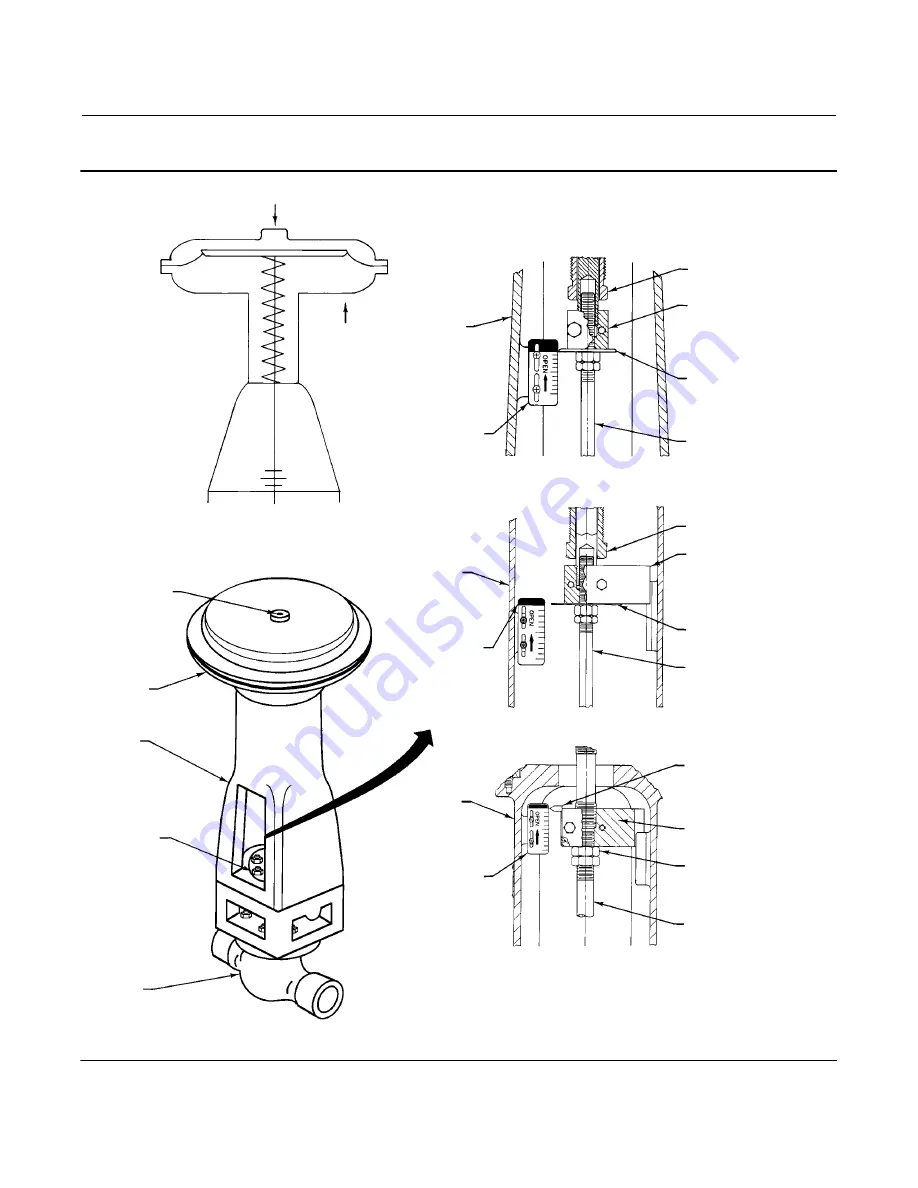
Instruction Manual
D102602X012
657NS Actuator
November 2012
7
Figure 1. Schematic and Stem Connection Details for Fisher 657NS
AF3833-A
45A9190-D
55A9192-C
55A1030-C
A5959/MM1
C0761
AIR
PUSHES
DOWN
SPRING
LIFTS
SCHEMATIC
SIZES 40 AND 45
YOKE
TRAVEL
INDICATOR
SPRING
ADJUSTOR
STEM
CONNECTOR
TRAVEL
INDICATOR
DISK
VALVE
STEM
YOKE
YOKE
YOKE
TRAVEL
INDICATOR
TRAVEL
INDICATOR
SPRING
ADJUSTOR
TRAVEL
INDICATOR
DISK
STEM
CONNECTOR
STEM
CONNECTOR
VALVE
STEM
VALVE
STEM
SIZE 70
SIZE 80
STEM CONNECTION
DETAILS
STEM
LOCKNUTS
TRAVEL
INDICATOR
POINTER
NPT INTERNAL
CONNECTION
DIAPHRAGM
CASING
ACTUATOR
VALVE
STUDS
AND NUTS
FISHER
DBQ-NS
VALVE