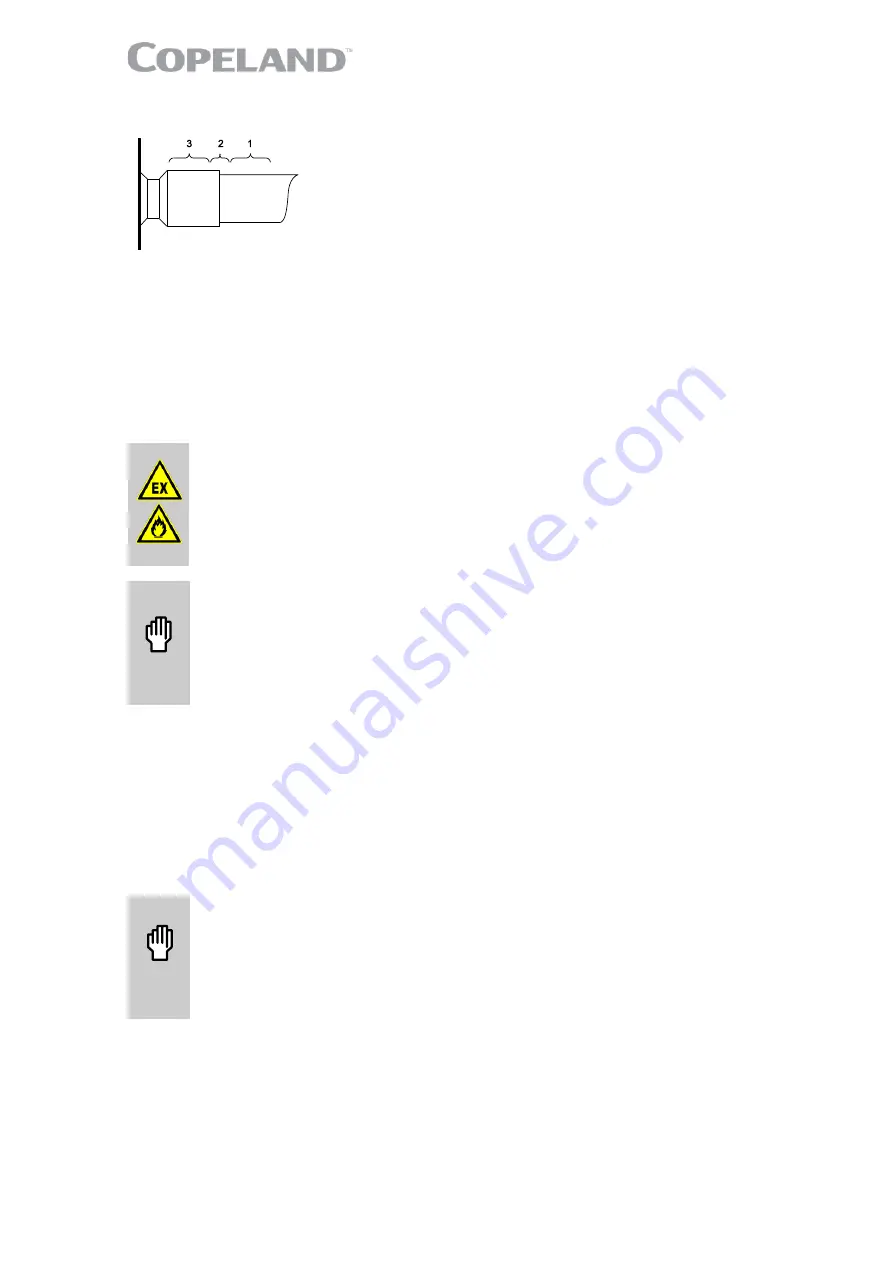
36
AGL_Stream_ST_A2L_A1_4M_6M_EN_Rev00
6.
Drain, recover and dispose of compressor oil as appropriate.
To disconnect:
▪
Using a pipe cutting tool, cut off the suction and discharge
lines in such a manner that the new compressor can easily be
re-connected into the system.
▪
Heat joint areas 2 and 3 slowly and uniformly until the braze
material softens and the tube end can be pulled out from the
fitting.
To reconnect:
▪
Recommended brazing material: Silfos with minimum 5 % silver or silver braze used on other
compressors.
▪
Due to the different thermal properties of steel and copper, brazing procedures may have to be
changed from those commonly used.
6.5 Exchanging the refrigerant
WARNING
Air/A2L mixture in a potentially flammable or explosive atmosphere! Fire
and explosion hazard!
For applications with A2L refrigerants, air/A2L mixture
in the refrigeration system must be avoided in any case. Make sure that the
system is filled with pure A2L refrigerant. In the event that the refrigerant needs
replacing, the charge should be recovered using A2L-qualified refrigerant
recovery unit and recycling bottles.
CAUTION
Low suction pressure operation! Compressor damage!
Do not operate
with a restricted suction. Do not operate with the low-pressure limiter bridged.
Do not operate compressor at pressures that are not allowed by the operating
envelope. Allowing the suction pressure to drop below the envelope limit for
more than a few seconds may overheat the pistons and cause damage to
parts.
Qualified refrigerants and oils are given in
Section 2.4.1
.
It is not necessary to replace the refrigerant unless contamination, for example due to an error such
as topping up the system with a non-condensable gas or incorrect refrigerant, is suspected. To verify
correct refrigerant composition, a sample can be taken for chemical analysis. A check can be made
during shutdown by comparing the refrigerant temperature and pressure using precision
measurements at a location in the system where liquid and vapour phases are present and when the
temperatures have stabilised.
6.6 Replacing a compressor
CAUTION
Inadequate lubrication! Bearing destruction!
For systems with refrigerant
accumulator, exchange the accumulator after replacing a compressor with a
burned-out motor. The accumulator oil return orifice or screen may be plugged
with debris or may become plugged. This will result in starvation of oil to the
new compressor and a second failure.
Remove the refrigerant and oil completely from the replaced compressor.
6.6.1 Compressor replacement
In the case of A2L refrigerant compressor replacement, the oil has to be drained out of the
compressor and the compressor should be flushed with dry nitrogen. DO NOT close the stubs with
plugs.
In the case of a motor burnout, the majority of contaminated oil will be removed with the compressor.
The rest of the oil is cleaned through the use of suction and liquid line filter driers. A 100 % activated
alumina suction line filter drier is recommended but must be removed after 72 hours. When a single
compressor or a compressor in a parallel configuration is exchanged in the field, it is possible that a
Figure 37: Tube connecting areas