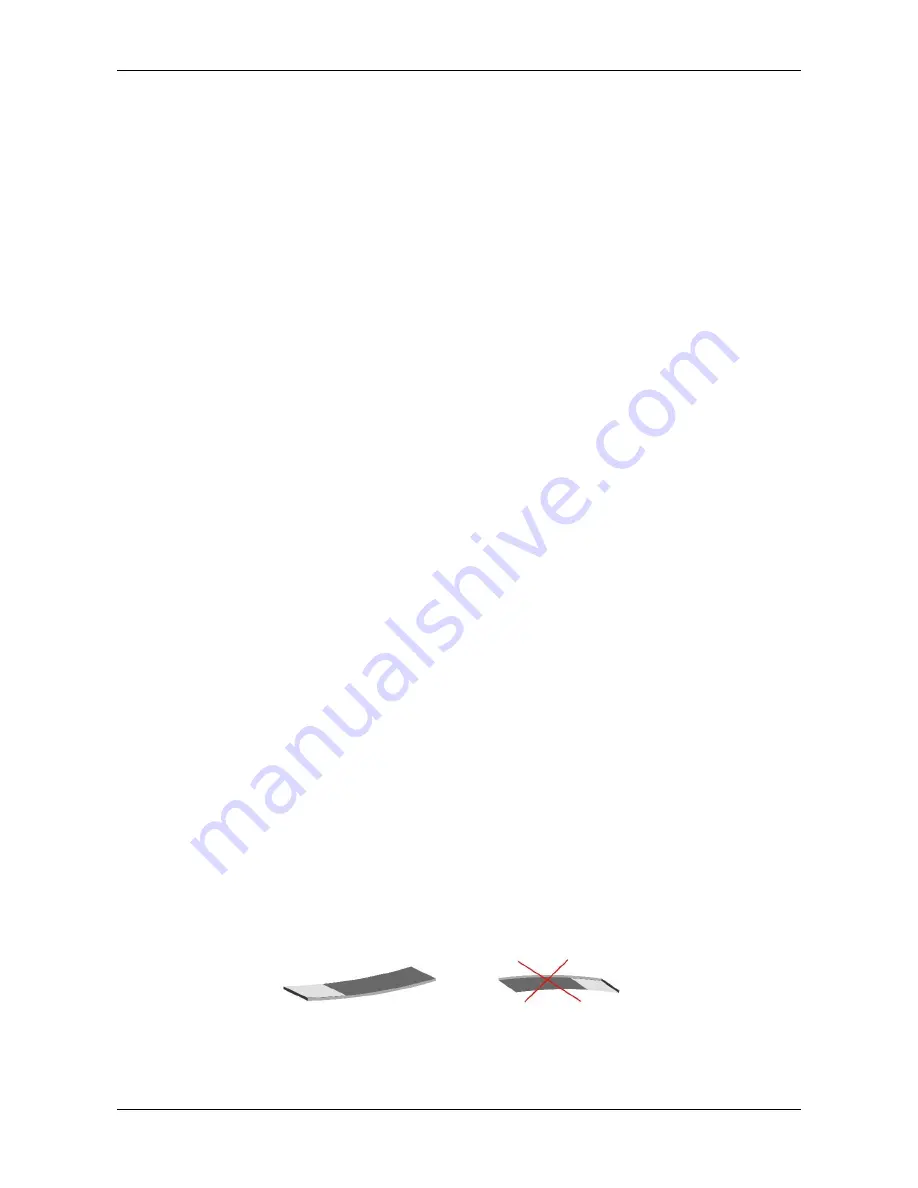
6. Calibration
© ElektroPhysik
MiniTest 2500 - MiniTest 4500
24 of 73
6. Calibration
6.1 General notes on calibration
The MiniTest 2500/4500 series offers a number of calibration methods to meet the individual
requirements of various applications, procedures and industrial standards.. When a batch is being
created you can select a suitable calibration method for this batch. The calibration can be carried
out immediately after you have created a batch or at a later time in measuring mode using the
„CAL” key. The calibration method can be changed as long as no readings are stored in the
currently active batch.
A calibration is made in the currently active batch and is directly related to this batch.
To ensure an optimum calibration, the following points should be observed:
Correct calibration is vital for accurate measurement. For calibration, a sample similar to the
later object to be measured should be used, i.e. both, calibration sample and the object to be
measured should be of the same shape and geometry. As a rule, you can say that the more
similar the calibration sample and the later object to be measured are, the more accurate
calibration and thus accuracy of readings will be.
Make sure the calibration sample and the later object to be measured have same
characteristics such as:
·
identical curvature radius of surface
·
identical substrate materials (such as magnetic permeability, electrical
·
conductivity; in the ideal case, they should be made of the same material)
·
identical substrate thickness
·
identical size of measuring area
Before starting calibration, make sure the calibration spot, the sensor tip and the calibration
standard are clean. If necessary, remove any built-ups such as grease, metal chips, etc. Any
impurities might affect calibration and lead to erratic calibration.
Make sure the calibration position and the measuring position are always the same, this
applies especially for measurement on small parts and measurements at edges and
corners.
Keep away from strong magnetic fields during the calibration procedure.
For maximum accuracy of calibration and later measurements, choose the thickness of
calibration standard within the same thickness range as the later measuring sample.
For measuring thick non-ferrous metal coatings on steel or ferrous substrates according to
the magnetic induction method (using sensor type F 1.6, FN 1.6, F3, F10 or F20) a multi-
point calibration must be carried out. The thickness standards must be of the same metal as
the later object to be measured.
If using calibration foils, make sure they are placed in plane position on the substrate material.
Any air gap below the foils must be avoided as this would lead to erratic readings. If the foils
are curved, make sure to place on them on the substrate as shown below (see illustration).
The precision thickness standards must be handled with care. Any wear-and tear of the
thickness standard will be reflected as erratic calibration value. Do not fold calibration foils.