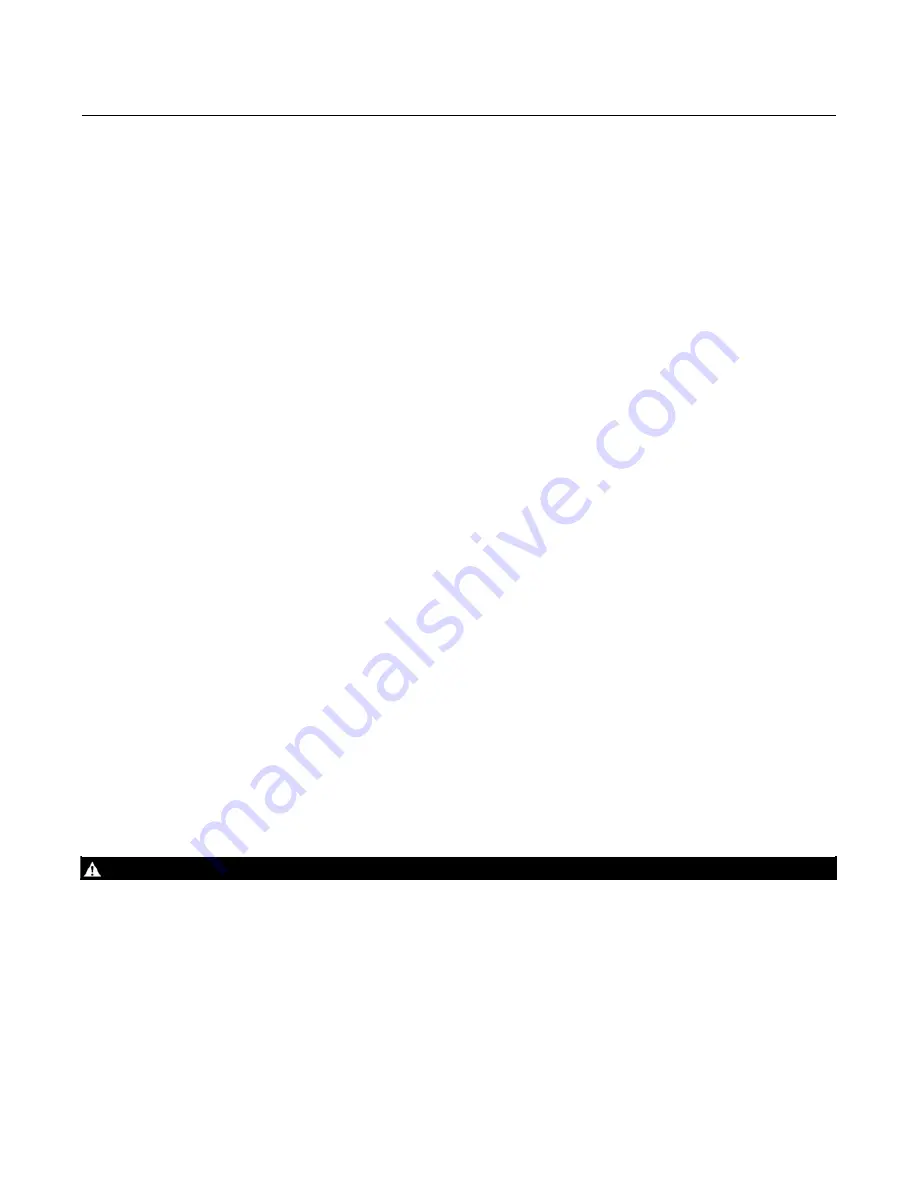
Instruction Manual
D102602X012
657NS Actuator
November 2012
10
is shown graphically in figure 1. In the event of failure of the loading pressure to the diaphragm of the actuator, the
actuator stem moves to the extreme upward position. Thus, by the proper selection of the valve plug action, either
push-down-to-close or push-down-to-open, the control valve will either close or open on failure of the loading
pressure.
The nameplate attached to the yoke of the actuator provides information about the specific construction and
operating range. The spring and diaphragm have been selected to meet the requirements of the application, and in
service, the actuator should create full travel of the valve plug when the diaphragm pressure (operate) range indicated
on the nameplate is applied. This diaphragm pressure range is generally 0.2 to 1.0 bar or 0.4 to 2.0 bar (3 to 15 psi or 6
to 30 psi).
Pressure in the valve body creates a force on the valve plug that has a direct effect on the actual operating diaphragm
pressure range. In some instances, the valve may not stroke completely over the indicated range because the pressure
conditions in the body are different from those for which the control valve has been set at the factory. A simple spring
adjustment, however, may be all that is required to obtain correct travel for the diaphragm pressure range utilized.
Note that the actuator spring has a fixed pressure span and that adjustment of the spring compression merely shifts
this span up or down to make valve travel coincide with the diaphragm pressure range.
The nameplate specifies a bench set pressure range in addition to a diaphragm pressure (operate) range. The bench
set range is that pressure range required to stroke the valve fully without any pressure in the body, as would be the
case if the valve were set on the work bench. However, in service, with the specified pressure drop applied across the
valve, it should stroke over the diaphragm pressure (operate) range indicated on the nameplate.
When the control valve and actuator are installed, the actuator should be checked for correct travel, freedom from
excessive friction, and correct action (air-to-open or air-to-close) to match the controlling instrument. For successful
operation, the actuator stem and the valve plug stem must move freely in response to the loading pressure change on
the diaphragm.
Maintenance
Normally, only the elastomeric parts and the spring of the 657NS actuator require inspection or replacement. The
maintenance instructions are divided into three subsections: Replacement of the Elastomeric Parts, Disassembly, and
Assembly. Perform only those steps applicable to the actuator size and required maintenance.
All maintenance operations can be performed with the valve in the line.
It is recommended that the diaphragm and all of the other elastomeric parts of the 657NS actuator be inspected every
two years. The absolute maximum replacement period for any of the elastomeric parts is four years.
WARNING
Avoid personal injury or property damage from sudden release of process pressure or bursting of parts. Before performing
any maintenance operations:
D
Do not remove the actuator from the valve while the valve is still pressurized.
D
Always wear protective gloves, clothing, and eyewear when performing any maintenance operations to avoid personal
injury.
D
Disconnect any operating lines providing air pressure, electric power, or a control signal to the actuator. Be sure the
actuator cannot suddenly open or close the valve.
D
Use bypass valves or completely shut off the process to isolate the valve from process pressure. Relieve process pressure
from both sides of the valve. Drain the process media from both sides of the valve.
D
Vent the power actuator loading pressure and relieve any actuator spring precompression.