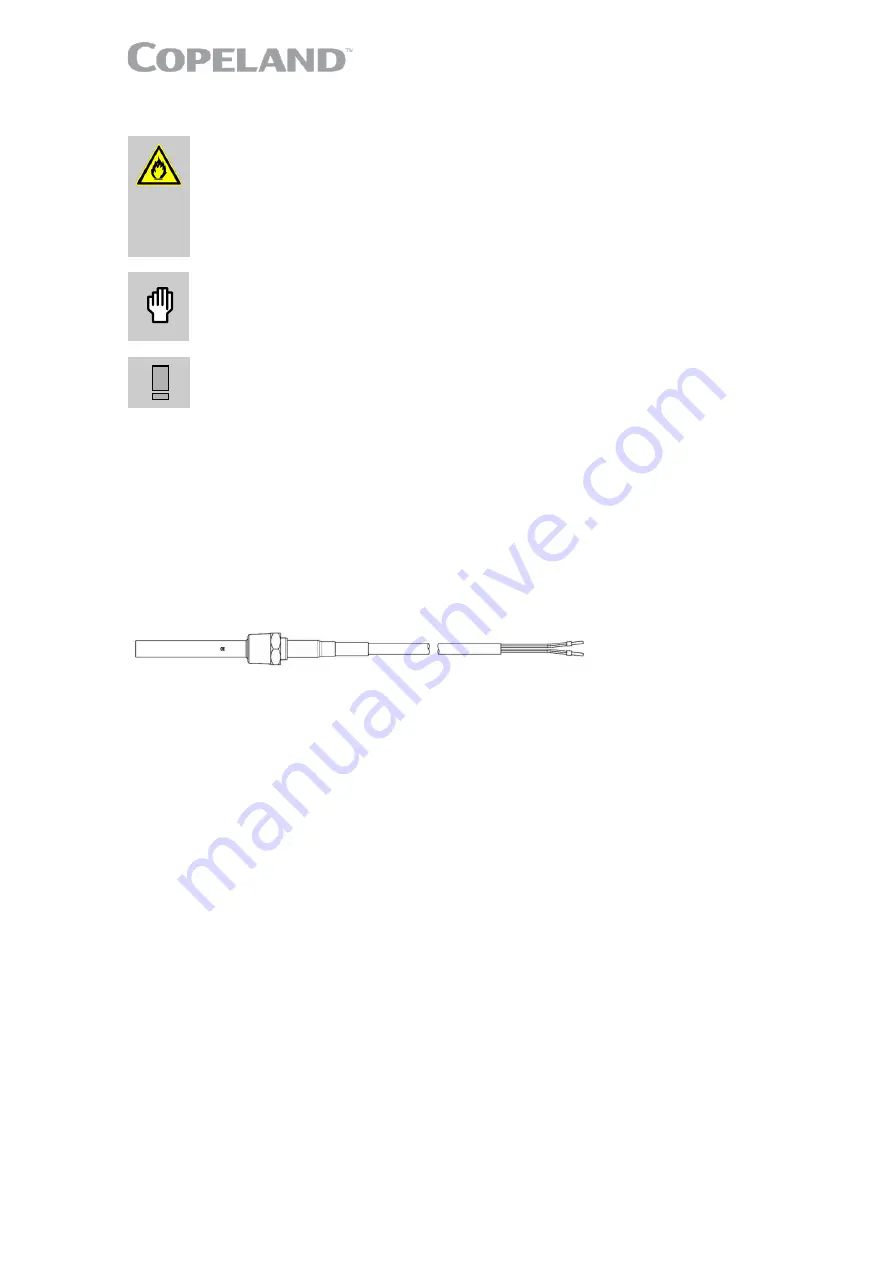
30
AGL_Stream_ST_A2L_A1_4M_6M_EN_Rev00
4.6 Crankcase heaters
WARNING
Ignition source in a potentially flammable atmosphere due to hot surface
temperature! Fire hazard!
The crankcase heater is not an ignition source
during normal operation in an A2L-refrigerant system but could become one if
not installed properly according to installation instructions.
Ensure correct mechanical installation of the crankcase heater into the sleeve
and compressor housing. Use heat transfer paste for adequate heat transfer.
CAUTION
Overheating and burnout! Compressor damage!
Never apply power to the
crankcase heater in free air, before the crankcase heater is installed on the
compressor or when it is not in complete contact with the compressor shell.
IMPORTANT
Oil dilution! Bearing malfunction!
Turn the crankcase heater on 12 hours
before starting the compressor.
A crankcase heater is used to prevent refrigerant from migrating into the compressor crankcase
during standstill periods.
Crankcase heaters for 4M* and 6M* compressors are available in 120 V, 230 V and 480 V.
The operation of 120 V and 230 V crankcase heaters is controlled by the Copeland compressor
electronics module; this is not possible with 480 V heaters.
The crankcase heater is screwed into a sleeve
– see
Figure 36
. The recommended torque for fixing
the heater into the sleeve is 57-68 Nm.
Ensure correct mechanical installation of the crankcase heater into the sleeve and compressor
housing. Use heat transfer paste for adequate heat transfer.
Figure 36: 100-Watt crankcase heater element
The crankcase heater must remain energized during compressor off cycles. The initial start-up in the
field is a very critical period for any compressor because all load-bearing surfaces are new and
require a short break-in period to carry high loads under adverse conditions.
The crankcase heater must be turned on a minimum of 12 hours prior to starting the compressor.
This will prevent oil dilution and bearing stress on initial start-up.