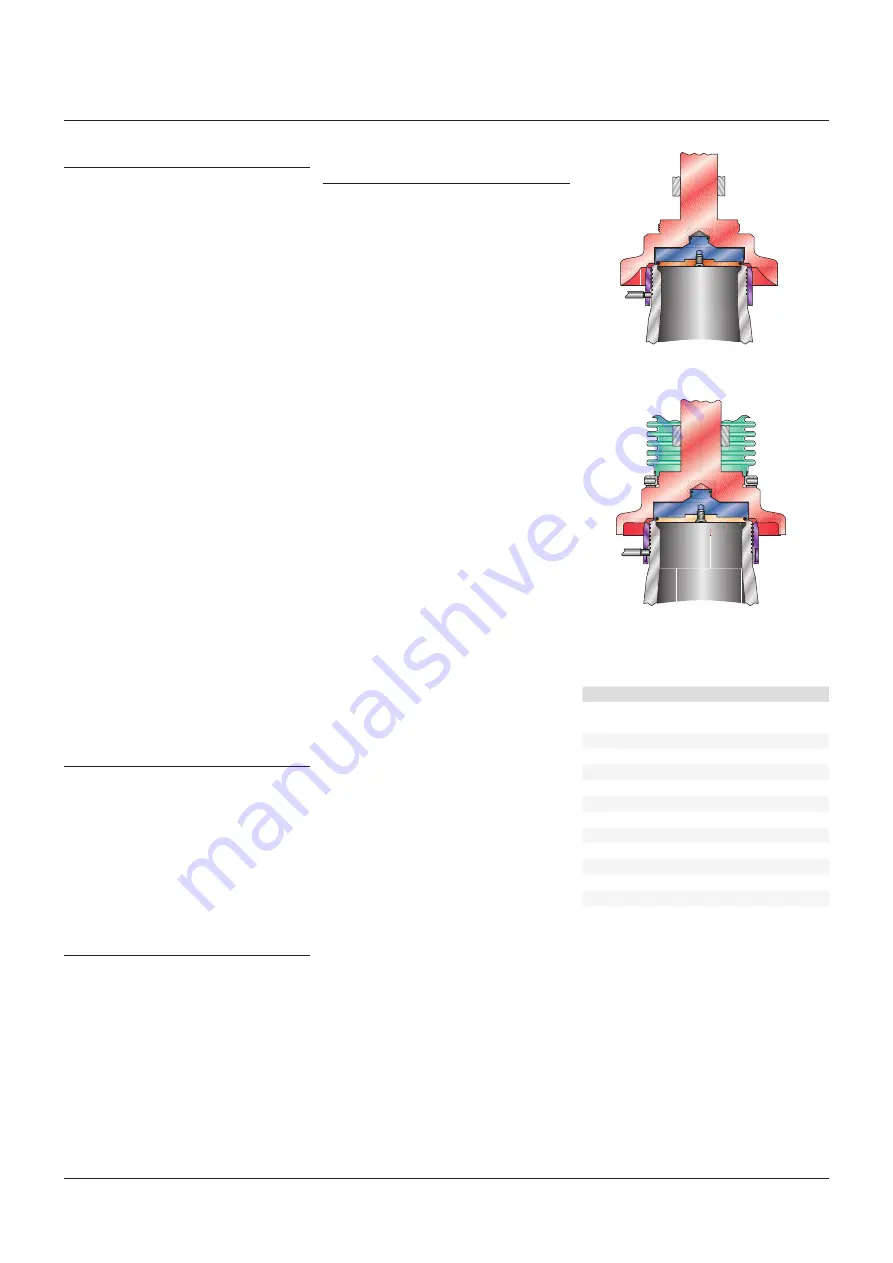
21
D, E
*2-013
** 2-014
F
2-113
g
2-116
H
2-120
J
2-125
K
2-130
l
2-226
M
2-228
N
2-230
P
2-337
Q
2-346
R
2-352
T, T2
2-438
Crosby
STylE JOS-E, JBS-E, JlT*-JBS-E, JlT*-JOS-E ValVES
InstallatIon and MaIntenance InstructIons
7 sTyle VariaTions
The Crosby Style JOS-E pressure relief
valve was designed with flexibility and
interchangeability in mind� Retrofitting
from conventional to balanced bellows high
performance liquid trim or soft seat design
is accomplished with a minimum number
of new parts� These style retrofits can be
accomplished at lowest possible cost�
• Balanced bellows
a Crosby JOS-E conventional non-bellows
pressure relief valve may be converted to a
Style JBS-E balanced bellows valve simply
by adding the bellows assembly and tailpiece
gasket�
• JLT liquid trim
Crosby Style JOS-E/JBS-E pressure relief
valves in D to N orifice sizes may be converted
to high performance JlT liquid service design
simply by replacing the standard disc holder
with a JlT disc holder, or vice versa� For P
to T orifice sizes, a new nozzle ring is also
required�
• O-ring soft seat design
Crosby Style JOS-E and JBS-E pressure relief
valves in all orifice sizes may be converted
from the standard metal-to-metal seats to an
exceptionally tight soft seat design� This style
conversion can be accomplished by replacing
the standard disc insert and nozzle with parts
adapted to accommodate the soft seat design�
The soft seat design uses standard size
O-rings and is capable of handling pressures
to 1480 psig� Standard O-ring materials
include NBR, EPR, FKM, Kalrez
®
, Silicone and
PTFE (see Figure 15 and Table 12)�
Jos-e/Jbs-e o-ring
Soft seat
JlT-e o-ring
Soft seat
FIguRE 15
Table 12 - soft seat o-ring sizes
orifice
o-ring size
8 serViCe reCords
Service records should be completed before
a valve is returned to service� These records
are important and will provide guidance on
establishing time intervals between repairs as
well as providing the historical record of repairs
and service conditions� Well kept records will
be useful in predicting when to retire a valve
and which spare parts should be maintained in
inventory to ensure uninterrupted plant operation�
9 sPare ParTs
When ordering spare parts, the valve shop
number, assembly number or serial number
should be given together with set pressure, part
name and item number, valve size and style�
On the valve nameplate, the valve assembly
number is shown as shop number�
Spare parts may be ordered from any Emerson
regional sales office or representative�
10 Trouble shooTing Pressure relief
ValVes
Troubles encountered with pressure relief
valves can affect the life and performance of
the valve vitally and must be corrected at the
first possible opportunity�
Failure of a pressure relief valve to function
properly could result in the rupture of a line or
vessel jeopardizing the safety of personnel and
causing damage to property and equipment�
Some of the most common troubles and
the recommended correction measures are
discussed in the following paragraphs�
10.1 seat leakage
Of all the problems encountered with pressure
relief valves, seat leakage is the most common
and the most detrimental� a leaking valve
allows fluids to circulate into the secondary
pressure zone of the valve where it can cause
corrosion of the guide and valve spring�
When a leaking valve problem is not addressed
immediately, the leakage itself will further
contribute to seat damage through erosion
(wire-drawing)�
10.1.1 Seats damaged by foreign matter
Seating surfaces may be damaged
when hard foreign particles such as mill
scale, welding spatter, coke and dirt are
trapped between the seats� While this
type of damage usually occurs while the
valve is in service, it may also happen in
the maintenance shop� Every precaution
should be taken to clean the process
system before installing a pressure relief
valve and to test the valve using only
clean fluids�
generally, damaged seating surfaces
are reconditioned by lapping� Most often
small pits and scratches may be removed
by lapping alone� More extensive damage
will also require remachining prior to
lapping�
In some instances, valve construction can
be changed to reduce the effects of seat
leakage� The use of an O-ring soft seat
when applicable will minimize leakage
and thus eliminate the associated
corrosion and erosion problems� If it is
not possible to use a soft seated valve, or
if the corrosive media is present in the
exhaust system, conversion to a Style
JBS bellows seated valve will isolate and
protect the guides and valve spring from
any corrosive fluids�
* all elastomers
** PTFE only