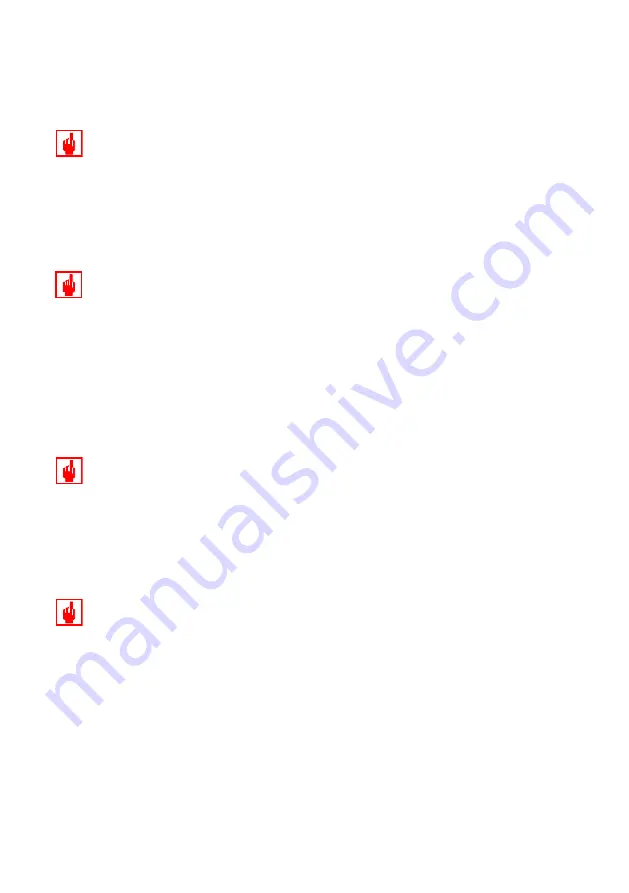
23
pH Probe
Before you calibrate the pH probe (Ch2) verify that you have two buffer solutions with values close to those found
in the plant (e.g. 7pH and 4pH). Select "pH PROBE" in the "PROBES" menu to calibrate 2 points of the probe.
Attention: this procedure assumes that the instrument is configured properly and connected to a
working probe, otherwise the results may not be reliable.
Calibrating the first point (P1)
Select "P1" in the "pH Calibration" menu and press the knob to enter the first point that is to be calibrated.
Prepare the buffer solution 7,00 pH and immerse the probe sensor.
Wait for the value to stabilise. Enter the
value of the buffer solution in the “Cal. at” field. Press to confirm.
End by moving the cursor to “OK” and
press to move on to the next step.
Warning: The value of the buffer solution may change if the ambient temperature is different from
20°C. Read the label of the buffer solution for more information. In this case the "pH Default" value
should be changed.
Calibrating the second point (P2)
Select ''P2'' in the ''pH Calibration'' menu and press the knob to enter the second point that is to be calibrated.
Prepare the buffer solution 4,00pH and immerse the probe sensor.
Wait for the value to stabilise. Enter the
value of the buffer solution in the “Cal. at” field. Press to confirm.
To end the procedure, select "OK" and press the knob. The tool will prompt the saving ("Save") of the settings.
Press "YES" or "NO" to either save or not.
Warning: The value of the buffer solution may change if the ambient temperature is different from
20°C. Read the label of the buffer solution for more information. In this case the "pH Default" value
should be changed.
ORP Probe
ORP calibration procedure involves probe’s selection with one point (P1) calibration. From “Menu
Calibration” choose “ORP probe”.
Note: This procedure assumes that instrument is correctly configured and a working ORP probe
connected and installed on system. Measurement must be performed using plant water. Otherwise
unattended results may occurr.
Calibration can be performed in two ways: the first by alignment with a buffer solution, the second by
reading the residual ORP level of the pool with the DPD1, comparison with the attached graph followed
by alignment of the pumps group. The choice of method is exclusively at the user’s discretion.
In both cases, to establish the set-point value, a check using the DPD1 or other analysis system is
necessary. The enclosed graphs provide a reference between the mV value read by the pumps group and
the quantity of residual ORP expressed in mg/litre, and are l
1) Measure buffer solution temperature and verify that it is the same printed on solution’s label.
2) Remove protective cap from probe and wash probe’s tip into water. Then dry it by shaking up to the air.
3) Set “Cal. at” value to match buffer solution value then put probe’s tip into buffer solution and wait until
instrument shows a stable reading value (mV field).
4)Move cursor on “OK” and press wheel ton cofirm the new calibration value. If calibration process fails the
instrument will show “CALIBRATION FAILED”. Repeat procedure otherwise move on “ESC” and press
wheel.
Attention
Attention
Attention
Attention
Summary of Contents for LOTUS AIR 10
Page 40: ...40 Logical working scheme...
Page 42: ...42...