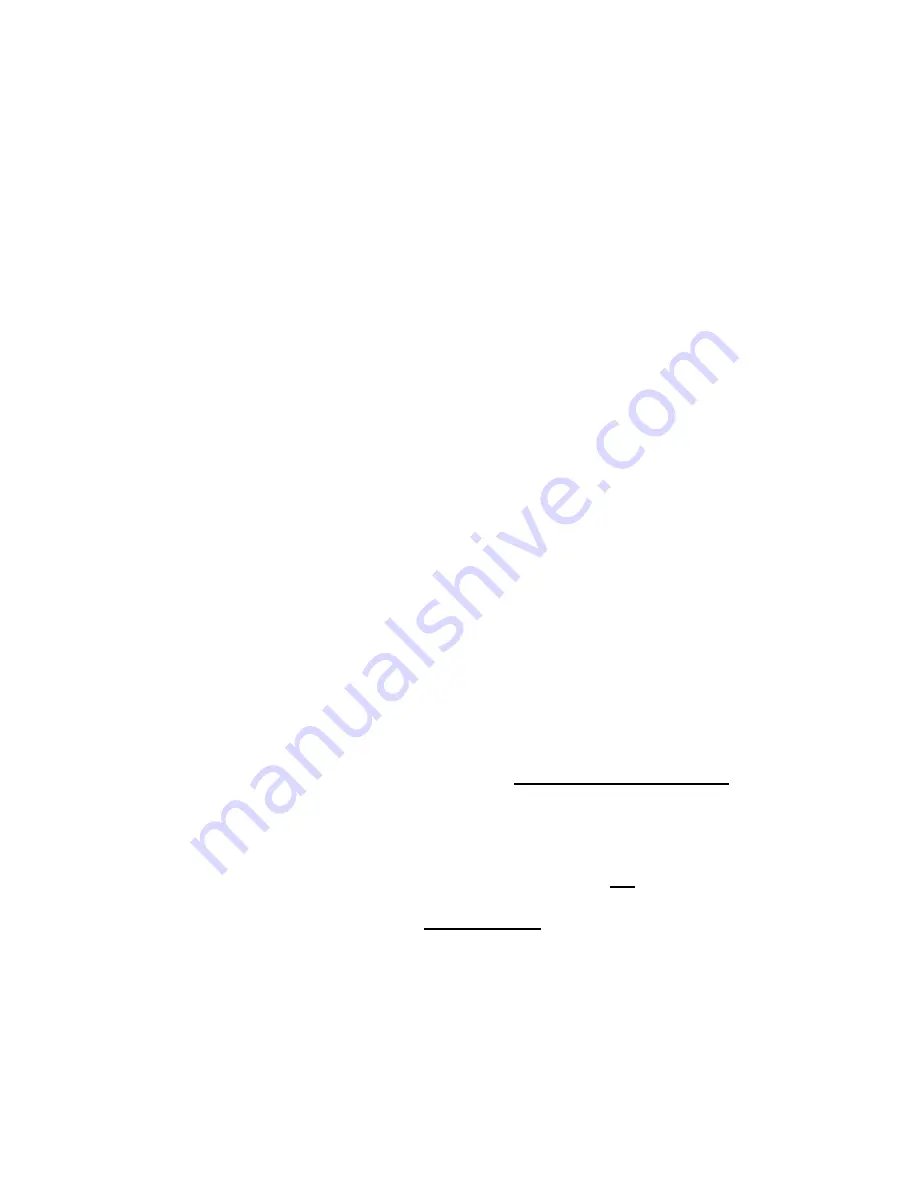
________________________________________________________________________
XDI200 Manual Version 0.1
- Page 18 -
©2017 Electromotive, Inc.
3.3.6 Camshaft- & Distributor-Mounted Trigger Setups
While crankshaft mounted triggers are preferred, it is sometimes easier to install a
camshaft- or distributor-mounted trigger wheel. For these cases in which the trigger wheel is
spinning at
half the engine speed
, a 120(-4) tooth trigger wheel is necessary. This wheel has
two sets of two missing teeth, spaced 180 degrees apart. As such, the input to the
XDI200
is
identical to that of the crank-mounted 60(-2) tooth trigger wheel. Electromotive offers 120 (-4)
tooth wheels in 3.25” and 2.75” diameters.
It is often easy to use an old distributor rotor to serve as the mount for a 120(-4) tooth
trigger wheel. A simple nonferrous bracket would need to be fabricated to hold the sensor. The
3/8” chisel point sensor (PN: 250-72219) must be used on 120(-4) trigger wheels. As such, the
bracket for the sensor should use a clamping arrangement rather than a setscrew to hold the
magnetic sensor.
Just like the crank-mounted trigger, the distributor/cam-mounted triggers
require the sensor to be aligned with the trailing edge of the 11
th
tooth after the two
missing teeth when the engine is at TDC #1.
The same tolerances that apply to the
crankshaft-mounted trigger wheels (
Table 1
) apply to the camshaft-mounted trigger wheels as
well.
A Note on Engines with High-Overlap Camshafts:
If your engine is equipped with a camshaft that has early intake valve openings or very
long duration, you may experience backfiring through the throttle during starting. This is caused
by the intake valves beginning to open on the exhaust stroke. Since the spark plugs fire on both
the compression and the exhaust strokes, the spark on the exhaust stroke may cause unburned
fuel in the intake manifold to ignite, resulting in a backfire.
To remedy this situation, advance the “mechanical” timing by manipulating the
DFU “A”
Trigger Wheel TDC
Parameter. If your crank sensor is aligned with the 11
th
tooth of the trigger
wheel at TDC #1, setting the Tooth Offset to a number LOWER than 11 will
add
mechanical
advance. If the number “10” was set for the Tooth Offset, the mechanical timing would be
ADVANCED by 6 degrees (6 degrees per tooth). This would require that you subtract 6 degrees
from the values in your ignition advance table in WinTec to obtain your desired advance value.
That is, the timing table will have to read 30 degrees in order for the engine to operate at 36
degrees advance. See
the Tuning Guide Section
for more details.
3.3.7 Individual Cylinder trim application
– Cam Synchronization
When individual cylinder advance angle trimming is desired, a once-per-engine-cycle
synchronization, or “sync,” pulse must be received by the ECU. Typically, the sync pulse is
generated by the installation of a 1-notch (or 1-tooth) trigger wheel onto the camshaft. A Hall
effect sensor is used as a triggering method. With this method, the tooth must pass by the
magnetic sensor between 180
o
and 6
o
before TDC Compression (not exhaust) of the number one
cylinder. See
Figure 11
for installation details.
The XDI200 will only trigger off a rising voltage during the synchronization period
(between 180
o
and 6
o
BTDC compression)
. A rising edge occurs when the metal on the cam
trigger wheel becomes closer to the sensor. See
Figures 8 and 9
for representative examples
and different cam trigger wheel designs, and their rising edge location.