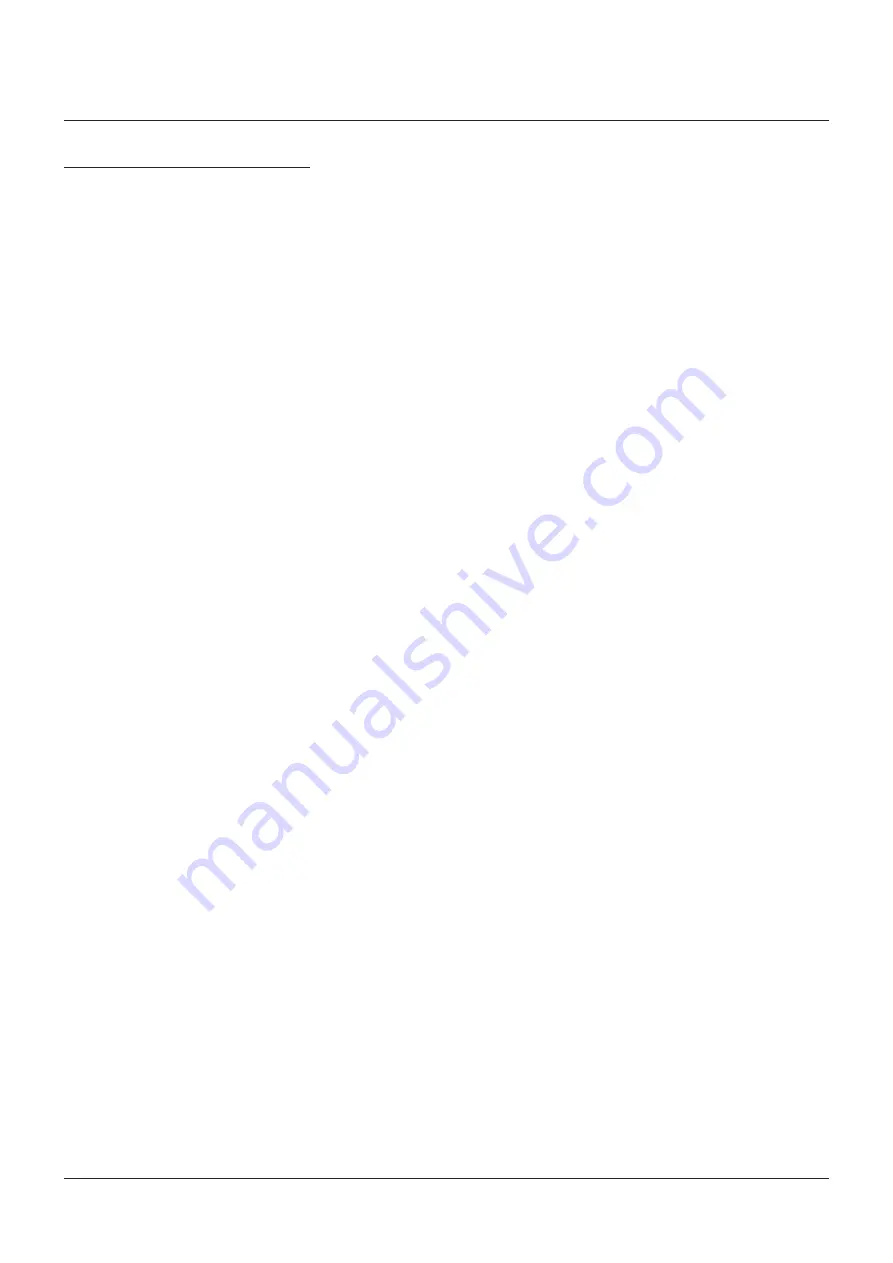
6
Crosby
STylE JOS-E, JBS-E, JlT*-JBS-E, JlT*-JOS-E ValVES
InstallatIon and MaIntenance InstructIons
5 seTTing, TesTing and adJusTMenTs
5.1 new valves
Every new Crosby J series pressure relief valve
is tested fully and sealed prior to shipment� The
external adjustment points of each valve are
sealed to ensure that no changes have been
made to the valve after shipment and that the
valve has not been disassembled or tampered
with� The seals and nameplates are your
assurance that the valve has been built and
tested to the applicable Codes and Standards
and are the physical evidence of our product
warranty�
all new Crosby J series valves are tested
fully prior to shipment on the appropriate
testing medium, so there is no need to pre-
test the valve prior to installation� If pre-
testing is required, in order to maintain the
product warranty, a Crosby valves authorized
service organization should be contacted to
perform the testing� Contact your local sales
representative or visit our website to locate
the authorized service organization closest
to your location� By choosing an authorized
service organization to perform testing you can
be assured that the correct testing procedure
is followed which will save time and cost by
avoiding possible valve damage caused by
improper testing methods�
In any event, if pre-testing is to be performed,
several important cautions should be observed�
First it is vital that the appropriate test fluid is
used to test any valve� See Section 5�5� This will
ensure accuracy of the test results as well as
avoid possible damage to the valve�
all Crosby J series valves are tested for seat
tightness after the final set point test and prior
to shipment from the factory� If further seat
tightness testing is required before installation,
it is recommended that the test be performed
prior to any set point verification testing�
Repeated pressure testing of a metal seated
valve can cause damage to the sealing surfaces
leading to seat leakage
Testing on a low volume test stand requires
specific testing techniques in order to ensure
accurate test results and to avoid damage to the
sealing surfaces of the valve� In many cases this
requires temporary adjustment of the nozzle ring
during the test as described in Section 5�8 and
specifically in Section 5�8�1� For valves with set
points in excess of 500 psig, it is recommended
that when testing on a low volume test bench,
the lift be restricted temporarily by use of a gag
or other suitable device�
However, it is good practice to inspect the valve
prior to installation�
This inspection determines any damage which
may have occurred due to rough handling in
transit or storage and initiates appropriate
service records�
5.3 Valves removed from service
Valves being removed from service should
be tested on a shop test bench before being
disassembled to determine the set pressure
and seat tightness� This is an important
phase of the maintenance routine and the test
results should be recorded for review and
determination of necessary corrective action�
The 'as received from service' condition of a
pressure relief valve is a most useful tool in
establishing the proper time interval between
inspections�
5.4 The test bench
The quality and condition of the shop test bench
is paramount to obtaining proper test results�
The test bench must be free of leaks and the
test fluid must be clean� Solids or other foreign
material in the test medium will damage the
seating surfaces of the pressure relief valve
being tested�
The test pressure gauge must be calibrated
and have a range proper to the pressure level
of the valve setting� Set pressure should fall
within the middle third of the dial range of the
test gauge� The test bench provides an accurate
and convenient facility for determining valve
set pressure and seat tightness� It does not
duplicate all of the field conditions to which a
pressure relief valve will be exposed while in
service� It is not practical to attempt to measure
relieving capacity or blowdown using a test
bench�
5.5 Test fluids - set pressure test
The test fluid should be air or nitrogen for
valves used on gas and vapor service and water
for valves used on liquid service� Valves for
steam service should be tested on steam�
It may be necessary to make a correction to
the adjusted set pressure to compensate for
the difference in temperature of the test fluids
(see appropriate instruction)�
5.2 reconditioned valves
Valves which have not been in service for
extended periods due to plant shutdown or
long term storage, or valves which have been
repaired or reconditioned, also should be tested
before being put into operation�
CauTion
Improper testing may cause valve damage and
seat leakage.