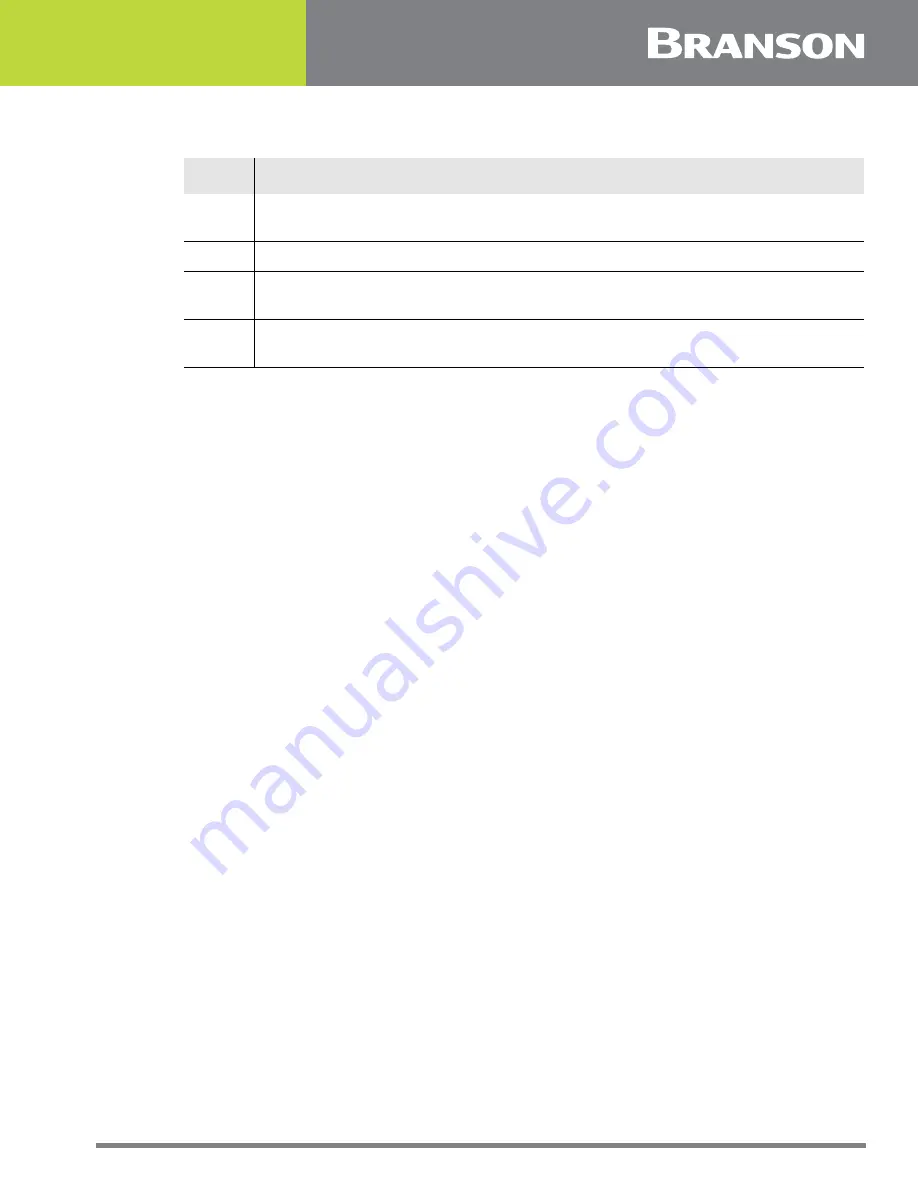
100-412-183 REV. 13
73
If converter cooling is required, use the following steps:
A 0.06 in (1.5 mm) orifice at 50 psi (345 kPa) will result in a reading of 80 ft
3
(2.26 m
3
)
per hour. This should be sufficient to cool most operations requiring a cooling air stream.
In continuous welding operations, or applications with longer duty cycles, it may be
necessary to cool the horn as well as the converter. Horns may require cooling because of
the heat transfer from contacting the work piece.
Table 5.21 Converter Cooling Procedure
Step
Action
1
Start with a 50 psi (345 kPa) air source or higher from a 0.06 in (1.5 mm) I.D.
orifice
2
Perform a run of welding operations.
3
Immediately after completing the welding run, check the converter
temperature.
4
If the converter is still too hot, increase the diameter of the orifice in small
increments until the temperature falls within the ranges in the chart.
Summary of Contents for DCX S
Page 4: ...iv 100 412 183 REV 13 ...
Page 22: ...12 100 412 183 REV 13 ...
Page 36: ...26 100 412 183 REV 13 ...
Page 47: ...100 412 183 REV 13 37 4 3 Declaration of Conformity Figure 4 1 Declaration of Conformity ...
Page 50: ...40 100 412 183 REV 13 ...
Page 54: ...44 100 412 183 REV 13 Figure 5 1 DCX S Power Supply Benchtop Dimensional Drawing ...
Page 86: ...76 100 412 183 REV 13 ...
Page 87: ...100 412 183 REV 13 77 Chapter 6 Converters and Boosters 6 1 Converters and Boosters 78 ...
Page 120: ...110 100 412 183 REV 13 ...
Page 137: ...100 412 183 REV 13 127 8 5 Circuit Diagram Figure 8 2 Interconnect Diagram Power Supply ...
Page 144: ...134 100 412 183 REV 13 ...
Page 145: ...100 412 183 REV 13 135 Appendix A Timing Diagrams A 1 Timing Diagrams 136 ...
Page 147: ...100 412 183 REV 13 137 Appendix B Signal Diagrams B 1 Signal Diagrams 138 ...
Page 154: ...144 100 412 183 REV 13 ...