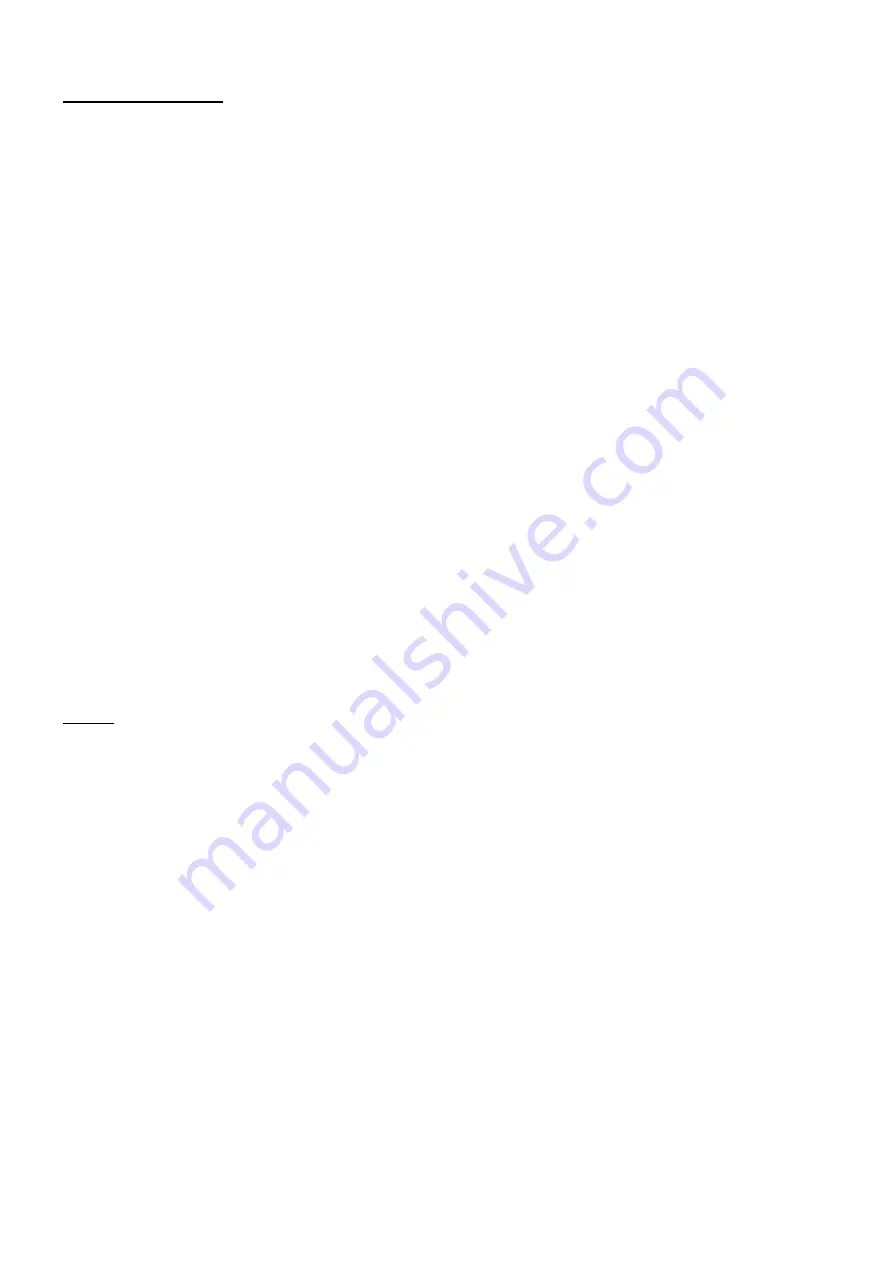
SX - Operating- & Service instruction - 8 074 667.02/02 - page 7
Commissioning
Before start of commissioning please notice the following items:
1. Check the correct connection of mains- and motorlines.
2. Check if the control lines are connected with the correct terminals.
3. Check if the frequency inverter is correctly grounded according to regulations and mounted vertically to a wall.
4. Remove all stray pieces of wire, solderless terminals or other objects left from wiring work.
5. Check if all screws and terminals are fixed.
6. Check if the motor is specified for the defined frequency range in particular for the maximum speed.
7. For optimum adaptation of the frequency to the motor see parameter A97, Auto-Tuning.
Factory default setting (Initialisation)
At delivery all frequency inverters of the series ELVO
vert
SX are preset to factory default. The devices can be reset to this
basic setting any time.
To do so, proceed the following steps:
1. Switch the power on (display 0 0 0) and press the FUNC-key once (display d 0).
2. Select parameter F14 by repeatedly pressing the arrow keys.
3. Press the FUNC-key once. Parameter A0 is displayed.
4. Select one of the parameters C0 - C7 (corresponding to the terminals 1- 8, e.g. C1 = input 2) via repeatedly pressing
the arrow keys and press key FUNC once.
5. Put in parameter 7 under this parameter by usage of the arrow keys (terminal function STN = factory default setting)
and store the input via pressing the FUNC-key once.
6. The terminal which is selected by this procedure is now used to activate setting to factory default. Connect this terminal
to terminal P24 and switch off power. Wait as long as the LED which monitors the link voltage is switched off.
7. Switch on power again and wait for appr. 6 sec.
8. Disconnect the link between the terminal for factory default setting and terminal P24.
9. Switch off power again and wait until the LED which monitors the link voltage is switched off.
Commissioning via built-in keypad
Remark:
Remark:
The inverter needs “Pulse unlocked“ to rotate the motor. Terminal 4 is from manufacturing preset with “Pulse unlocked“
and therefore has to be connected with P24 via a linking wire. Additionally a wire to link PLC with CM1 is required.
1. Switch on the power; the power-LED on the operator panel is then on (display shows value of d 0).
2. Select parameter F4 by repeatedly pressing the arrow keys. Press the FUNC-key. Now you can select the required
direction of rotation by usage of the arrow keys (F = forward, r = reverse). Store the input by pressing the key FUNC.
3. Select parameter F9 via pressing the arrow keys and put in 00 on this parameter position (see parameter F9).
4. Now selecet parameter F2 and adjust the set frequency by usage of the arrow keys.
5. Start the inverter via the RUN key.
Summary of Contents for ELVOvert SX
Page 1: ...8074667 02 02 ELVOvert SX Operating Service Projecting Mounting Connecting...
Page 4: ...SX Operating Service instruction 8 074 667 02 02 page 2 Notes...
Page 28: ...SX Operating Service instruction 8 074 667 02 02 page 26 Notes...
Page 52: ...SX Operating Service instruction 8 074 667 02 02 page 50 Notes...