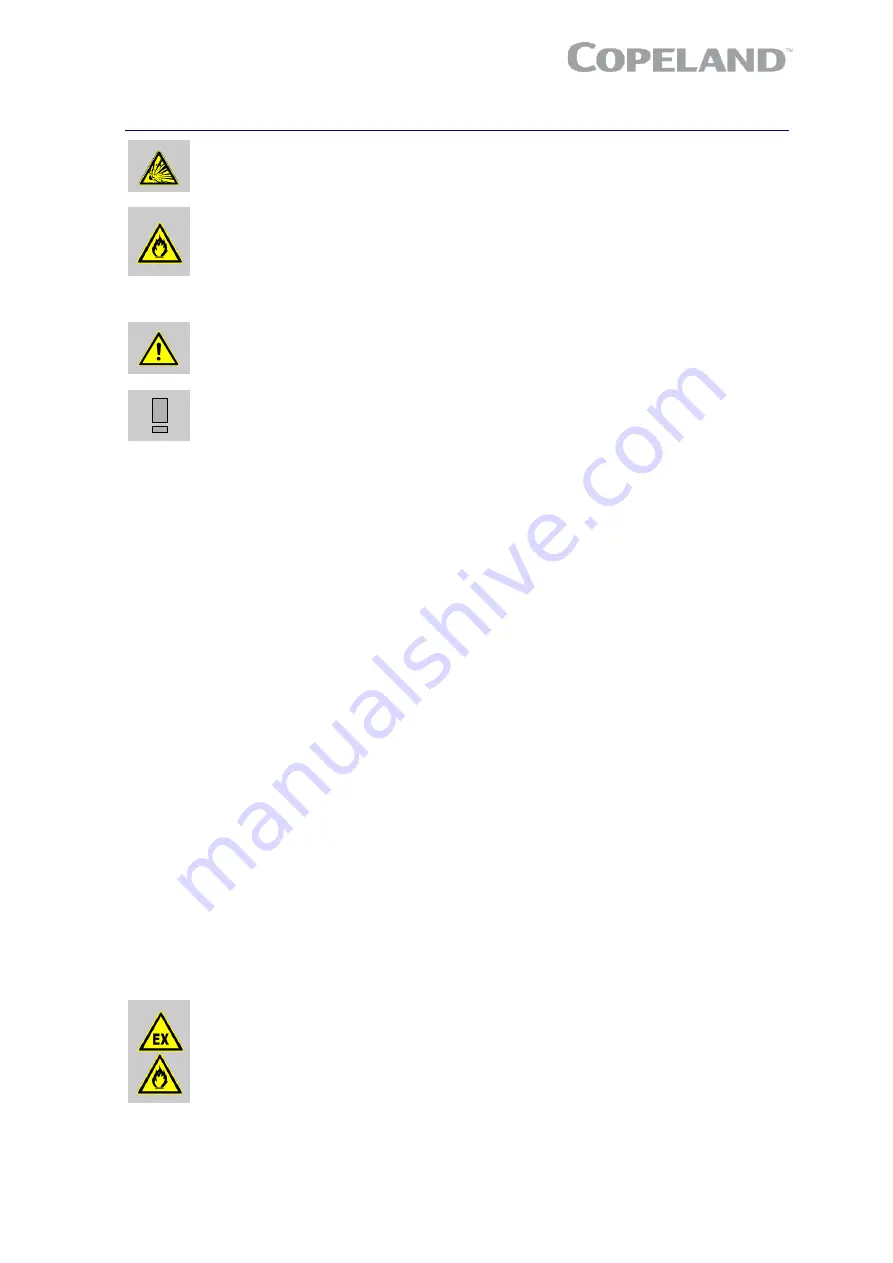
AGL_Stream_ST_A2L_A1_4M_6M_EN_Rev00
31
5
Start-up & operation
WARNING
Diesel effect!
Compressor destruction!
The mixture of air and oil at high
temperature can lead to an explosion. Avoid operating with air.
WARNING
Air/flammable refrigerant mixture! Creation of a flammable atmosphere!
Make sure the atmosphere is non-flammable before starting the system.
Ensure that the system contains only refrigerant.
5.1 Compressor tightness test
WARNING
High pressure! Personal injuries!
Consider personal safety requirements
and refer to test pressures prior to test.
IMPORTANT
System contamination! Bearing malfunction!
Use only dry inert gases (for
example nitrogen) for leak testing. DO NOT USE other industrial gases.
The compressor has been tested for tightness in the Emerson factory.
All compressors get a factory holding charge of dry air (about 1 to 2.5 bar, relative pressure). The
presence of an intact holding charge serves as a proof of quality against penetrating moisture.
When removing plugs from the compressor in order to connect a pressure gauge or to fill in oil, the
plugs may pop out under pressure and oil can spurt.
Any later modification to compressor connections (plugs, screws, etc.) can have an impact on the
compressor tightness. Always leak-pressure test the compressor after opening or modifying the
connections.
Never add refrigerant to the test gas (as leak indicator).
5.2 System evacuation
Before the installation is put into commission, it has to be evacuated with a vacuum pump. For A2L
systems, the vacuum pump and all tools have to be approved for A2L refrigerant/air mixture. The
installation should be evacuated down to an absolute pressure of 3 mbar. Proper evacuation reduces
residual moisture to 50 ppm. During the initial procedure, suction and discharge shut-off valves on
the compressor remain closed. The installation of adequately sized access valves at the furthest
point from the compressor in the suction and liquid lines is advisable. The pressure must be
measured using a vacuum pressure gauge on the access valves and not on the vacuum pump; this
serves to avoid incorrect measurements resulting from the pressure gradient along the connecting
lines to the pump.
The highest demands are placed on the leak-proof design of the installation and on the leak testing
methods
– please refer to EN 378.
The whole installation including the compressor shall be tested for tightness before the system is
charged with refrigerant. Procedure and acceptance criteria shall conform with the applicable
standard, eg, EN 378.
5.3 Preliminary checks
– Pre-starting
WARNING
Air/A2L refrigerant mixture in a potentially flammable or explosive
atmosphere! Fire and explosion hazard!
Whenever starting up a system
charged with A2L refrigerant, eg, after filling, repair, or maintenance, make
sure not to start and operate accidentally in a flammable or explosive
atmosphere.
Discuss details of the installation with the installer. If possible, obtain drawings, wiring diagrams, etc.
It is ideal to use a checklist but always check the following:
▪
no explosive atmosphere or flammable gas in the ambient, especially for systems with A2L
refrigerants;