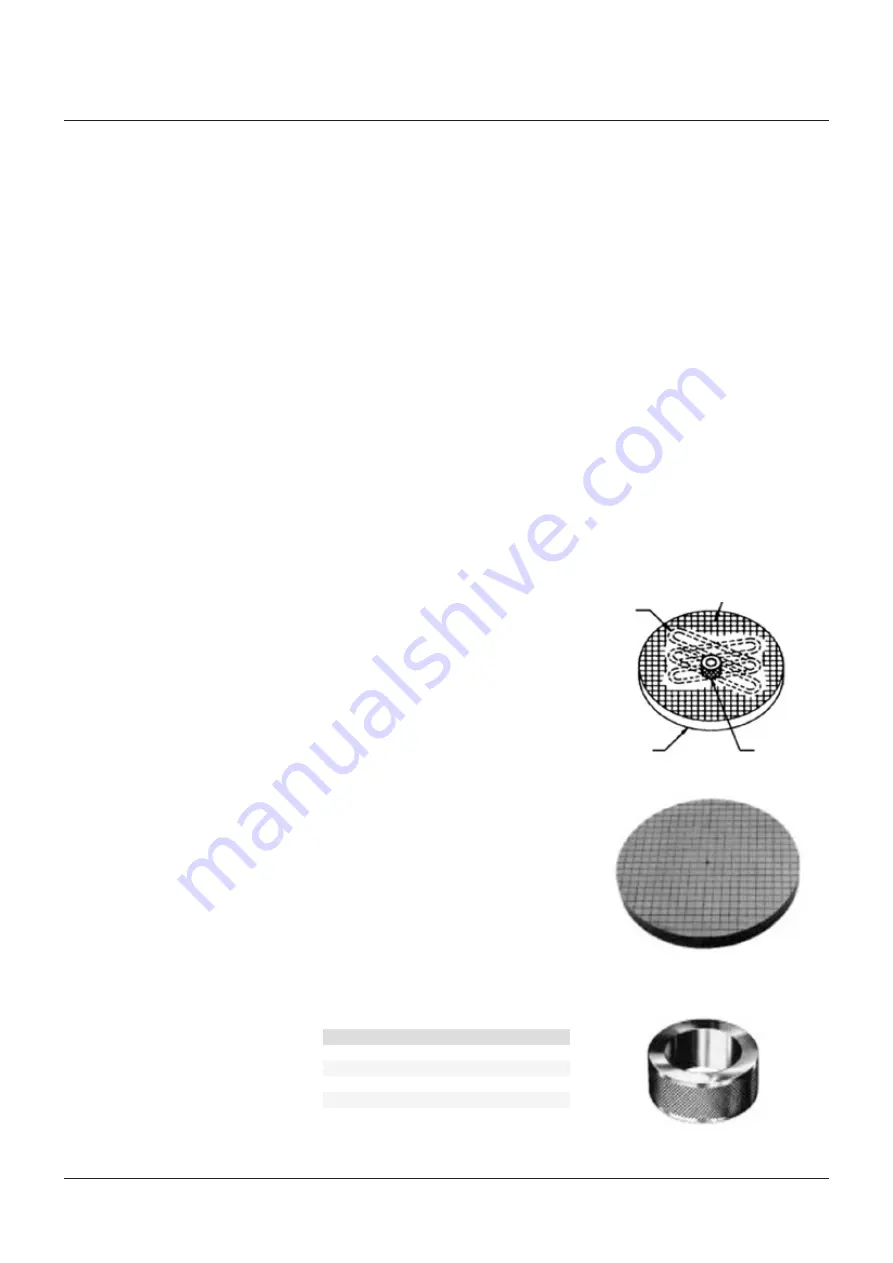
12
Crosby
STylE JOS-E, JBS-E, JlT*-JBS-E, JlT*-JOS-E ValVES
InstallatIon and MaIntenance InstructIons
6.4 inspection
Check all valve parts for wear and corrosion�
The valve seats on both the nozzle and disc
insert must be examined to determine if they
have been damaged� Most often, lapping the
valve seats is all that is necessary to restore
them to their original condition�
If the inspection shows that the valve seats are
damaged badly, remachining will be necessary
or it may be advisable to replace these parts�
When the time element is a factor, it may be
advantageous to replace damaged parts from
spare parts stock, thereby permitting the
replaced part to be checked and reworked at
leisure� (See Figure 10 and Table 8 for critical
dimensions)� The valve spring (18) should be
inspected for evidence of cracking, pitting or
deformation� The bellows (6B) in a Style JBS-E
and JlT-JBS-E valve should be inspected for
evidence of cracking, pitting or deformation that
might develop into a leak�The bearing surfaces
on the guide and disc holder should be checked
for residual product build up and any evidence
of scoring� Inspection of valve components is
important to ensure proper valve performance�
Damaged valve parts must be repaired or
replaced�
Spindle assemblies should be checked for
excessive runout� For D to K orifice the total
runout between the spindle point to top of the
spindle rod should be less than 0�015 inch�
For l orifice and larger it should be less than
0�030 inch�
Check and inspect all gaskets for evidence of
damage (creases, gouges, cuts) or corrosion�
Metal gaskets may be re-used if found to be
undamaged� all organic fiber or soft gaskets
should be replaced�
grit compound no.
description
320
Medium coarse
400
Medium
600
Fine
900
Polish
FIguRE 9
lapping block resurfacing plate
lapping block
Top lapping surface
lapping block to
be squared up
Motion shown by
dotted lines
Bottom rough
surface do not use
6.5 reconditioning of valve seats
The tightness of a valve and its proper
operation depend directly on the condition of
the seats� Many pressure relief valve problems
are due to eroded or damaged seats�
The standard Crosby Style JOS-E/JBS-E/JlT-E
valve is constructed with a flat metal-to-metal
seat� It is important that seating surfaces be
refurbished properly by lapping with a flat
cast iron lap coated with the correct lapping
compound�
6.5.1 Lapping procedures
unless the seats have been damaged
badly by dirt or scale, lapping the seating
surfaces should restore them to their
original condition� Never lap the disc
insert against the nozzle� lap each part
separately against a cast-iron lapping
block of the proper size� These blocks hold
the lapping compound in their surface
pores and must be recharged frequently�
lap the block against the seat� Never
rotate the block continuously, but use an
oscillating motion� Extreme care should
be taken throughout to make certain
as the lapping nears completion, only the
compound left in the pores of the block
should be present� This should give a very
smooth finish� If scratches appear, the
cause is probably dirty lapping compound�
These scratches should be removed by
using compound free from foreign material�
Disc inserts should be lapped in the same
way as nozzles� The disc insert must be
removed from the holder before lapping�
Before the disc insert is placed back in
the holder all foreign material should be
removed from both parts� The insert must
be free when in the holder� If the disc insert
is damaged too badly to be reconditioned
by lapping, it should be replaced�
Remachining the insert will change critical
dimensions, affect the action of the valve
and is not recommended�
• Lapping blocks
lapping blocks are made of a special
grade of annealed cast iron� There is a
block for each orifice size� Each block
has two perfectly flat working sides and
it is essential that they retain this high
degree of flatness to produce a truly flat
seating surface on either the disc insert
or the nozzle� Before a lapping block is
used, it should be checked for flatness and
reconditioned after use on a lapping plate�
The block should be lapped in a figure
eight motion, applying uniform pressure
while rotating the lapping block against
the plate as shown in Figure 9�
• Lapping compounds
Experience has proven that medium
coarse, medium fine and polish lapping
compounds will condition any damaged
pressure relief valve seat properly except
where the damage requires remachining�
The following lapping compounds, or their
commercial equivalents are suggested:
that the seats are kept perfectly flat�
If considerable lapping is required, spread
a thin coat of medium coarse lapping
compound on the block� after lapping with
the medium coarse compound, lap again
with a medium grade compound� unless
much lapping is called for, the first step
can be omitted� Next, lap again using a
fine grade compound� When all nicks
and marks have disappeared, remove all
the compound from the block and seat�
apply polish compound to another block
and lap the seat�