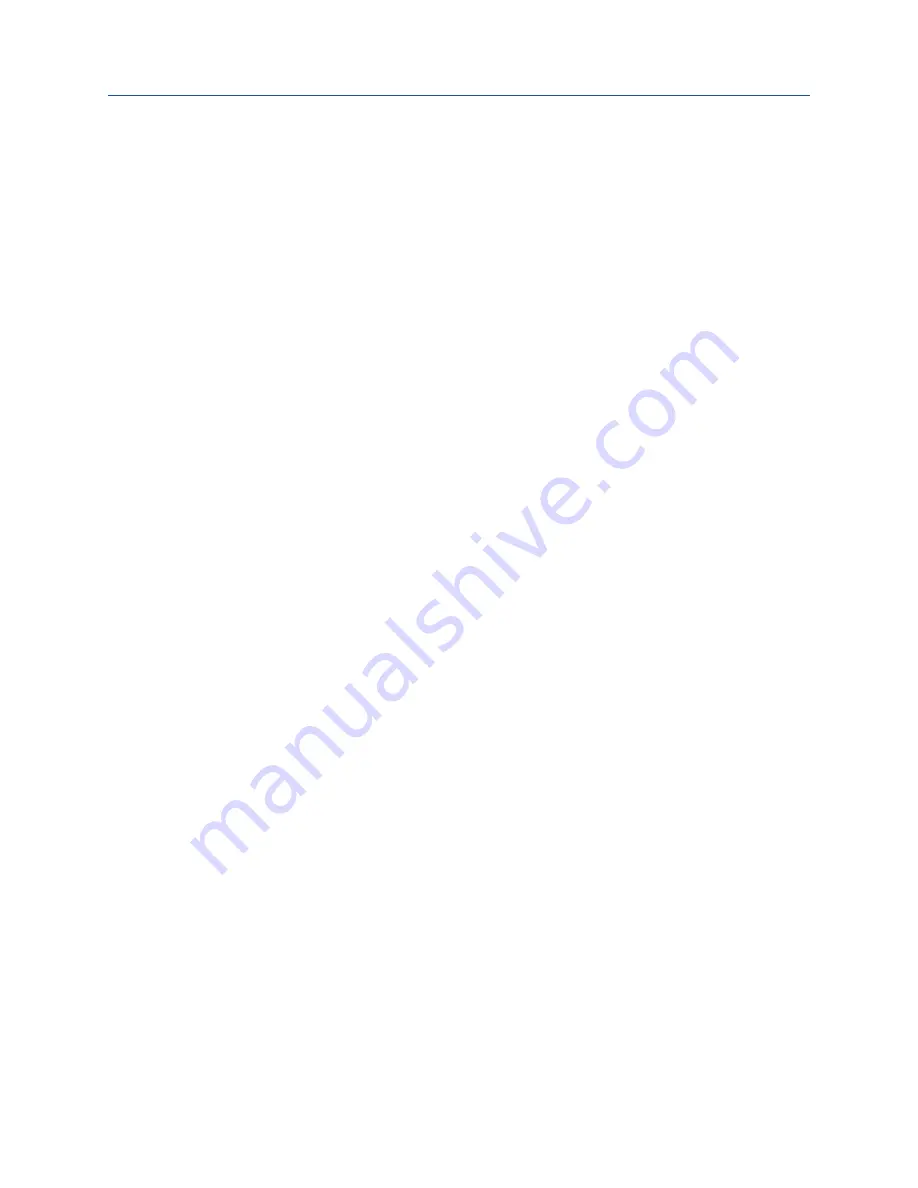
Installation, Operation and Maintenance Manual
VA-DC-000-1878 Rev. 0
December 2020
31
Section 4: Field Conversions
Field Conversions
Section 4: Field Conversions
4.1
Fail Mode Reversal (CW to CCW, or CCW to CW)
4.1.1
Remove spring module per Section 5.3.
4.1.2
Remove pneumatic power module per Section 5.5.
4.1.3
Reinstall the spring module onto the opposite end of housing (1 - 10) as it was
previously located per Section 5.4.
4.1.4
Reinstall the override cylinder assembly into spring module per Section 5.2.
4.2
Converting Double-Acting Actuator to
Spring-Return with Override Cylinder Assembly
4.2.1
Remove Blind End Cap per steps 4.2.1.1 and 4.2.1.2.
4.2.1.1
Remove hex cap screws (5 - 20), with spring lock washers (5 - 30),
from blind end cap (5 - 10).
4.2.1.2
Remove blind end cap (5 - 10) from end of housing (1 - 10).
4.2.2
If pneumatic power module needs to be relocated due to fail mode requirements
(fail counterclockwise) use Section 5.5 for removal and Section 5.6 for installation.
4.2.3
Install Power Swivel module per Section 5.8.
4.2.4
Install the spring module onto the end of housing (1 - 10) per Section 5.4.
4.2.5
Install the override cylinder assembly into spring module per Section 5.2.